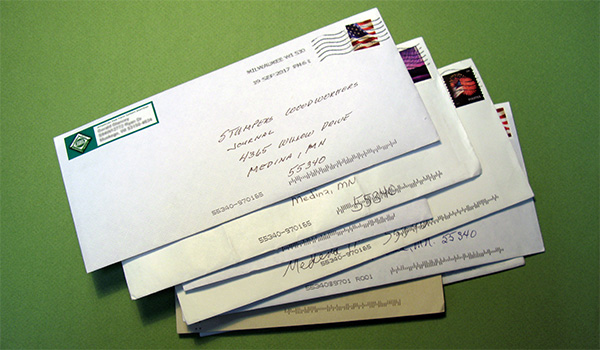
Granddaughter Project: What’s the Verdict?
The question Rob posed in his editorial last eZine related to his planned Christmas gift for his granddaughter: a rocking horse or a play kitchen, he wondered? And invited your votes. Some thought either choice was inappropriate at this age. – Editor
“Don’t you think it would be a good idea to wait until she can at least walk before putting her in her own kitchen? A horse? At her age, again, what are you thinking. She can’t even walk, let alone ride. There are lots of small toys; some of them will drive the parents nuts, but that is the idea of spoiling a grandchild: get revenge on the kids!” -Robert Hoyle
“At less than one year old, your granddaughter won’t get much use out of a play kitchen or rocking horse. My dad made our kids bright, colorful blocks to play with. At two, he made a push toy, a duck with rubber feet that slapped as the child pushed it. At three and up, that’s when they wanted horseys and kitchen.” – Jim Cottingham
Then again … – Editor
“If you are like me and would take about two years to make your gift, your nine-month-old granddaughter would be ready for either of your ideas.” – Dave Pettit
There was at least one vote against the rocking horse. – Editor
“Go for the kitchen – I made a rocking horse, and I can count on one hand how often and long it’s been used!” – Bill Schrage
But others had different experiences. – Editor
“I made a small rocking horse for my granddaughter last Christmas. She was a year and half old. She loves it. Not sure where I got the plans, but I was happy with my toy making.” – Rich Schaaf
“Having built and given a rocking horse for Christmas, I can definitively say that it is one of the best gifts that you can give. You will get more positive feedback from that one gift than you will anything else you make in that person’s life. It is also something that continues to give for generations. One of the great joys is seeing it passed down to another appreciative rider. Did I mention that a rocking horse is gender neutral. Who knows if you’re going to have a great-grandson or great-granddaughter? Do you think that a miniature kitchen set will become an heirloom? And finally, not that the two are necessarily connected, but, my goddaughter (the rocking horse rider) was on the equestrian team at her college, and is now studying to be an equine veterinarian. I gleefully remind her that I gave her her first horse.” – Tom Scott
That gender neutrality issue — whether or not – came up from a few other readers as well. – Editor
“Having made a rocking Harley for my grandson; call me sexist, but I felt the same was not appropriate for my granddaughter. Having studied the Harley layout, I then adapted it to be a rocking bicycle. I have made 4 so far, and there is demand for more. Nothing fancy woodwork-wise, I’m afraid, but very robust. She was, I seem to remember, about 13 months when I gave it her and she mounted and ‘rode’ off immediately. Still riding at 2 – just more vigorously.” – Martin Spurling
“I think that you miss a very important point: the kitchen sounds great, but how about some building toy to go with it? Girls like to build and use tools just as much as boys. Try and be a little less gender orientated when thinking about gifts. It is an opportunity to expand her horizon, not to pigeonhole her world. Just a thought and a hope that it expands your gifting experience.” – John Mullally
“As a born again chippie coming to terms with wood and sharp tools again, I read with some hilarity your article in this month’s eZine! I am in the process of doing the exact same thing for my granddaughter (born 12 months ago) at this very moment. The difference is that I am making a toy car that she (and her future brother!) can both sit in and pretend to drive. Have attached a pic of my basic design (using Sketchup Pro). That will keep me busy for some time: will have to turn up the wheels and lights on the lathe and use my newly acquired table saw, jigsaw and all the other really sharp man’s tools also acquired recently to cut out and put together the bits and pieces (with safety and sturdiness a priority). I am searching the web for ideas and bits and pieces to attach to it, like steering wheels, gauges or decals of gauges and things, horns, lights, number plates etc.” – Warren Howard
This reader encouraged breaking the stereotype of the rocking “horse,” per se. – Editor
“I encourage you to break the stereotype and ditch the horse. For irrational reasons, I was determined my kids would not grow up to be cowboys – I wanted to encourage the Viking side of my Norse heritage, so built a rocking boat for my kids. The design was organic (meaning I winged it). I did break one of the sides when pulling it to shape – but there was enough scrap to allow for a do-over. My babies are now 19 and 21 – both had many hours of fun – usually with a helmsman and a passenger in the back and sometime passengers in both the back and front. Passengers were often the sibling or favorite plush toy (try that with a horse). Anyway – here is to encouraging you to think outside the box (and ditch the horse).” – Leslie Troyer
“Just make both.” That was the message of quite a few readers, as well — some of whom expressed it rather bluntly. – Editor
“Come on. Really? You hafta choose? Why not build both? Are you lazy or just a bad granddaddy? You look to be in good enough shape to knock out both projects in a good weekend and a few afternoons, and she could develop so well by having both.” – Bo Chaney
“Make the kitchen set for Christmas and the rocking horse for her birthday. That should settle the issue.” – Emery Buziak
“Over the years, I have done both the kitchen and the rocking horse. I would advise you to do both, but do the rocking horse first. Kids lose interest in the rocking toys well before they lose interest in the kitchen. Another word of advice: let them have pretend water faucets. I put in real water once, and it was a definite mistake. There are, as you are aware, a million plans for rocking things out there. A buddy of mine made a rocking elephant and got a little carried away. He started out with only a few tools and wound up with almost a complete shop. He has to build more stuff or that is going to be the most expensive rocking elephant in the world.” – Lorin Bartels
And, people looked toward the future – the legacy of this project – and back to the past, remembering special projects from their own ancestors. – Editor
“A beautiful little wooden rocker just her size to be used now and for her mom to save and give back to your granddaughter when she has own daughter, and her granddaughter, and to each generation. It will become a family heirloom, just like the one made by my great-granddaddy and presently with my daughter, awaiting the day of my grand baby’s arrival! Your love of woodcrafting will pass as a legacy to each generation. Just talking about my rocker brings tears of joy in remembrance of my great-granddaddy. May God bless you.” – Jeanne Hendren
“She will enjoy the kitchen more next year, and you will have more time to work on it. Make the old-timey pre-electric kitchen so she can use her Play-Doh® items. My uncle built me a small china hutch when I was two. It traveled from Hawaii, where my father was stationed, to California, many moves in that state, and then I moved away to college. The one item I wished I still had: that plywood hutch.” – Elaine Duff
“I just glanced at the eZine. I, too, am excited about what to make my new grandson Quentin. I, too, don’t know what to make. I will keep reading the eZine to find out what you make. Anyway, you mention a rocking horse. I made one many years ago for my first grandson in about 2000 for Christmas. You can’t imagine how proud I was to give him that. One of the things you will learn to appreciate is the fact the things we make will be handed down when you have more grandchildren. That is something non-woodworkers will never have the satisfaction of feeling.” – Thomas A. Grady Jr.
From Trees to Lumber to Projects (the continuing story …)
As you may recall, in his editorial a couple of eZines back, Rob asked if any readers had ever created lumber “direct from a tree.” Yes, indeed you have — to such an extent that the stories shared have spread (so far) into two different eZines’ Feedback sections. – Editor
Some woodworkers, as part of this process, have found themselves working with some unusual woods. – Editor
“Just read your article about using timber from your own backyard. So here is a little anecdote. When we moved here to Oz from the U.K., we bought some land and had a house built. We had to have two trees taken out as one was leaning across the other; the tree feller was told to take both out for safety reasons, but he refused to cut one up for waste as one was a eucalyptus, which was the problem tree, and the good tree was a tallow. When asking what is a tallow, I was told it would be worth having it milled as it was a timber that would not rot, and was termite resistant (a natural oil type resin ). The log was four meters long and a girth of 38 inches. Cost a small fortune, but has been well worth it. It was milled into 1″, 2″, 3″ slabs. My neighbor at that time asked if I would like to store it under his rear decking, which was open to the fresh air but out of the rain — very little warping and shrinkage. I have used the timber for several projects: barbeque table, retaining wall, whilst it was unseasoned — still going strong after seventeen years. After it seasoned for a couple of years it has been used for woodturning, foot stalls, coffee tables and and plate racks, and several odd boxes. I still have a small length of it left.” – Len Last
[Editor’s Note: Tallow’s scientific name is Eucalyptus microcorys, if you’re inclined to look it up.]
“I have made lumber from the trees on the property and then used it for making projects. One such project I made was a jewelry case for my wife made from Styrax obassia; another was a jewelry case from maple made for my sister. Other projects include small stands made for friends who can’t find anything commercially available for that special corner of their house. All of my turning wood comes from trees cut on the property: apple, cherry, maple and ash. Tool handles come from the prunings of dogwood trees. I just cut two Japanese Snowbell trees, which are related to the Styrax, and will dry that wood to see if it works as nicely as the Styrax did. ” – Charles Carney
“Last fall, we had a freak snowstorm at the end of October here in Pennsylvania, and many trees came down. There is a wonderful hiking trail system on a local ‘mountain’ near my home, and I frequently take my two Labs for a walk there. Several trees had come down across the trails, and volunteers quickly cut them up into 2′ to 3′ pieces and left the debris at the side of the trails. I couldn’t resist taking a chunk down the mountain with me every time I went there. Throughout the next couple of months, I must have hauled down 20 pieces or so. I then took them to the band saw and resawed the longest pieces into 5/4 and 4/4 slabs and stacked them in the workshop to air-dry. There was one particular species that, try as I might, I could not identify. I tried to identify it by the bark and then by the leaves on the fallen trees, but there was a big pile of debris, and by the time I thought of looking for the leaves, they were mostly shriveled up or buried in snow. I spent the entire winter looking at that pile of wood, anticipating what I could make from it but knowing I should let it dry for at least a year… that is the hard part of this process! Well, this spring, the stub of the fallen (yet to be identified) tree started to send up new shoots, and it soon unveiled its foliage to give me the long-awaited answer. It is a Paulownia tree, native to China! The wood is light, fine grained, soft and warp-resistant. It is used to make the soundboards of musical instruments, wood boxes, chests, clogs and even surfboards! Now my mind is full of ideas for what to make with my harvest. So, while I haven’t yet brought the cycle to full circle, I’ve have truly enjoyed the journey up to this point… this is something every woodworker should try!” – Mike Mathias
Other woodworkers have been inspired — for various reasons — to do even the actual cutting of the trees themselves. (With, um, various tools…) – Editor
“Back when I was living in Weslaco, Texas, my next door neighbor decided that he didn’t like the way his mesquite tree kept weeping sap onto his brand-new concrete walkway, so he had a tree man start to take it out. Luckily for me, the tree guy never came back to finish; he left an 8′ tall 18″ dia. trunk standing upright on his lawn. As a neighborly gesture, I told him I would take it down for him, because I could certainly use the wood. Sadly, all I had for the task was an electric chainsaw and a kitchen chair. So, I spent the next 6 hours standing on a kitchen chair making vertical cuts from the top to the base, then cutting across the base to free the new plank. Maybe not the best method, but being my first attempt at such a thing, it did the job. I was covered with sawdust and sweat. Needless to say, the planks were a bit uneven, but a family friend let me use his planer to smooth out the planks. There went another 6 hours. (Did I mention they were a bit uneven?) I’ve still got one of those monsters from back then, but the rest of that tree turned into carved crosses, part of my headboard, countless knife handles and tools, and a fish tank stand. There is definitely something to saying that you personally knew the tree that your project turned into, and it gives you a real appreciation for some of these historic sites that still have the barns, houses, fences, tools, furniture, etc., etc. that were made using the same methods but with FAR more primitive tools. I still find myself eyeing these portable band saw mills, so I believe I’ll probably do it again!” – Sean Carney
“We have a Norwood sawmill and Ebac kiln here in Lincoln County, West Virginia. I had a friend ask me about an uprooted cherry tree on his creek bank in his front yard. We were able to extract the tree from his yard, mill it into lumber (net about 125 board feet), dry it in the kiln, and create most of the components needed (used cherry veneer ply for panels) for a small entertainment cabinet for his family room. This piece is really close to him simply because it came from his front yard. He tells everyone about it that visits his entertainment room as an ‘interesting talking point.'” – Troy McClung
“I got sick of seeing usable logs go to waste or turning them into firewood. So, after visiting the NYS Woodsmen’s Field Days in Boonville, New York, I bought a small band mill I saw demonstrated there. Since, I have milled cherry, ash, butternut, aspen, yellow birch, hemlock and whatever other logs I had cut. I have built kitchen cabinets, tables and put in two ash floors. I cut lumber for building sheds for my son and son-in law and trim and framing lumber for myself. I donate surplus hardwood to our local high school woodshop It is amazing to see what is inside a log when you cut it. Currently, I am cutting wood for turning blocks, spalted hard and red maple, and cherry crotches. This was one of my most fun tools, and it is made right in New York State. The mill cost $3,000, other equipment $600. Not only does it give us an unlimited supply of lumber, it is fun.” – Tony Pingitore
“A couple years ago, my wife and I moved into our new house on 9.3 acres of land which is mostly wooded. There are quite a few sick trees among the healthy ones, so I had to have some cut down. As a woodworker, I couldn’t bear the thought of all that wood being turned into firewood, so I started researching on how I could mill them into something usable. I decided on the Alaskan MKIII chainsaw mill and a new chainsaw. It’s a lot cheaper than a band saw mill, though it’s also a lot slower. But I have a lot of time. I’m turning a bunch of silver maples into boards for a new kitchen, as well as a bunch of ash trees that were killed by the emerald ash borer into some new flooring. As you know, without a kiln, the wood takes a very long time to dry. Also, moving large logs around is not an easy job. I have a compact tractor with a front end loader to lift them into place on a jig I’ve constructed for my Alaskan mill, but not everyone has that. The logs can be milled as they lie on the ground, but I find it’s much safer and easier to lift and secure them onto (heavy-duty) sawhorses and run the mill on a pair of 2×4 rails. It’s a lot of hard work, but I wouldn’t be able to live with myself if I had just burned what probably amounts to 5 to 10 tons of perfectly good wood. Even more so since I discovered the maples have a lot of ambrosia staining.” – Jay Bruckner
“I have a Lumber Maker attachment for my chainsaw which mounts onto the bar and allows me to rip rough planks from a log. No heavy equipment is required to move the logs as you do the cutting where the log lies. The trick here is to switch the chains out and install a chain that has been specifically ground to rip instead of crosscut. My dad planted a couple of moraine locust trees the year I was born, so saving the wood from these was important. It is similar to a honey locust and is about as hard as concrete! The lumber that it yielded is beautiful, and I have made several pieces, including a ‘chest of baskets’ for my wife. Cutting the logs requires patience and practice. In addition, you need a planer, a joiner, and a drum sander would help a lot, too. Yes, the wood is not costly in terms of money. You will, however, spend a good deal more time getting to the end product. Some might not wish to expend this much effort along the way. I enjoy the work, and the final product is more meaningful when completed.” – Boyd Nordland
And, of course, there are woodworkers who may not have cut the lumber themselves, but have built a variety of items from trees they have known in person. – Editor
“I have used maple, for napkin boxes, as well as alder. I also had several alder trees cut up by a local guy with a sawmill, into 2″ x 8″ slabs, for future projects. The maple started out as a 6″ to 8″ log, 4 feet long, dried about 8 months. I established 2 sides with my jointer, then finished up with my planer and table saw. I’m pretty much a beginner, so I’m sure there are better ways, but it’s doable even at my skill level. And it is kind of neat to be able to tell people it came right from here.” – Al Mashburn
“I had a very large open field black cherry on the corner of my property that was starting to decline due to how close it was to the road. I had a local sawyer, who was in the area milling lumber for a neighbor, mill it up for me and stickered it to dry in my garage loft. Total cost was under $500.00 for what the sawyer estimated was 1,500 board feet of wood. A neighbor who builds boats took all the crooked pieces off my hands to use as knees and ribs. I had hoped to use the lumber for built-ins and trim work in an addition we were building at the time, but was worried that I wouldn’t have time to properly dry the wood. Well, 10 years later and the built-ins aren’t completely finished.
“In the meantime, the cherry is beautifully dry and I’ve made two end tables, two built-in dressers and trimmed out an entire living room using the lumber. I still have hundreds of board feet left. Admittedly, the lumber isn’t perfect, and there’s quite a bit of waste when milling, but I own the whole tree, so I can also make beautiful thick book-matched tops and panels. If you can wait for the lumber to dry, and have a place to store it while it does, and can tolerate wood that isn’t ‘perfect,’ cutting your own lumber is a beautiful thing.” – Andrew Hendrickson
“It has been many years now since I have purchased wood from a retail outlet. I was able to harvest close to 500 board feet of red oak when my neighbors cleared their property to make room for their house. I then was able to harvest another 300 board feet of red oak when we cleared our property for our cabin. Luckily, I have access to a local lumber mill, where they turned my logs into quartersawn boards. I am always on the lookout for someone who is clearing their land. I came upon a clearing project for a drainage ditch, and I was able to harvest over 500 board feet of white oak and hard maple. I could have taken more but my wife, aka ‘the treasurer,’ starting complaining about the amount of lumber that I had stacked in our barn. I am what you call a reverse lumber buyer. I buy my lumber before I have a project to make it out of. I have also been able to harvest some white cedar, pine, poplar, hickory and cherry, all for just the cost of milling — which runs between 25 to 35 cents a board foot. The bottom line: yes, harvest your trees for the lumber! You will just have to be patient while waiting for the lumber to dry, about a year in my case.” – Mark Hoard
“My interest in using trees started back about 1980 when the city cut down a big walnut in front of my house for a street widening project. They took the trunk but allowed me to gather up the limbs. Took ’em to an old farmer with a sawmill, and I am still using the walnut boards. Later, when a white oak blew over, and we had to remove a shingle oak, they went to the sawmill too. The guy I use now has a bandsaw mill which gives me less waste and can handle smaller logs. He charges $40 per hour, which works out to about 20 cents per board foot. I have since recovered more oak, some silver maple, a blue spruce, and some red cedar from neighbors. Eastern redbud is beautiful wood if you can find a tree that is not rotten in the center. Still watching for osage orange. Some of the projects: The 6′ wide stairs from our dining room to family room is built from white oak 1×12’s, along with fancy newel posts. Also a schoolhouse clock, and I’m starting on a replica of a giant English oak wall clock. A set of Craftsman-style oak bunk beds for the grandsons. All the oak trim in a bathroom remodel and walnut trim for a kitchen remodel. A red cedar tool box for a grandson. And picture frames, toys, and miscellaneous shelves. Many of my shop shelves and racks are made from the lower grades of my milled lumber (lots cheaper than #3 pine).” – Mike Schoeppner
“My first lumber cutting project was larger than most and a little overwhelming. A number of years ago, the world’s largest American chestnut blew down about a mile from my farm. I got permission from the parks department to take the trunk, which was 6′ in dia. and 20′ long. After donating a 6″ slice to the local pioneer museum, it took me 2 years to get it sliced up and drying. Because of a major shop renovation, I’ve only gotten about 15 small projects made out of it, but my granddaughters are scheduled to get hope chests and my wife a sewing machine cabinet.” – Charles Redford
“Back in the late ’70s, a friend of mine who lives in southeastern Louisiana was going to build a house, and we were going to do as much of the work as possible. He was not one who could draw out his plans with a set of drawing instruments, so he drew the floor plan on a sheet of graph paper and the elevation on another so he could get the rise and run of his rafters. The house was a three bedroom, two bath, with a steep pitch roof and a big hobby room upstairs. He wanted to panel the inside of most of the house with cypress tongue-and-groove boards. We found some standing cypress, cut it down, hauled it to a local sawmill, cross-stacked the boards under a shed to dry, and we were in business. After air-drying for some three years or so, we planed the wood to thickness, cut the tongue-and-groove and a chamfer on each board. Then we went to paneling the inside of the house. The paneling is still in place and has a rich color to it. If you have the equipment to work with and a place to air dry the wood or even better, to kiln dry the wood, it is a great way to go.” – Charles Buster
And here is a letter from a reader that brings the trees to lumber topic and that of the grandchild gift together. – Editor
“I have gone from tree to finished product many times, though most of the projects are relatively small in scale.I do turn a lot of green blanks, among other things, but I believe you are asking about ‘flat’ work. One ‘flat’ work project was included in your reader’s project gallery a few years ago. I am happy to report that each of the two cribs is being used for a second grandchild, for a total of four, and both cribs have withstood the tests nicely, though they do show some wear Cherry certainly ages better than do I. I am currently working on two matching four drawer chests out of some of the same curly cherry and hope to have them finished before Christmas. All it takes is time in the shop!” – Jim Webb