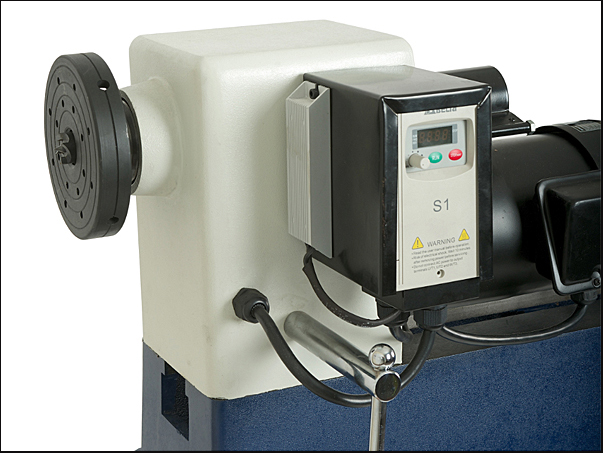
I inherited a lathe from my father that has a four-step pulley system for changing speeds. The lathe has a 7-1/2″ throw, and I would like to turn the largest bowl possible. The slowest speed on the lathe, as far as I can calculate, is 475 rpm. I feel this is a little fast for a chunk of burl that large. Is there a way to convert an AC motor to variable speed? – Rusty Aurand
Tim Inman: Now you’re into my favorite territory. Turning has always had a special place in my world. Most of my work has been restoring the turnings others have done, and turnings typically found on fine furniture. I do turn bone and exotic hardwoods, along with my clock lathe work, too. So, making things round and smooth is fun for me. That said, I’m in total agreement with you that your lathe is going too fast for bigger work. Instead of RPM, think in terms of SFPM. Surface Feet Per Minute represents the “ground speed” of the wood going past your cutter. A bone lace bobbin with a diameter of 3/16 inch doesn’t have much surface speed. A tree stump two feet in diameter makes that treadmill go fast. (I hate math, but these two examples figure out to be this at 475 RPM: Bobbin = 23 feet per minute surface speed. Stump = 2,985 feet per minute surface speed.) The size of the object being turned has a great impact on the cutting speed of the project.
For me, almost everybody turns too fast. More speed usually just means more heat and shorter tool edge life. I like to turn slower – just fast enough to make things work. Remember, all that fine furniture in the museums with exquisite turnings was done with foot treadle type lathes. They were not turning at thousands of RPM. The work speaks for itself. You CAN turn beautifully with slower speeds. It is more enjoyable work, too.
Fast motors are cheaper, though. So with electric motors comes fast spindle speeds. How to slow it down? My best answer, and a choice I use myself, is a jack shaft. Instead of trying to change out the pulleys, add a jackshaft with its own pulleys in between the lathe head and the motor. If you want to see how an old master ivory and bone turner did it, read Bill Jones’ Notes from the Turning Shop. Bill was a personal friend of mine, and his “infinitely variable speed foot pedal” is wonderful. It uses the most simple “old-school” technology, but it really works. If your pockets are deep, and you don’t want to try a jackshaft, then a DC motor is your next best option. Full torque at variable speeds is what you’ll get for your money.
Slow down and have more fun!
Chris Marshall: There’s a reason why typical drill presses and lathes with induction-style AC motors have stepped pulley systems: you can’t vary their operating speed electrically without potentially overheating the motor and damaging it. So, pulleys—or in some cases, centrifugal clutches—provide a mechanical speed-changing solution. I’m sure you’ve considered stepping the speed down further with an even larger/smaller pulley option than your lathe currently has, or implementing the type of jackshaft retrofit Tim suggests above. Some people have tried to slow down AC motors with fan dimmer switches, but I wouldn’t go that option: the motor is intended to run optimally at a constant speed. Rusty, I don’t have a simple solution for you here, but I can speak to safety. If you load 15-in.-dia. bowl blanks on that lathe, use the tailstock to pin them tight against the headstock and faceplate for maximum support. Start with the most round and balanced blanks you can, to try to minimize the initial vibration during the roughing stages. Bolt your lathe down to the floor, and definitely wear a face shield to protect yourself. You are testing the machine’s limits here.
There are true electronic variable-speed lathes with DC motors these days and others that offer lever-controlled, clutch-type variable speed changing. Eventually you might want to step up to one of these. Or, if you keep using your dad’s lathe, just resolve that safety wins out over size, and stick to turning smaller bowls instead.