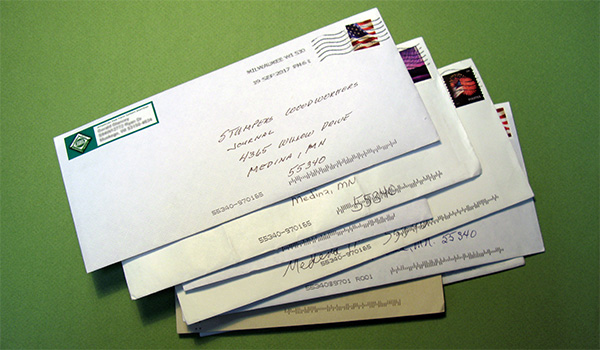
Routing Arcs on a Ball
In our last eZine issue, one of our Q&A questioners wanted to know how to rout decorative arcs on a ball. A couple of readers had some additional suggestions for him. – Editor
“For Mr. Schroeder’s ball routing problem, my solution would be to build a cradle on a thin sheet of plywood to mount over the router bit on his router table. Use 4 wooden triangles to support the ball in both directions (mount them so the ball will rotate in any direction, but the bit will always point to the center of the sphere). The view shows one-half of the setup; there would be another set of blocks at 90 degrees to this.
“Then mount another piece of plywood on four legs (like a little table) above the ball. Fasten a dowel into a matching hole in a block of wood with glue and then hot glue the block to the ball. Draw and route the desired pattern into the plywood ‘tabletop.’ The width of the routed groove would be the same as the diameter of the dowel. Now feed the dowel into the routed pattern hole and mount and clamp the ‘table’ over the top of the ball. Start the router and, by moving the dowel around in the pattern grooves (like a lawnmower stick shift), it will trace the shape into the ball. (For a shape like this where the center of the pattern would fall out, you’d need to hold the center portion in with small blocks that would maintain the position of the center piece until you arrive there with the dowel, then temporarily remove that one block as you pass by; or alternatively, leave the center piece out and trust yourself to always push against the remaining side of the template with the dowel. The flat pattern could be developed and tested by using a pencil in the fixture prior to using the actual router.” – Jerry Firlik
“I’d like to offer an idea on this subject. Please pass it on if you think it is worthwhile. It seems to me that the only way that you can do this is to keep the router anchored solidly. Create a simple jig to hold the ball stable — a simple hole in a plywood sheet should do. It should be wide enough to hold the ball steady, but not so wide that the ball slips through. Trace the pattern on the ball. Screw on two handles so that you can hold the ball steady and slowly push it forward against the router bit. You may have to move the handles. Better yet, screw on one handle at the bottom of the ball (sort of like an upside down joystick) and raise the ball and holder up to meet the router bit, then turn the ball along the trace. I’d love to be in the shop when you try this…” – Habib Salim
Helping Others Out
In last eZine’s editorial, Rob asked how you, as woodworkers, help other people out. That same week, a devastating tornado struck the city of Moore, Oklahoma – providing another opportunity to help people in the aftermath of that tragedy. – Editor
“Just received and started reading the latest eZine. I was very pleased to see that you like to donate test tools to Habitat for Humanity. I work with the local affiliate (Wake County, North Carolina) every Saturday. This has been how I spend every Saturday so far this century. Actually, the first time I participated in a Habitat build was in 1994. It was around ’99 or ’00 that I got a bit more serious and made it every week. This past Saturday, I went to four different tool trailers to find the tools I needed for my volunteers: a couple of flat bars and some utility knives. There are never enough tools available, and what is available is ofttimes not in the best repair.
“I’ve also made a few pieces of furniture for the kids, done some repairs on some of the neighbors’ houses and made stage sets and props for a group of folks who are developmentally / emotionally challenged. The work I do the most of, the work I enjoy so very much, is building with Habitat for Humanity. I just wanted to say thank you for thinking of us as you make those donations. Every tool helps.” – Ray Martin
“Finding ways to help out is never hard when you are a woodworker. The long list of projects that I have is proof enough of that. I have helped out in a unique way. I work for a high-end door and window company. We generate lots and lots of scrap wood that is really good stuff. I have made some great connections with the local turning and woodworking group. And through that connection we do a ‘Wood Dump’ once a quarter. I come in on a Saturday and open up the gates to give them free access to all the wood they can take. We save back lots of the more choice pieces over the three month period. The wood all goes to great causes. The groups make pens that goes to the serving military overseas, tons and tons of toys are made for needy children, and many other things like that. Great topic! We all need to find ways to help out our neighbors.” – Clayton Clark
“This is a story that is too difficult to really tell in detail. Our son was murdered in 2005 and, as part of the process for arrangements, I started looking for an urn. We really wanted one with his name, dates, photo, etc. What we found was a lasered urn with all of the information we wanted was around $600. Being a woodworker, I decided to make the urn myself. That started me looking at lasers. We were able to find a very good deal on a laser that had never been used but had been sitting in a warehouse for two years. We currently work with a support group, providing urns and laser photos on wood for anyone who has suffered the kind on tragedy we experienced. The first several urns I made I used a box cut, but I now use a lock miter joint, which gives a much cleaner look. The bottoms are removable for inserting the ashes. There are few things in my life that have been as rewarding.” – Ed Sapp
“There is no greater need for people with woodworking skills of whatever caliber than in the city of Moore [Oklahoma]. And the sooner you can get those folks down there, the better.” – Rodger Rudkin
Best Shop To Build
This reader responded to the question from last issue’s Q&A about building a new shop with a suggestion: move the location of the shop. -Editor
“The Q&A of the most recent edition of the eZine contained a question about the best kind of construction for a new outbuilding to be used as a shop. I agree with the recommendations, particularly those pertaining to lighting and dust management. But, I think there is a better option than an outbuilding. If one is building a new house, simply design the house with a walk-out basement that contains a garage and a shop. I have a 24×28 garage adjacent to a 20×40 shop. Both are climate controlled. I use the garage for overflow assembly of large projects and finishing. As new construction, I was able to route a 6″ PVC pipe beneath the slab to an adjacent room for dust management equipment. When I did a cost-benefit analysis, the basement shop was less expensive than a similarly elegant outbuilding. It is also much more convenient.” – Carey P. Page, M.D.