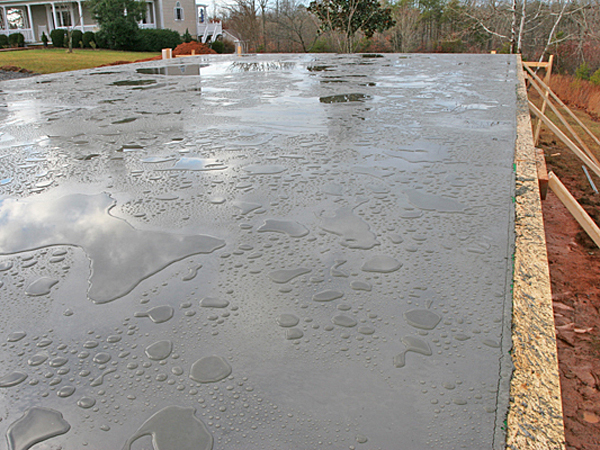
I’m getting ready to retire in the coming months and am in a position to build an actual workshop for my wood orking toys instead of sharing with the garage. I know my wife would be happy to have a place to park her car out of the elements, as in west central Georgia there aren’t many basements that I could use. My question: if I build a two-car garage, what should I use for flooring?
I know standing all the time on concrete is tiresome and can cause problems with leg issues that I would like to avoid, but are rubber mats the answer or should I consider something else? As I am in the planning stages, it would be nice to have some ideas so I can pass along to the builder so they can be worked into the construction plans. – Lee Nalley
Chris Marshall: What a great position to be in, Lee: building your dream shop! I’ve had shops with plywood flooring and concrete. Honestly, I’ve found that wearing a good pair of supportive shoes makes concrete as comfortable for me to stand on for extended periods of time as my plywood floor used to be. As you suggest, dense foam or rubber mats, placed in front of your bench and machines, could be another good preventive measure to try. There are also resilient flooring tiles that interlock like a puzzle, or even rolled rubber flooring that could be applied over your slab similar to what you might see in an athletic building. Cost-wise, I’d go with a concrete slab, and start with mats. You could always roll out a rubber floor or lay down soft tiles later. Or even install wood sleepers over your concrete floor and lay plywood over them. Concrete will afford you lots of options, and a slab floor will give the next owner of your shop every alternative for using the building, too.
Rob Johnstone: If I was building my perfect woodshop (and I’ve daydreamed a good bit about this), it would have hardwood floors (wide red oak boards). But my preference would be as much for how the floor would look and feel as its performance. Perfect dream woodshops don’t need to be paid for and don’t take much maintenance. When I build my next workshop, it will have concrete floors.