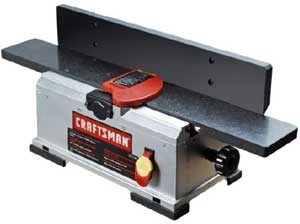
I have a 6″ Craftsman benchtop jointer. Every time I run the edge of a 3- or 4-foot board across it, the cut is concave and not straight. What can I do to correct this?
Ellis Walentine: This sounds like a classic case of the knives being set too high relative to the outfeed table. Raise the outfeed table so it is just a couple thousandths above the cutting arc of the knives at top dead center. It wouldn’t hurt to see if the tables are co-planar while you’re at it. You can do this with a reliable straightedge placed across the infeed and outfeed tables from end to end. If either table droops at the end, it could cause concave cuts.
Lee Grindinger: Concave edges can have a couple of causes. The first cause, and by far the easiest, is that the knives are too high in relation to the outfeed table. To correct this condition the first thing to do is check the knives themselves. Is there a high knife? If they need changing, this is the perfect time to do it. Knives should protrude no more than two thousandths ( .002 ) from the plane of the tables when they are zeroed out, and they should never be below that plane. A dial indicator with a magnetic base is a good tool to own for setting knives, but a perfectly acceptable job can be done by “walking” a straightedge using the top of the arc of each knife. With the tables zeroed out the straightedge should “walk” about an eighth of an inch as you turn the cuttherhead by hand. If all of your knives are the same height going into this, it may be easier to adjust the height of the outfeed table. Not all jointers have this capability, but it’s a desirable feature.
The next, and more troublesome, cause is that your tables are not on the same plane. You’ll need an accurate straightedge and winding sticks for this check. Raise the infeed table to the same height as the oufeed table. Using the straightedge, check that the tables are in plane from one end to the other. Next, with winding sticks placed across the ends of the tables, check for twists. If either table needs adjustment, you’ll place shims in the dovetail ways upon which the moving tables slide. If your outfeed table can accept shims you should true the outfeed table to the infeed. If the outfeed table cannot be adjusted, place shims in the ways of the infeed. Keeping in mind that the table will be moved and the shims could become dislodged, place the shims accordingly.
Michael Dresdner: The most common cause of that is tables that are out of alignment, but it could also be caused by a high blade.
First, check the blades to ensure that they are all the same height as the outfeed table at the top of their rotation. Then turn the head so that no blades are showing, and raise the infeed table level with the outfeed table. Using a long straightedge or laser level, check the tables to make sure they are level from end to end. Usually, the condition you describe is due to one or both of the table ends being lower than they are at the center where they meet the cutterhead. You can usually adjust or shim the tables so that they are dead level from end to end, and that should solve your problem.