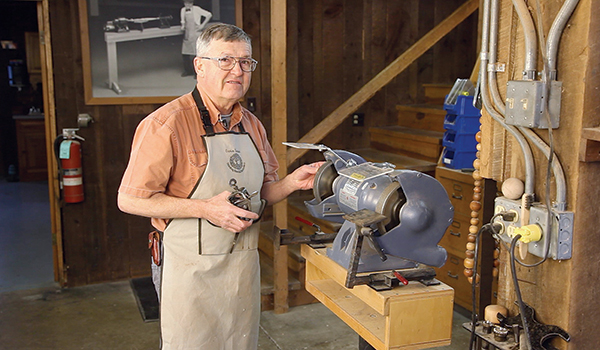
Cubic boron nitride grinding wheels (CBN for short) will take your ability to sharpen tools to the next level.
In my lifetime, I have witnessed some groundbreaking advances in sharpening of turning tools. In my boyhood, many turners sharpened their tools on oilstones, not owning a grinder at all. It was slow and fussy. Fortunately, my father’s shop had several grinders, but we did all of our grinding of turning tools freehand. As I have often stated, freehand sharpening is turning turned inside out: turning’s evil twin, so to speak.
Compounding matters, we only had carbon steel tools, which required constant quenching in water, or they overheated and lost their temper. (So did my father.)
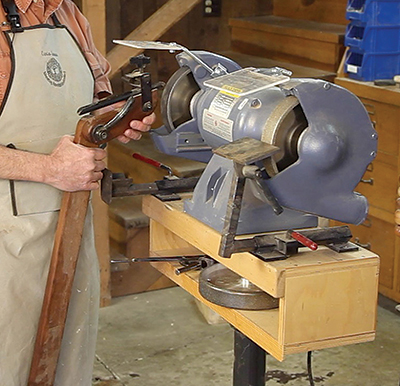
In 1982, Jerry Glaser introduced the first turning tool sharpening jig, which separated turning from its evil twin. It positioned the turning tool perfectly against the grinding wheel so that the turner only had to sweep the edge smoothly against the wheel. There was a minimal learning curve and now anyone could sharpen a tool. Tim Clay based his Wolverine and Vari-Grind™ jigs on Glaser’s design.
With all this development, the only weak point in the system these days is the grinding wheels themselves. Grinding wheels are akin to pottery with sharp grinding particles mixed in. A new grinding wheel is not round and has to be trued once mounted on the grinder. I’ve addressed this previously in my video on bench grinders (below).
VIDEO: Sharpening Turning Tools with a Bench Grinder
CBN Wheels: The Next Step
Now we have the final step in the evolution of sharpening turning tools. It is cubic boron nitride grinding wheels — CBN for short. A CBN wheel differs greatly from a standard grinding wheel: it is a machined disk of metal, either steel or aluminum, that is coated with cubic boron nitride crystals. The resulting wheel is perfectly round because it was turned from metal, unbreakable (it cannot explode) and very well-balanced. Many are dynamically balanced; you will see drill holes on the side that bring the wheel into balance. The result is that the wheel runs absolutely true with no vibration whatsoever.
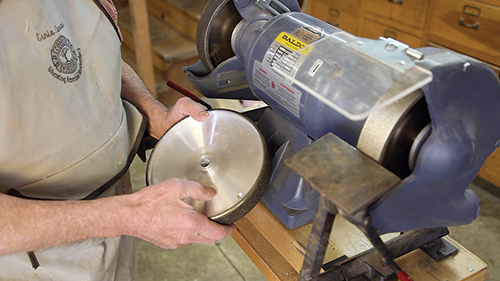
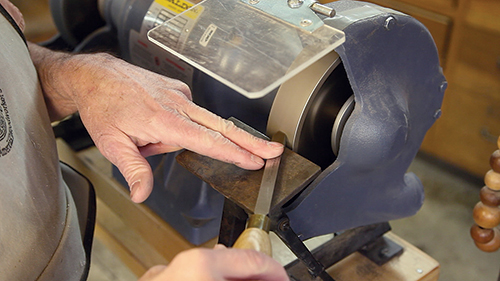
Boron nitride is a compound of boron and nitrogen with a chemical formula of BN. When its crystalline structure is cubic, its abrasive cutting qualities are analogs to diamonds. The only harder abrasive particle is diamonds, but CBN will hold its integrity at higher temperatures than diamonds. The really juicy plum in the CBN pudding is thermal conductivity. The most common material used in grinding wheels for tool sharpening is aluminum oxide, which is not a good thermal conductor. Because of this, 90% of the heat from grinding with aluminum oxide ends up in the workpiece. CBN is a good conductor of heat, so only 40% of the heat goes into the tool being ground. The rest goes into the wheel, which, being metal, is a good conductor of heat. Thermal properties are so good that there is very little sparking when grinding with CBM and the tool is usually cool enough to touch. Because of this superior thermal conductivity, CBN will dry grind tool steel where diamond wheels will be ruined if used dry.
Pros and Cons
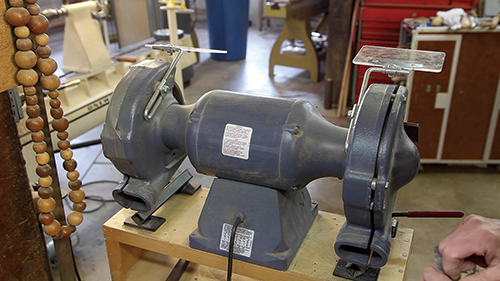
There are some drawbacks to CBN wheels, the first being expense. The typical 6″ or 8″ wheel costs between $150 and $250. The other drawback is that they will only grind hardened tool steel: mild steel will ruin them. They really work best on high-speed steel but will do fine on carbon tool steel that is Rockwell C scale 55 or above. I feel the expense for even one wheel is justified by the fact that most people will never need to replace it and a good aluminum oxide wheel costs between $50 and $75 and wears out. A solid compromise is to keep a 46-grit aluminum oxide wheel on the left side of your grinder and mount an 80-grit CBN wheel on the right. Do your mild steel and rough tool grinding on the aluminum oxide and final tool grinding on the CBN.
Because there is no danger of the wheel exploding, you can mount CBN wheels at a higher level, giving better visual acuity. If you are also running an aluminum oxide wheel I would not do this, however.
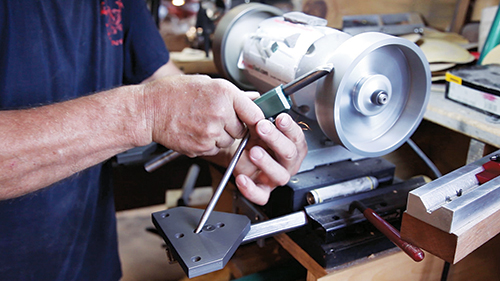
Using CBN wheels is quite a different experience. There is no vibration, there is no shower of sparks and there is not even really loud noise. Only light pressure against the wheel is required. It is all very sedate, and the finished grind is performance art. On scrapers the burr is uniform, working as well as, or better than, one raised on an aluminum oxide wheel. I even grind carving tools on the 80-grit CBN without burning them.
The final problem with CBN wheels is that most will not fit inside the grinder’s guards. Most turners are simply removing all guarding on the side that has the CBN wheel. This may be OK because there is no danger of it exploding. Being cautious, I was able to use the guards on my 8″ Baldor by putting some washers between the two halves. This leaves a small opening but is still safer than no guards at all. It also allows me to use the rests that came with the grinder in addition to the Wolverine and Vari-Grind supports.
If you use a CBN wheel, you’ll appreciate the amazing quantum leap forward that it is.