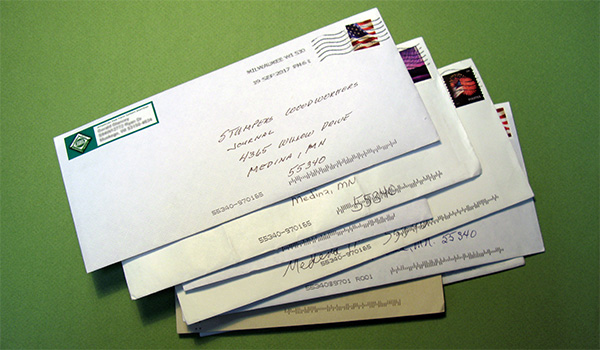
Rob’s editorial in the last issue of the eZine posed a question of style – specifically, whether woodworkers try to incorporate specific stylistic choices into their projects. Here’s an answer we received. – Editor
“With any woodworking I do, from tiny boxes to outdoor hard landscape construction, my first instinct is to try to lighten the appearance of the work by paring away any unnecessary timber bulk. The simplest example is to bevel at least one edge of trimming timber, and I prefer to do this on the underside of the workpiece, which contributes a floating feeling. Curving the underside of bearers, so that the centre of the span retains the minimum cross-section required for strength, contributes style, but also allows for a larger mating area where bearers are bolted to piles or posts. I find myself doing too much post-and-rail fencing to keep small dogs where they’re supposed to be, and get a sense of lightness by alternating two rail widths (say 150 x 25 and 75 x 25), and using a dark stain to highlight paler foliage behind, in front of, and through the fence. When constructing wooden gates, by putting the brace in compression instead of tension, I get the same feeling of lightness – subjective, I know, but it works for me.” – Graeme Coles
And, of course, we are still hearing from woodworkers who have advice or memories to share about projects made for the grandchildren – their own or others’. – Editor
“I don’t have a story about projects built for my progeny. But I do have one about a ‘toy chest’ requested by a coworker for her son. After the request was made, I realized there would be safety issues with a chest, the top of which could fall on little heads and fingers. My love of Shaker and Mission furniture influences my designs, so I knew I wouldn’t build anything but a paneled chest (which I assumed would outlive any plastic one that might ordinarily be bought). I solved the safety issue by not requiring that toys be stored / retrieved through the top. What I built was a chest that could convert to a storage unit with open shelving. The conversion is done by repositioning the detachable back panels so that they become the unit’s shelves. What I like about this is that you can readily go back to a top-loading chest when there’s no longer a safety concern. Maybe that takes until the kid goes off to college, but then Mom has her choice of what to do.” – Mike Weise
“Make sure you include a secret compartment. All kids love having that secret place to hide something special. I made a jewelry box for my daughter, now 33, and yes it has a secret compartment. She is still my little girl.” – Joe DeJulio
Cutting Corners with Glue
We also heard a reaction to one of the queries in our Q&A section, from a woodworker who wanted to skip the mixing part of using two-part epoxy. – Editor
“I am writing in reference to Randy Wolfe who said he has heard you can put epoxy part A on one surface and part B on the other surface. I am a retired paint chemist and formulator with 47 years of experience. People who try to cut corners and go against the instructions are their own worst enemy. In an epoxy, the epoxy resin and the catalyst must be mixed in a definite mathematical relationship to one another. They must be mixed thoroughly and then allowed to ‘marry’ for a certain period of time to achieve ‘design’ properties. There are hundreds of possible resin combinations and literally thousands of catalyst combinations to achieve a number of design properties. But if you cut corners and don’t do it right, you got garbage.
“I have two epoxy glues that I use: 5-minute and 45-minute. The first has an open time of 5 minutes. This I use for little jobs that I can get clamped and left alone before it sets up in 5 minutes. The second is the 45-minute system that has an ‘open’ time of 45 minutes which allows the glue joints to be assembled and adjusted as is needed. Epoxy glue is very expensive in comparison to other competent wood glues. You would choose an epoxy because it will what no other chemical compound will do. He should ask himself ‘why epoxy?’
“I personally have had a tendency to over engineer my project my entire life. I have to go back, for time to time, to Occam’s Razor: ‘The easiest solution is the best.'” – Richard Melton
Rob’s editorial last issue confessed to his obsession with casters: an addiction to adding mobility to everything in his shop that could be put on wheels. Readers had a lot to say on whether or not their shops were mobile. – Editor
“I’m with you. Everything in my shop is on casters. Except my sawhorses. That gives me an idea.” – Ken Erlenbusch
“My shop is a bit undersized (25′ X 25′), and most of my shop is on casters. I use 3- and 4-inch casters to insure that I can roll over typical debris without too much trouble.” – Jeff Winders
“If it wasn’t for everything on wheels, I wouldn’t be able to create anything. I just don’t have the luxury of a lot of room, much to my dismay.” – Bob Trachta
“Absolutely anything I can put on casters, rollers or wheels (depending on size and weight) I do, unless it is light enough to break down and store away.” – Dan Robinson
Some felt it was the shop location – or configuration – that determined the need for casters. – Editor
“When I received permission to add six used stationary tools to the garage, the only requirement from the better half was that both cars had to be in the garage at night. Rockler happened to have a special sale on their rolling bases so I ordered enough sets for all the heavyweight tools.When the cars are out, it’s a shop. While admittedly, cleanup and put away takes a bit of time, it is well worth it to have a full shop when I need one. I had to develop special driving skills to get both cars in the garage very close to all the machines, but I haven’t dented either the cars or the machines. Rolling bases are wonderful!” – Ed Amsbury
“If your shop were as small as mine, just half of a garage, you would have used casters a lot sooner. All my major tools have casters on the rear of the cabinets. On the front, I’ve installed a 2″ X 2″ piece of angle iron so I can use a ‘J’ bar that I built to move the tools around. The ‘J’ bar has the other pair of wheels with a pin on the tip of the J. I just put the pin in a hole in the angle iron and away we go.” – Robert Hoyle
“I, too, am an avid woodworker who enjoys transportation in my shop. I have a lathe that is on the light side, but does what it is supposed to. My lathe is a Nova 1624. I have it on wheels and I made a shelf at the bottom of it. I normally don’t turn heavy off-center pieces of wood on it, but when I do, I install heavy ballast on the shelf. I know you’re not supposed to put a lathe on wheels, but I did. Everything in my shop is on wheels ’cause my shop is also my garage.” – Wayne St. Amand
“I’m still setting up my shop, but I think I’m going to have to put everything on wheels. The space isn’t bad – about 18′ by 18′ – but there’s a set of Laly columns down the center, and I expect I’m going to have to dance around those, and/or rotate machines, to get reasonable working lines.” – Joseph Kesselman
Or the configuration of the shop user. – Editor
“I had to put all my shop equipment and worktops on casters after I became a wheelchair user. My workshop is relatively small, so the caster platforms make it easier to arrange the items on a need-to-use basis. I built all the caster platforms so the equipment and worktops are all at the sitting height. I really enjoy your newsletter and the valuable information it provides.” – Dave Pilkington
“The only things not on casters in my shop are my benches. I have a rolling cabinet for my planer with storage underneath; a rolling power hand tool crib; wheels on my table saw (SawStop), jointer, band saw, router table and scrap lumber bin. My drill press and spindle sander are both on one of my benches. Funny thing is, though, I hardly ever move them around . . . but when I do, hey I’m rolling.” – Carlos J. Dominguez
Some readers are just really big fans of wheels. – Editor
“Wheels are the greatest thing since, er, the invention of the wheel. I have a 20 x 28 shop which might be big enough for me except for the fact that our vehicle has to come inside each night. Consequently, only one tool in the shop is stationary, the table saw. I might have considered having wheels on that, too, but it’s too heavy and there’s the ceiling-mounted blade guard/dust collection unit and then there’s the uneven floor. Once I had it set I didn’t want to move it. Everything else is on wheels. The 28-year-old ShopSmith, the miter saw, CarveWright, FlatMaster, scroll saw, the huge Legacy Ornamental Mill, planer and if I’m building anything too heavy or bulky to manage, I put it on wheels too. Caster wheels are wonderful in my shop. I even made a roller stand with caster wheels. It’s good because it doesn’t ‘steer’ the work, especially important when infeeding on the table saw. I don’t need my roller stand to fight my efforts to keep the workpiece against the fence! I have extra wheels on hand in various sizes and types for any occasion. What would I do without wheels? Keep on rollin’!” – Don Butler
“My husband, Jim, is a believer in casters. We bought our house almost three years ago. We have spent all that time fixing, organizing, etc., but my dear hubby has finally found some time to start organizing his shop, aka (per me) “man cave.” He, too, is putting all things possible on casters. I am waiting for him to finish up his shop and move on over to the shed. That will be a great feat. Thank you so much for your input on casters. I thought Jim was the only one like that. He has storage containers full of different sizes and says. ‘Well, you never know when you may need some.'” – Teresa Dowdle
And then there’s this guy, whose shop mobility method is a little bit … different. – Editor
“I am more of an ‘anchor it to the ground’ type of guy. I do not want machinery to move when I apply pressure on them. When I need to move something, I have a fold-up engine hoist. I have a bridle arrangement that will allow me to hook to any of my power tools and raise it off the floor and move it wherever I need in my shop. I tell people that the engine hoist is one of the best things I have bought as an accessory for my shop. They can be had at the local big box made in China store for less than the $200 mark and will pick up 2 tons on a short pick-up arm. I have a portable generator that is stored in my shop on a shelf to get it out of the way. When I need it, I roll the engine hoist over to it, hook to the bridle and pick it up and set in the back of the truck or on a trailer or on the concrete drive. When I need to change blades on the riding lawnmower, I use my engine hoist to lift the front of the mower so I can put some jack stands under the mower and change the blades. ‘In my younger days,’ I used to manhandle things but I am to the point I need to save all my energy for more important things.” – Charles Buster
Gun Stock Bedding
We also heard from a reader who agreed that it was a good idea to let a gunsmith repair a particular gunstock. – Editor
“The question from Nancy about repairing a gun stock brought good advice from both Chris Marshall and Tim Inman. I would only like to add another reason to have the repair done by a gunsmith: The “bedding” of a rifle barrel into the stock has a major effect on accuracy and consistency of the rifle. Any repair of the stock could have an adverse effect on this critical component, and should therefore be done only by a competent gunsmith.” – George Worthington
Dust Collection Hope
And this reader had some additional ideas for the questioner in last issue’s Q&A who wanted to retrofit an old table saw to modern dust collection standards. He began with a quote from the Woodworker’s Journal experts’ answers. – Editor
“Just a comment:
“So – retrofitting an old (but good) saw to comply with today’s workplace standards and practices is what you’re up against. Or, just learn to live with it and get a broom …”
“Give this guy some hope!
“I have a 1985 vintage Delta Contractor’s saw (bought it new) that most likely had – or didn’t have – the same dust control features as P.L. Cannan’s. Over the years, I have customized the saw to meet my changing needs by upgrading to a Biesemeyer fence and custom building extension wings to accommodate a router table and large crosscut sled. However, the most significant changes I made were to increase the dust collection efficiency on the saw AND in my workshop. These modifications were the least expensive and the least complicated of any I made to that old relic of a saw.
“Diagnosed with leukemia in 2002, I spent a long time away from the shop, and a whole lot of other places as well. When I recovered enough to regain my woodworking interests, I had to make some changes to my shop environment to accommodate my ‘new normal.’ Improving air quality became my primary objective. First, I closed the bottom of the saw base with an aftermarket 4″ plastic dust port/collector sold at Rockler, put a 2-1/2″ reducer which connects to my large Ridgid shop vac equipped with a near-HEPPA filter through a Vortex separator, bought from Rockler. I cut a baffle that attaches to the steel saw housing on the back of the saw with magnetic tape from ¼” plywood scrap. The baffle is cut to accommodate the passage of the drive belt from the motor to the saw arbor. The baffle fits close enough that it must be removed to cut any kind of bevel. After I did these things, I discovered a number of holes in the saw case housing that I taped over with pieces of duct tape. Dust also escaped through the spaces created where the cast-iron table bears on the steel saw case housing, so I used a small part of a can of spray foam insulation to seal those spaces. Use this stuff sparingly! These modifications do not impede the saw operation and greatly decrease free dust in my shop.
“Other shop operations contribute more to the dust problem than my saw, and I, like you, use a dust mask. However, I use a 20″ box fan with two furnace filters taped to the intake side of the fan that runs constantly when I’m in the shop. I use a coarse filter on the outside to catch the big stuff and a fine filter nearest the fan to get the smaller stuff. I change the outside filter when I see it getting dirty, and the inside filter less frequently (filters are cheap!). Because the fan is so light and portable, I can move it close to whatever dust producing operation that requires it. Since I have made these changes, I have noticed a significant reduction in the amount of dust collecting on various surfaces in my shop.” – Rick Ross