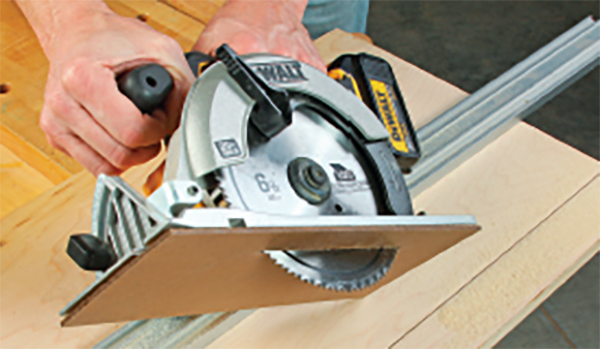
I have a Craftsman direct drive saw that is about 3 years old (model 137.228210) and would like to begin using a zero clearance insert for almost all of my sawing operations. Sears does not carry one that fits my saw and most of those available from 3rd parties … either the size, shape or thickness is wrong. My current inserts are made of stamped metal only about 3/32″ to 1/8″ thick and the shoulder where the insert fits is only recessed by this amount. Most of the blanks I have seen in Rockler, MLCS, and others are 1/2 inch thick. If I make my own from 1/8″ thick material, will it be safe and what is the best material to use…Plexiglas, plywood, hardboard, plastic, etc.? Or…if I use a 1/2″ blank, what tool can I use to reduce the blank’s edges to the 1/8″ thickness required to seat flush with my table top? Or should I just buy another saw?
Michael Dresdner: There are a few plastics that would be safe and rigid enough to work in 1/8 inch thickness, including polycarbonate and phenolic. You could use either of those, but avoid Plexiglas (acrylic) because it tends to shatter on impact and it is a bit too flexible in that thickness. You could also use dieboard (dense, high quality plywood made with thin, voidless plies.) However, if it were me, I’d use a thicker insert out of hard wood, or a commercial insert, and rout the edge leaving a 1/8″ thick lip just the width of the recess. You can cut the recess on a table router with a bearing-mounted rabbeting bit.