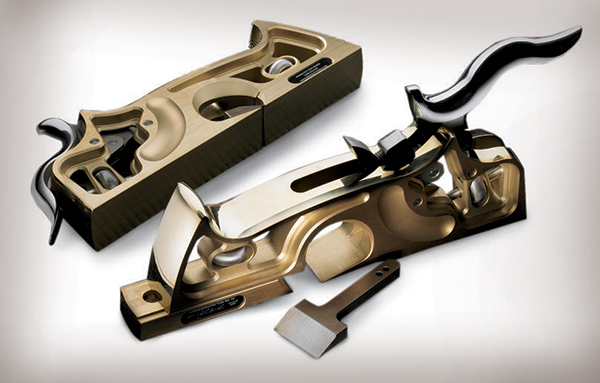
What does a woodworker do when he can no longer do woodworking? In the case of John Economaki, you make tools.
Lead photo: Can you spot the fox in the CT-14 11⁄8″ Foxtail Shoulder Plane?
John, the founder of Bridge City Tool Works, developed a severe allergy to wood dust, likely triggered by rosewood, in the early 1980s. At the time, he was a high-end furniture designer; his “Nutcracker” piece was part of a juried exhibition at the Renwick Gallery of the Smithsonian Institution and later became part of its permanent collection.
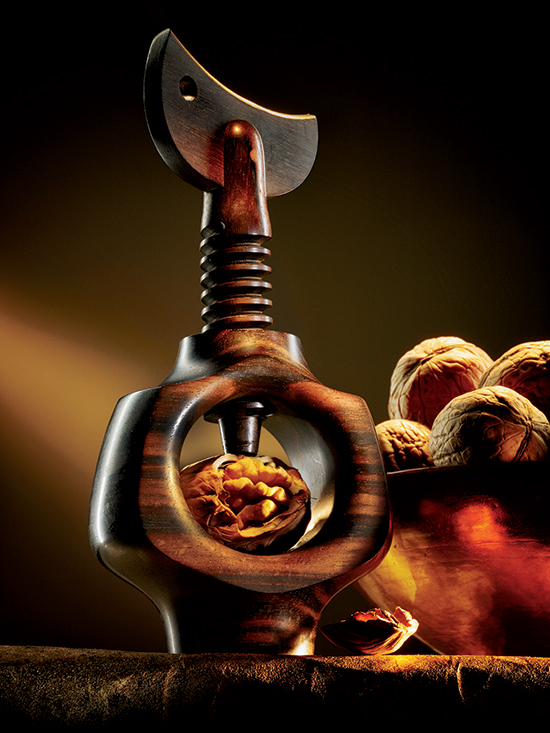
“My heart is in furniture design. The next best thing is living vicariously through the work of others,” John said. In many ways, however, he sees some strong similarities between being a furniture maker and being a tool maker.
“They’re both forms of expression. When I was building furniture, I was doing things that had never been built before. Now, I’m doing the same thing: you use cool materials, and make stuff that’s going to last.”
Durability
Making things that last is important to John, who laughs at software companies promoting their latest launch. “None of that stuff will be around in 15 years, let alone 300,” he said.
Many of the Bridge City Tool Works pieces, on the other hand, have already become collectible. For instance, John cited his CT17 Block Plane and CT18 Bench Plane — designed with a reversible iron, so that it can transform from a regular plane to a smoothing plane to a low-angle plane by switching the iron — “I know enough about the tool market to know that those tools will be highly prized 200 years from now.”
Bridge City’s Commemorative Tool #1, a try-square (pictured below) with an integral bevel in the handle, was made in a batch of 300 that sold for $89 in 1992. “On the market, it will fetch up to four grand,” John said.
The initial price tag on Bridge City tools is not cheap. “The woodworking community doesn’t really get that what I’m doing is expressing myself through tools: they need to be functional and if it sells, great; if not, great,” John said.
“I would get frustrated when people would ask, ‘Does this plane cut any better than this other one?’ I’d answer ‘Probably not,’ and they’d ask, ‘Then why would I spend all that money on it?’ and I’d say, ‘Then don’t.’ I’m expressing myself through the medium.”
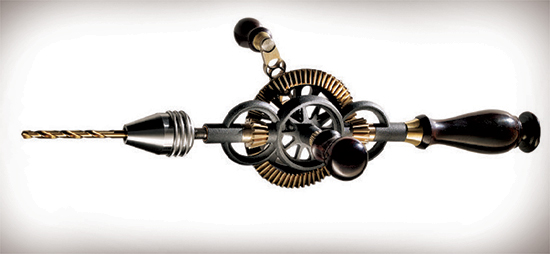
Museum Show
The Museum of Contemporary Craft in Portland, Oregon, has recognized that expression and created an exhibit, “Quality is Contagious: John Economaki and Bridge City Tool Works,” that is currently on display at the Bellevue Arts Museum in Bellevue, Washington.
The exhibit showcases John’s work, from completed tools to prototypes to furniture, as well as that of Joe Felzman, who has photographed his pieces, including Bridge City Tool Works catalogs, for over 30 years. “It’s fun to see tools in that environment,” said John.
Over the years, he said, changes in the business have included a move from addressing ergonomics issues of new tool designs through a series of wooden prototypes, to printing multiple permutations of a design in a single day on a 3D printer.
Bridge City also no longer sells through a catalog, and shuttered its factory in 2002, moving to an outsourcing model. “It’s all made to order; it’s almost identical to being a furniture maker.”
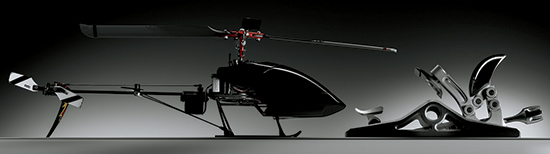
Designs for Downsizing
In addition to new technology, John attributes changes in the business in part to post- 9/11 economics, and in part to changing demographics among woodworkers.
In addition to aging, that group is also downsizing, John said. “My focus as a toolmaker now is on stuff that will allow people to do high quality work in a small space. If you’re going from a garage shop to a condo where all you’ve got is a spare bedroom, you have to deal with not only space constraints, but also do work that does not require a dust collector.”
One of his newest tools, a jointmaker’s saw that requires no dust collection, fits those criteria and has also allowed John himself to do some work with wood again. “We’re reinventing how to make furniture with tools that don’t make dust, even though it seems counterintuitive,” he said.
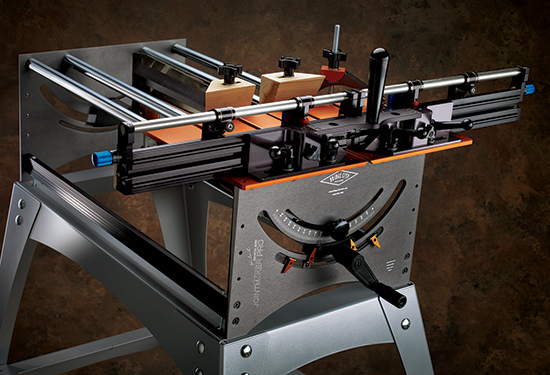
Another current focus, as John watches himself and his customers age, is “taking out all the little inconveniences” of tools, he said. “As I got older, and got arthritis in my hands, tools with knobs: I couldn’t even unlock some of ’em. Now we make a T bevel that has a lever lock on it that can be worked with the palm of the hand.”
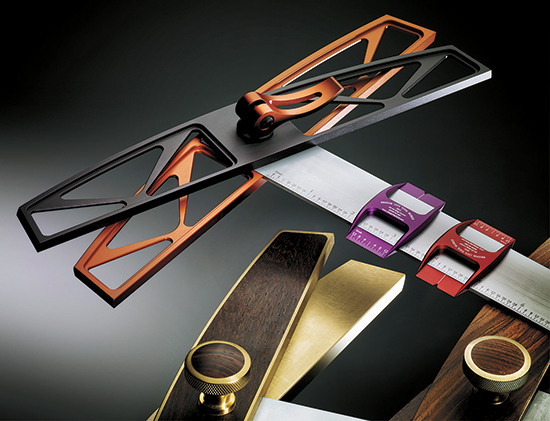
All new designs will take such considerations into account, John said. “From a designer’s perspective, there’s no difference from designing a tool that could be used by a child. If it’s kid-friendly, it’s elderly-friendly.”
Safeguarding Exotics
The first tool John designed was the TS-2 8″ Master Try Square. It was originally a project built and used by his students when he was a high school shop teacher in the 1970s. (He had received a shipment of squares that were out of square.)
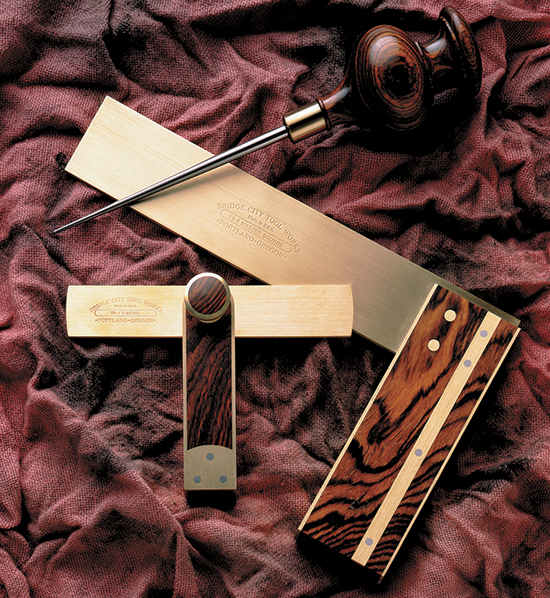
Early versions of that tool, and others for Bridge City Tool Works, incorporated rosewood into their construction. Although John still has a supply of rosewood on hand (purchased before it was included on the CITES Convention on International Trade in Endangered Species) list, he now prefers to avoid using it, particularly for something he doesn’t deem worthy of the wood.
“I used to have a rule that if you were going to use exotics, the piece or the tool should last as long as the tree would have lived in its natural life, usually a couple hundred years. Some monkey gave up a home so you could have a stripe in a cutting board? That’s not right.”
As the title of the museum exhibition indicates, John’s focus is on longevity, and on quality. In the accompanying book, curator Nicole Nathan stated, “There is no separation between craft, design and art with John Economaki.”