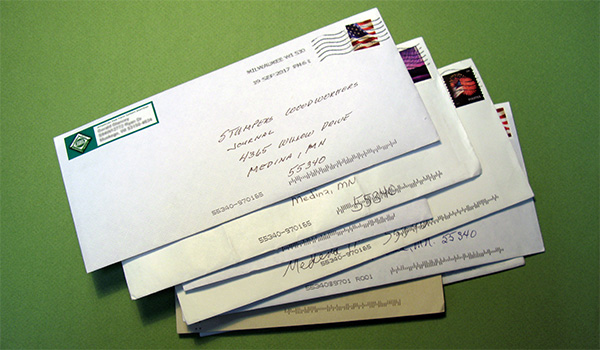
Do Real Woodworkers Use CNC?
That’s the question Rob posed in his editorial last time out (actually, he used even stronger language, wondering if using a CNC in the woodshop was “cheating”). It seems that eZine readers have a few opinions to share on this topic. – Editor
“If you use a CNC machine and palm your work off as handcarved, then yes, it’s cheating. If you declare ‘Look what I can do with my new toy…I mean tool,’ then no, it’s not. We should do with woodworking whatever suits our purposes and desires. Let’s just not misrepresent ourselves and take credit for a skill we haven’t developed.” – Rich Bonvouloir
“Yes, to the same degree that stencil work is when painting. Or that pantographic routers are (which this is just a fancy version of, after all). Heck, what about the fancy router-bit (and molding-router blade) profiles — aren’t they cheating compared to using a sequence of simpler shapes? For that matter, aren’t purchased moldings and rosettes and inlays a cheat? How does that differ from hiring someone to do some hand-carving for you? As always, it’s a difference in degree, not in kind. And in the end, it’s a difference in style. Is your concept of the piece the effect it has on people when they see it, or the effect when you can say ‘I did that?’ For most of us it’s a mixture of the two, and the percentage varies per person and per piece.” – Joseph Kesselman
“I don’t think I would consider it cheating. It reminds me of my first programmable calculator. My teacher at the tech institute said we could use them if we wished. He had a guy in the previous semester program it wrong and failed the final. You have to know how to do it manually before you can program successfully.” – D.W. Taylor
Not everyone was happy with the entrance of CNCs into the home workshop. – Editor “Congratulations on your purchase of a new CNC router. You have now taken the first step in evolving from a woodworker into a computer programmer.” – Matt Mattera
“To me, CNC routing isn’t woodworking. It’s OK for a factory, but for the ‘home enthusiast’ or the custom cabinet or furniture maker, it’s not ‘playing by the rules.’ It’s having a combination computer and machine do what you are supposed to do. There’s no woodworking skill level required. Woodworking takes years to learn and, like you said – you learned the CNC in three days. My work isn’t perfect, but I’m proud of the effort. It’s not the same when the machine does the work for you.” – Barry Saltsberg
“I feel this puts woodworkers in the same category as women with automatic embroidering machines. Assuming we’re dealing with hobbyists: why do you want to have a machine take over your hobby? Doesn’t the joy of woodwork come from saying, ‘I did that,’ not from saying ‘I’m rich, so I bought a machine that does it for me.'” – Laurie Power
“If you are a real woodworker in blood and soul, there is nothing to get excited about, because after you have created something with this machine are you going to dare to say, ‘I have made this with my two hands’? When you as a woodworker make use of this machine, you cannot claim any credit for the product.” – Sarel Jooste
“I don’t think that you are truly ‘woodworking’ when you put a pattern in a machine, program it, and watch it do the work. I get my pleasure in trying new techniques, especially with hand tools, and succeeding/failing, but at least trying. I just don’t see how CNC routers can be classified as ‘woodworking.'” – Steve Busch
Others thought of it more as a natural extension of changes in technology, tools — and technology in tools. – Editor
“I consider myself an advanced novice woodworker. I feel good about my work, but would never try to sell it. I do not think CNC routing is cheating any more than using a palm sander instead of my #4 smoother. Carving is a different skill and many woodworkers have not attempted it or mastered it and if there is a tool available to help complete a project you have no skills at, then go for it if you can afford it.” – Bob Cornett
“I started out on Timex/Sinclair, then Commodore Vic 20! I even had experience coding on a 4 bit processor. To the question at hand: Is it cheating to use a CNC machine in our workshops? Hmph! Is it cheating to use a table saw or a band saw instead of a hand saw? Is it cheating to use a router or a random orbit sander? Is it cheating when my wife uses a sewing machine instead of hand sewing? Is it cheating when she uses a dishwasher? Certainly not! Machines extend our hands and technology extends our machines. I’m not ashamed of my little CarveWright or my humongous Legacy Ornamental Mill Model 1200 EX.” – Don Butler
“If every new innovation was considered cheating, and no one cheated, we’d be nowhere. The nail gun is a good example – for framers and roofers it’s just about eliminated the need for a hammer. In that case, the objective is not to drive a nail; it’s to roof a house or build a wall. In the same sense, the use of the CNC machine is not to just cut materials in a very precise manner; it’s to speed you on your way to your final product.” – Paul Bailey
“I’ve been a Commercial artist for 40-some years. When I graduated from La Roche College in Pittsburgh, Pennsylvania, I started my career using the tools of the trade available then. Pens, ink, pencils, paintbrushes, paint, T-square, triangle, French curves, art board, drafting tables and drafting arms, X-Acto™ knives, rubylith…the list goes on and on. Today, I have a desk with a 27-inch Macintosh computer and a second auxiliary 19-inch monitor. ALL of what was done years ago by the hands of craftsmen is now accomplished on the computer. We laid down our hand tools and accepted the new ‘tool,’ the computer. I viewed it as just another tool to do my work with. I made life much easier at work and at home. The use of a CNC router in the home shop should be viewed as just another tool from the advancements available with the computer. And after all, we still need the ability to program the system to build our projects. As I tell people I work with, the computer doesn’t make you an artist, the artist can make the computer a useful tool in his work.” – Paul A. Germeyer
“I have been working with wood for about 30 years. In my case, I look at the all the tools I have as I did when I was developing test equipment in the electronics industry. For me, it is important to be able to use ‘all’ versions of tools, old and new, to accomplish your ‘prototype masterpiece.’ You cannot live with technology alone, but you should understand it and implement new technology if and when the need arises. To me, technology doesn’t take away from woodworking, but it assists you at the proper time.” – Gus Gonos
Some thought a CNC was more appropriate for a professional shop — or at least for a hobbyist who was also making things for sale. They addressed issues pertaining to money, and to time. – Editor
“One can appreciate the way of doing the carving and sign making with the computer, but where is the glory? Yes, some woodworkers can also run a computer, but does that improve the quality or just quantity? For production, it may be fine, but for the home shop, take your time and have a coffee break.” – Gary A. VandenBerg
“There are always applications that fit the needs of the woodworker and then there are the nice-to-have tools that are usually way too expensive for us home shop guys. My day job involves programming, setting up and operating a CNC milling machine, CNC lathe and a CNC turret punch. These machines, of course, are way, way too expensive for the home shop and way too sophisticated for the casual user. We have had these machines in our Model Shop for about 10 years. Before we purchased them, I told my boss that I didn’t think we would really use them all that much and the cost would not be justified. Boy, was I wrong. Now, every chance I get to put something in any of the CNC machines, I’m doing it! What a time saver. There’s accuracy, speed, repeatability, etc. The point is, it seems to depend on what kind of woodworking you actually do in your shop. Is it a hobby or do you make money from the things you make? If you make money, then it is time to start thinking about the investment. Maybe it will pay for itself in the time you save. Once the machine is running it’s like having another set of helping hands.” – Bill Miller
“I, like you, am an old computer geek, but I think I could get the hang of the CNC. I have thought about one many times, but then the big question arises. Is it really worth the money? There are only so many things you could decorate with a CNC for your own use, which then leads to the next level which would be making items to sell. That means going to flea markets and such to sell the items you made with your $4,000 CNC. That seems to me to be a lot of items and a lot of flea markets. I think I will just buy a couple of really good traditional tools for the same money and trade my flea market time for shop time.” – Loren Estes “Is CNC routing for the home workshop? Well, maybe for the person who is making crafts to sell — after all, from what I see, it is too much work to program it and set up the workpiece to do one thing. Tell me if I am wrong? I have thought about getting one, then I ask what for? While it would be nice to have the ability to put carved objects (I am not a carver) into a workpiece, is it worth it?” – Dwight Doane
“Seems like a CNC router is overkill for the home shop unless you do a lot of elaborate carvings. It seems that there are so many other accurate power tools out there now – routers, Festool’s Domino. There are also so many plans for jigs to help increase accuracy. It seems that the money might be better spent on upgrading your table saw to a top-of-the-line saw or your jointer. All those tools are very basic and accuracy on those tools is probably much more important.” – Randy Heinemann
Some of those questions were addressed in responses from hobbyist woodworkers who (gasp!) actually own CNCs. – Editor “I have owned a LHR Technologies Compucarve CNC woodcarving machine for about three years now. I also build rustic furniture and I am an avid scrollsawer. I do these as a hobby. While my CNC machine is in carve mode, I am pursuing my other interests at thesame time. I can be cutting out a project on my scroll saw or cutting a tenon for my rustic furniture while I wait for my CNC project to finish. I can do more with the time I have. I guess to make it short and sweet I do not feel using CNC technology is cheating, but another aspect of working with wood that I love so dear.” – R. Michael Hoy
“I had a personal encounter with the question: Is the application of technology to woodworking cheating? I was turning a large segmented salad bowl for a gift. At the center of the design in the bottom of the bowl I planned the owner’s initials, in maple, to be inset in a one-inch ebony circle. None of the solutions I tried combined with my skills resulted in anything pleasing. Finally, I had the darn thing cut with a laser. It was beautiful. The bowl was great, but I was ashamed for having capitulated. My daughter emailed me a thought on the issue that changed my perspective: ‘But if a fellow were to straddle the fence of technology and traditional craftsmanship, he might render inspired projects that celebrate both and exceed the standards of each.'” – Harold Horchover
“I am an amateur woodworker who has been at it for 20 years and got into CNC routing six years ago. In my view, it is another tool in the woodworker’s kit and not the ‘be all and end-all’ in woodworking. I still do most of my projects with traditional hand or power tools and reserve CNC for certain special tasks. Nearly always, the CNC elements have been integrated into work done with other traditional methods. To me, CNC routing is a natural evolution in woodworking, just like SketchUp has replaced the drafting board. I do woodworking for fun, and I enjoy working with hand tools and most power tools, so why replace doing something I enjoy?” – John H. Little
“I’m a hobby woodworker, and my CNC router has made woodworking a lot more fun. On all my projects, like my boxes, signs etc., I add a lot more personalization. I even get orders to make and sell more. You still have to have good woodworking skills to make things come out right.” – Bill Chovan
“I built my CNC router about 2-1/2 years ago. I originally thought it was going to be my main ‘go-to’ machine in the shop – that most of my woodworking will now be centered around the CNC. With such precision, why bother using anything else? Well, in reality, although it’s a great piece of equipment to have around and although I could probably do much of my work with the CNC, I often find it is quicker and easier to do certain operations with the ‘traditional’ shop tools. Don’t get me wrong, I love having the CNC in my shop, I use it often—just not as much as I originally envisioned. So, how does a CNC fit into my shop? To me it’s kind of like a drum sander. Is it a piece of machinery that is necessary to have in a shop? No, not at all, but boy, it certainly makes some operations a heck of a lot easier to do than the old way.” – Brian Lee
And for some, the question of to CNC or not to CNC was a matter of philosophy – and a view of woodworking’s future. – Editor
“I guess it is a continuation of the old divide between the people who are dedicated hand tool users and the people who use a lot of new power tools. As the CNC gains more use among woodworkers, the ‘hands on’ satisfaction seems to get farther away and a bit more of the skills of using tools gets lost. My work consists of a lot of wood sculpting and hand shaping using a combination of hand and power tools. I don’t know if I could simplify this process using a CNC device, and I really have no idea if I could duplicate what I do by using one — but to me it seems like something would be lost in the creative process and take away some of the pleasure I get from how I do it.” – Greg Little
“For many people, woodworking is more than a job or hobby; it is a higher calling, a fulfillment of a basic need. For some, however – the Krenov’s of the world – woodworking is a spiritual experience and the very act of cutting into wood is a sacrament. For many of these people, I am sure that using a CNC is sacrilege. I have a problem with that. My opinion is that the method we choose to interpret our woodworking creativity is as much a reflection of who we are as the finished product, and that reflection has the same rights and weights as any other. Let the CNCs scream…and let the creation continue, because all roads lead to that same little pieceof heaven, where someone’s eyes get big and they just have to touch something you just made.” – Phil Gilstrap
“My first thought on your CNC machine was that, while inexpensive as CNC machines go, it’s probably too expensive for my shop. In fact, if I had that kind of money, I think I’d first spend it on a nice cabinet table saw and the electrical connection to plug it in. Beyond that, I’m wondering what the future of woodworking as a craft will look like, given the immense impact technology has already had on our lifestyles. I mean, what’s going to happen to the skill of woodworking if you can just upload a design into a computer program and have a machine do all the work for you? Will we someday be limited only by the X, Y and Z axis of our computerized machinery? How long until the boards are no longer flat and the cutting tool pivots across an arc from the horizontal plane to the vertical? Will our joinery then become a simple matter of mounting two pieces of wood on a machine and hitting ‘Enter’ on the keyboard to cut adjoining pieces to an exact fit? ” – Larry Schuh
“Technology. The End? Of woodworking as we know it? Yes. Of woodworking? No. The difference between woodworking today as opposed to next year, as opposed to 50 or even 500 years ago is simply a measure of the output ‘skill gap,’ which exists between the amateur and the professional. Tomorrow’s technology will only alter, improve, speed, and broaden the scope and availability of the working-of-wood, how we do things, but never end it. After all, while woodworking has its origins in the practical – a chair to sit on – as practiced by ‘woodworkers,’ whether professional or amateur, woodworking is clearly an expression of art, soul, the multiple and unending expressions of creativity. And the human species is, without a doubt, the ultimate creatively expressive being. I suspect the human heart’s need to create will outlast the trees themselves. Woodworking has a sure and glorious future.” – Christopher L. Clark
Craft Shows and Copies
Another question from eZine 299, this time relating to the discussion in WebSurfer’s Review, was the issue of making furniture in designs copied from well-known woodworkers or high-end craft shows: right or wrong? – Editor
“Some folks are really getting bent out of shape over this, and I think they should lighten up! I have been a ‘custom furniture builder’ for many years (I would make a piece according to my client’s specs.) These pieces may be made ‘in the style of’ Shaker, Arts and Crafts, Sam Maloof, etc., etc, but none of them are direct copies of anyone’s original creation or original copyrighted plan. I believe that ‘in the style of ‘ is great flattery to the originator, and it is not stealing anything. To me, it’s like playing music in a band, say, where a musician (or group of musicians) has adopted a playing ‘style’ (i.e.,: from Chet Atkins, Jimmy Paige or Brad Paisley – guitarists all) and applied this style to their musical compositions because this is how they learned to play. This is how we grow and develop ‘new’ styles and improvisation. If we didn’t do that, we would learn nothing…and we might as well just go home and vegetate!” – John Coulter
Some presented the argument that “there is nothing new under the sun.” – Editor
“Did not those ‘original’ designers copy the work of others? Did their chairs have four legs, a seat and a back? Did the wardrobe have two doors? All furniture flows onwards and outwards from basic designs, evolving as it goes. People challenge themselves, using others’ earlier work and perhaps building on that to create something slightly different. So creative juices start to flow. I think there would be no innovation if some degree of ‘copying’ did not occur ever. Surely all furniture makers must be guilty of it at some level.” – Lynda Kelley
And some made distinctions, between inspiration, and straight copies. – Editor
“Let’s see. You see a piece of furniture you like, photograph it, and attempt to duplicate in your shop. Unless all the joinery is visible, you need to figure out (design) your own joinery for the project. Unless you did a chemical test/analysis of the finish, you need to experiment and/or build your skills in finishing. How did you identify the wood(s) used in the piece? Were you permitted to actually measure the piece or only look/photograph? Unless you are building from plans, you must do a great deal of analysis and some trial and error to come up with something that ‘looks’ like the photograph you took.
“This is the essence of derivative work (copyright concept) that is fair use. Photographers for years studied Ansel Adams, even took workshops, all to be able to come close his photographs of Half Dome. There is no illegality here unless they sell the photo as an Ansel Adams. Ah, here’s the rub. Are you selling the furniture by trading on the name of the original worker, e.g. ‘a Maloof chair,’ or ‘a Maloof style chair.’ The first is illegal if it was not built by the Maloof studio. The second is fair use. So, my suggestion is give credit: ‘Inspired by Rob Johnstone design,’ or ‘Design based upon the work of Krenov,’ or like terms. Just be honest and say that the design is not wholly your own.” – Charles Googooian
“I think the point that is being overlooked is how is the work being presented. Copy a designer’s style, I feel is perfectly acceptable and happens every day in almost every industry. This is how trends/movements start. Someone designed and created the first ‘Arts and Crafts’ style piece. Others liked the overall design and began creating pieces of a similar design and style. This is how fashion trends begin as well. I myself am not a designer, I’m just not creative that way. The question is whether the work is being sold/marketed as an original or not. Let’s say I see an original Rob Johnstone piece and really like the design. I go home and use the same design elements and joinery techniques. Now if I want to sell it at a show, I can say the piece was inspired by a Rob Johnstone design or ‘in the style of,’ but I cannot say it is a Rob Johnstone piece since Rob didn’t have any part in the actual production of the piece. My final thought is that as long as a woodworker is not misrepresenting the piece then there is no real issue.” – Barry Breslow
Search for CD Holder Inspiration
Finally, in Feedback related to eZine Issue 299, we have a reader who is inspired to research the Early American furniture that inspired the Compact Disc Holder free plan in that issue (no longer available as a free download). How about it, eZine readers: any insights on Early American Revolving Bookcases? Is there one in a museum in your town? – Editor
“I noticed with interest that the Compact Disc Holder in [eZine 299’s] free plans is based on an ‘Early American Revolving Bookcase.’ Even after some thinning of my musical herd during my married years, my CD collection is well over 400 in number. After seeing the small but attractive coffee table sized CD holder, glancing at my CD collection, and envisioning a much larger revolving bookcase, I had a melding of all three images, imagining a large bookcase-size revolving CD holder or two or three…
“Do you or the readers have any recommendations on finding pictures or information regarding this old and venerable design for inspiration and proportions on a larger scale? I’m not looking for someone to provide modified plans but would like to visit the original source of inspiration before designing my Spinning Tower of CD’s. Just brainstorming a little on this but making it taller would invite wider proportions for stability and more efficient use of space. I would at least double the dimensions and add another vertical row of CD’s (or more with respective dimensional increases). With dimensional stability addressed and some added mass in the base to help anchor it, the remaining adaption to account for would be a larger and beefier swivel to handle the added weight while still revolving at the touch of a finger or two… OK, maybe a whole hand in my case, but I can live with that.” – J. Scott Bell