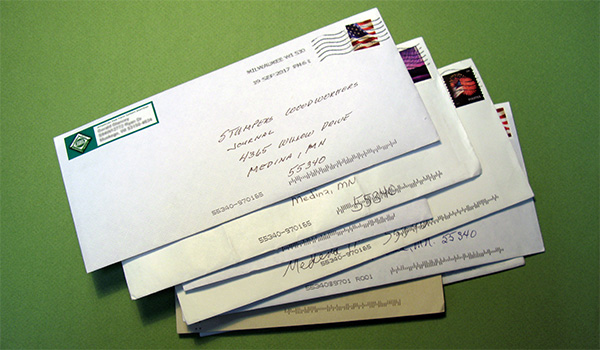
Cookin’ Up Ideas for Cookies
We’ll start with the cookies, and the winning ideas our readers cooked up for alternate uses for Rockler’s Bench Cookies™. Here, in order, are the first, second and third place winners. – Editor
“For pushing large panels through the table saw, a couple of Bench Cookies attached to either end of a handle (visualize a telephone handset) would be perfect, lots of control.” – Phil Gilstrap
“Place under the Christmas ham for easy slicing.” – Frank Speyerer
“I also use my Bench Cookies for: a) elevating a workpiece/project for clamping, b) raising furniture for staining/painting (I first cover the Cookies with wax paper).” – Charles Mak
And a couple of other suggestions. – Editor
“Use them as an excuse to clean off a portion of a bench top….” – Sheldon Grand
“When not in use, leave them out on the coffee table and tell your friends you used to play hockey for (insert favorite team here).” – Riley Grotts
Clarifying Therming
A portion of our Feedback in this issue comes from the subject of our previous issue’s Today’s Woodworker department. Denise DeRose gives a more precise explanation of the “therming” technique she sometimes used in creating her turned wooden handbags. – Editor
“Therming is an ancient technique where several pieces of wood are turned at the same time mounted parallel to the lathe bed. You can kind of get the picture if you imagine having a barrel mounted horizontally on a lathe. Barrels were not made this way, though. Spoons and table legs were made in this manner. You turn one side of several pieces at the same time, then flip the pieces over and turn the other side. You can turn as many sides as you wish. When I use the technique for turning purses, I turn the two flat sides of the bag using the therming technique, and then band saw the edges. I then have to cut the pieces in half lengthwise, and then hollow out the inside by hand or using a Forstner bit. Pretty hard to explain. Hope this is clearer, though.
“Also, would be great when discussing the 30 inch bowl if you would mention that I made it for an order with a friend. [turner Michael Serpa]” – Denise DeRose
Giving Thanks for Woodworking
Rob’s Thanksgiving time editorial prompted a reflection from this woodworker, who gave thanks for the craft. – Editor
“Today I had the extreme pleasure of delivering an antique bed to a friend. On a recent visit she showed me the bed. The side rails were missing and the slats were resting on a metal frame. It was unsafe to use. She asked if I could restore it so that she could use it in her guest bedroom. I had done a little repair on some furniture but never on a bed over 100 years old! I made the side rails and they turned out very well. I also washed it down with a red oak stain (Minwax) mixed with mineral spirits. It looked almost new and not ‘refinished.’ When I delivered the bed, our friend was overwhelmed! For me, it is the gift of giving such pleasure that is the real reward for being a woodworker. So, we woodworkers truly have much to be thankful for, especially the gift of woodworking.” – W.F. Osburn
Spontaneous Fire Starters
In our last issue’s Q&A section, a new woodworker asked whether the warnings about spontaneous combustion related to finishing rags reflected a real threat. Others with more experience are here to say that, indeed, it does. – Editor
“We were once finishing a historic building floor with only a boiled linseed oil rubdown. I repeatedly warned the contractor to let the rags dry stiff and only then gather them all and put into a galvanized garbage can with a tight-fitting lid, outside. Next morning as I came on the job, the contractor said, ‘You better look at this.’ In the parlor floor was a perfectly round, 20″ diameter, charred edged, hole through the 1″ thick oak floor. Peering down through the hole, eight feet below, the can (with lid still on tight) could be seen sitting on the brick basement floor. When they say finishing rags can spontaneously combust, believe it!” – B.H. Rucker
“The rag can still spontaneously combust if there is enough volatile matter, etc. Put the rag in a metal container! Combustion is governed by the available air – if you restrict the air, you limit how much can oxidize. Any metal, sealed container will do – even a metal cookie jar.” – Don Dziubakowski
“You must double check your area after using!!!!! I have a safety can and have had rags burn in there. I usually set it outside. You can’t be too careful!” – John Crouse
How Low Should the Blade Go?
Another Q&A in our previous eZine asked what the correct height setting should be for a table saw blade. This is an area where our correspondents had differing opinions. – Editor
“When I first encountered a woodworking teacher, we were told to let the blade gullets clear the wood [that was 50 years ago]! I recently attended a seminar by the regional Freud rep, who advised: raise the blade to one half the gullet dimension above the wood. His explanation was it gives the blade enough clearance to clear the chips and if it hits your finger, it doesn’t cut it off.” – Don Dziubakowski
“As a veteran of 35+ years in the power tool business, I was taken aback by the answer to this question. You state that the best cut & the most efficient cut is with the blade up as high as it can go. Au contraire. With the blade in the highest position, you will have the fewest teeth in the workpiece at any given time. With the blade at approx. 1/8” above the workpiece you will have the most teeth in the workpiece at any given time. This was always one of the major selling points of a radial arm saw. No matter the thickness of the workpiece, the blade was just through it. You didn’t have to adjust blade height as work pieces varied.” – Tom Gould
Blade height is one of those questions that will likely never be answered to anyone’s satisfaction. Here are a couple of things to remember: The saw blades that we are using today are so superior in terms of their design and their performance that we are in a different world than we were 30 or 50 years ago. How blades cut through material and exit the dust from the gullets is a fine science. My buddy Ian Kirby says that putting these blades on a contractor’s or benchtop table saw is like putting a diamond in the arse-hole of a goat. While I don’t understand that comment in any practical terms, it is a comment on the quality of the saw blades. Depending on the cut I am making, I will have the blade position very high (if I am making a cut in material that splinters easily), to the position that the Freud guy was advocating.
My personal opinion, and I have put it in print, is that more important than a blade guard is a solid riving knife system. A robustly made riving knife — one that keeps its distance to the saw blade and rises and falls with the blade, will save more fingers than any other piece of safety equipment by preventing 99% of kickback events. It is my opinion that in most cases, fingers get tangled up with saw blade when kickback occurs. The good news is that new regulations are now forcing table saw makers to include an easy-to-use riving knife system with any new table saw. (This has been a law in Europe for 20 years or so now.) – Rob Johnstone
A Lesson in Map Reading
The phrasing in last eZine’s Industry Interview about Rob Doyle importing burls “from Australia and Tasmania” prompted our friends from down under to provide a geography lesson. – Editor
“Just read your latest eZine: good stuff, but the article on Bad Dog Burls was a little surprising. Apparently Tasmania is its own country now! Although we make fun of them on the mainland, Tasmania is still part of the Australian Nation.” – Bryan McGrath
“Although Tasmania is a little triangular island to the southeast of the ‘mainland’, it is still part of Australia and has some magnificent and rare woods. My favourites are blackheart sassafras, blackwood, and Huon pine (when I can get it at a reasonable price).” – Roger Forrester