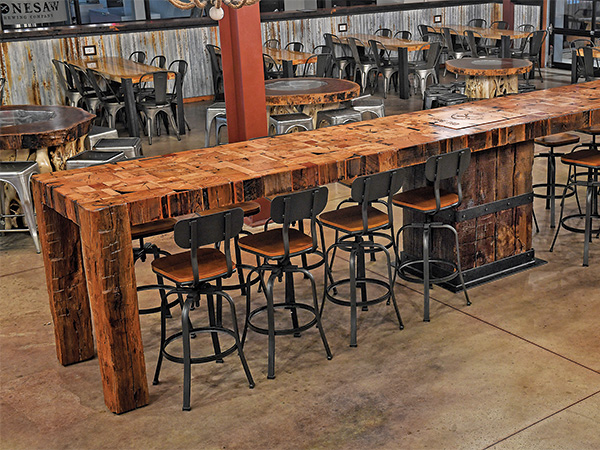
When you enter the tasting room of the Bonesaw Brewing Company in Glassboro, New Jersey, you won’t be able to miss its recently installed tasting table — it quite likely is the largest end grain table in the world. Designed and built by Randy P. Goodman, founder of Random 8 Woodworks in Pedricktown, New Jersey, the table boasts impressive statistics: it is 19’6″ long, 5″ thick and made of 1,008 pieces of reclaimed wood, milled from structural beams acquired from the Philadelphia/south Jersey area. The table’s 485 board feet of wood, plus an angle iron under framework, tips the scales at 1,798 lbs.
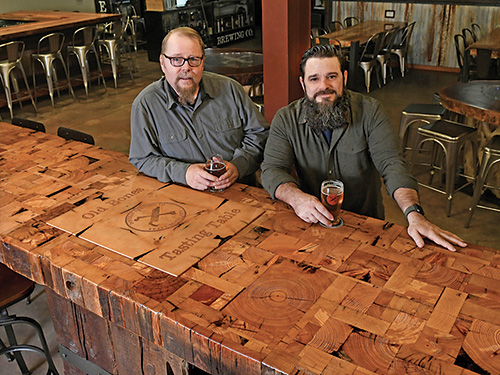
“Guiness does not have a category for this and declined our request for the creation of a new category, saying they consider the ‘largest end grain table’ to be too narrow for their purposes,” says Dorsey Marshall, Random 8’s shop foreman.
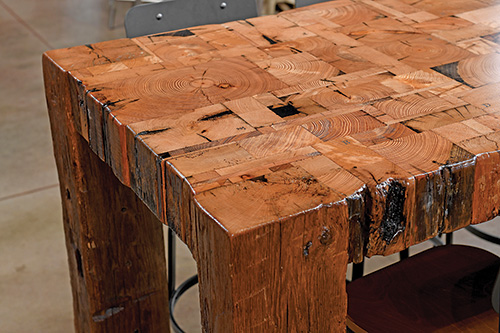
Bonesaw hired Random 8 to create a bar, tap wall, cabinetry and tables for the new brewery’s tasting room. The owner envisioned a large community table that would be situated down the center of the space as its centerpiece. Random 8 was a logical team for the job: the company builds original figured wood and live-edge tables for a variety of clients.
“They trusted me enough to give me complete freedom to design and build the table,” Goodman recalls. “I imagined this hodgepodge of random blocks in a massive, thick table … Once I had the idea, I couldn’t not build it.”
Historic Timbers
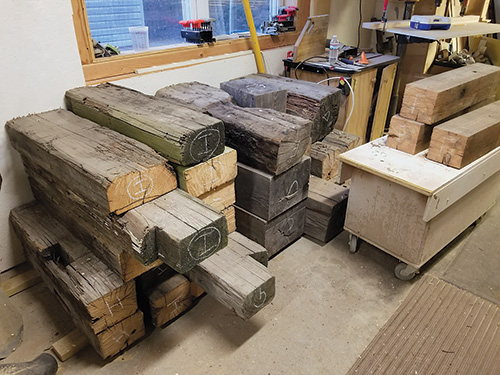
Lockman Hardwoods of Elmer, New Jersey, sourced the table’s timbers, which consist of eight different species: old-growth longleaf heart pine, longleaf heart pine, American chestnut, hickory, loblolly pine, white oak, other pine, Douglas fir and Eastern red cedar.
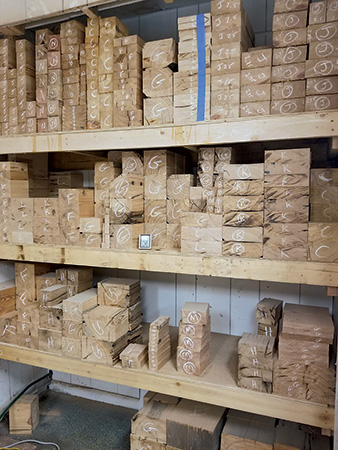
Most of the vintage lumber can be traced to its original structures. For instance, the old-growth longleaf heart pine once formed platform joists and carriage beams in Philadelphia’s Broad Street Station. Its hickory was taken from a house in Salem, New Jersey, that was built in 1744.
Complex, Exacting Build
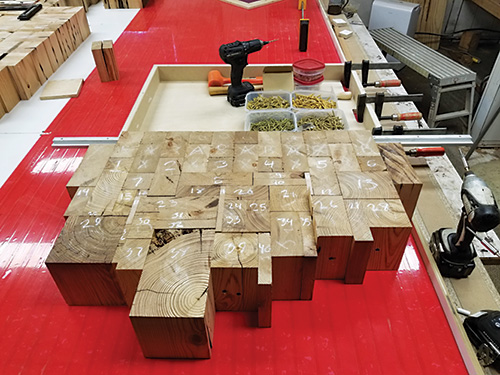
After acclimating in Random 8’s shop for more than six months, the beams were first cut into 6″ blocks of various sizes, according to two Fibonacci sequences.
“Using those fractional Golden Ratio measurements allowed us to create a pattern that fit together and hit our marks in both directions,” Marshall says.
Given the challenges of using multiple block sizes, the tabletop pieces were meticulously cataloged, then assembled with slow-cure epoxy. Blocks were added to the tabletop in groupings of 18″ to 24″. Shop space restrictions required that the top be built in two halves, finger-jointed across the middle and bolted together with 1/2″ steel rod.
In order to prevent tearout and accommodate for multiple wood species with various densities, the tabletop was saturated with epoxy to stiffen the wood fibers and then milled flat with a router and slab-milling jig.
End grain has limited tensile strength, so the tabletop is supported by a welded framework of 3/8″-thick angle iron. “It extends from the center pillar and is mortised into the corner legs,”Goodman says. “Our aim was to distribute weight to the legs and prevent the tabletop from sagging.”
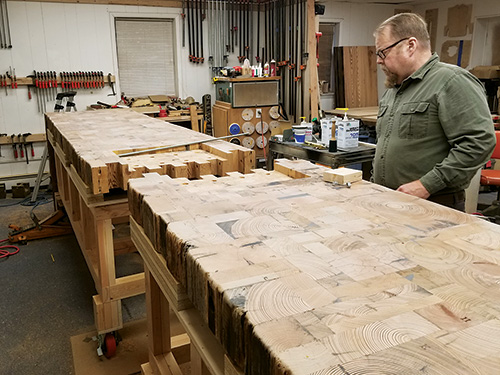
The table’s length, and unevenness in the taproom’s concrete floor, required that each table leg be cut to specific length to suit its exact location on the floor. Lengths vary by as much as an inch.
Marshall says throughout the build, wood movement was a constant concern and was corrected for in various ways. Even now, several months after installation, the table has shrunk about 1/4″ along its length.
Once the table sections were delivered, forklifted into position and bolted together, Goodman and Marshall still wondered if it would be level. But at the moment of truth, “all our calculations were validated and our second-guessing rendered irrelevant. It was dead-on,” Goodman says.
While the Random 8 team reflects that much was learned throughout the yearlong building process, they also wonder how many other important lessons might have flown right over their heads.
“We’re grateful to have had the opportunity, but we never want to do it again,” Marshall jokes. “There’s a reason nobody builds giant end grain tables … it’s really hard.”
Photos courtesy of Craig Terry