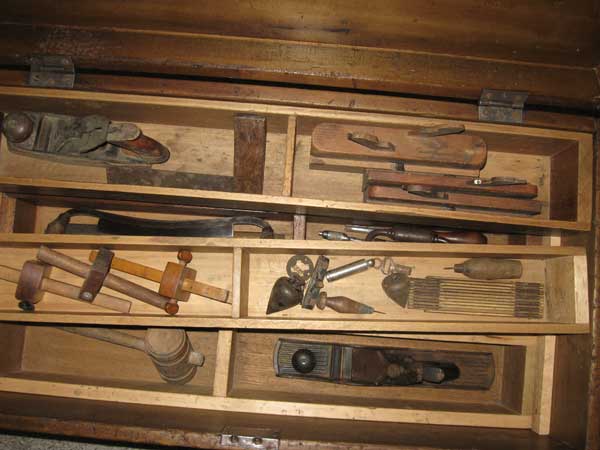
I have a tool chest with all tools which my great-great-great-grandfather used as a cabinetmaker in the shipbuilding trade in England and which he brought to the U.S. in 1832 and started working as cabinetmaker in Rochester, New York, shortly thereafter. The inside of the top is inlaid with a design (marquetry, I think it is called). It is currently painted black, but it appears to have been green at one time based on some earlier paint showing through. My question is whether it would be appropriate to strip the paint off and put some kind of clear coating on the chest. This would show the wood and probably make it a better piece to have in a room in the house as opposed to a very dark piece – it measures 44″ length x 28″ width x 28″ height. Also, some veneer on interior top-level drawers has come loose and a few pieces are now missing — should I have someone repair the veneer and replace missing parts like a puzzle, or leave it alone? If you have other sites for information specifically about tool chests or books related to the topic, I would be interested in knowing about them. – Bob Stiles
Tim Inman: What a prize! I’d take my time and do some homework before I did anything. Consult with professional restorers and conservators. We’re actually pretty nice people, most of us, and we enjoy sharing our knowledge whenever we can. It is both good for business, and good for the material assets that draw our interest to the trades. We like to see things taken care of, and we generally like the people who are interested in doing it. Seeing the project is the only way to get and give good advice. That said, many of these chests started out life as “training samplers” in the apprentice stage of the owner’s life. Building a tool chest can be an excellent training vehicle for an exercise in just about any phase of joinery, marquetry, boulle work, carving and turning. Often, the outside of these chests appears to be pretty plain and simple. They are frequently painted on the outside. Open the box, though, and on the inside it is like seeing Aladdin’s cave. Fancy joints, inlays and the works. As the apprentice became more skilled, he (almost always he) pressed higher and higher with his art to show what he could do. Cabinetmaker’s chests usually do not have handles on the outside. These chests lived under the cabinetmaker’s bench, mostly. Carpenters and other “on-the-job” specialists had handles on their chests. I own the tool chest made and used by the German-American cabinetmaker, August Werner, of 1800’s wooden helicopter fame. It is one of my prizes! The worn cupped surface of the mallets matches the mushroomed wooden handles of the chisels. They tell a story all to themselves, and I wouldn’t repair one thing about them.
Judicious repairs would be my rule: structural repairs, definitely and first. Cosmetic repairs would need more thought before action. Loose and chipping veneers happen because the glue/adhesive is failing or has failed. If the adhesive problem is not addressed before repairs are made, then you’ve just put a Band-Aid® on the problem. Unless a skilled and qualified person does the veneer repair, it is likely that worse damage will happen during the repair than if the site were just left alone. You can learn to do this, but don’t practice on this piece! Practice on scrap until you become highly proficient, and have complete confidence in what you’re doing. This chest is a gem, and needs to be cleaned and polished like one, too. Don’t start regrinding the facets on the emerald just yet….
Chris Marshall: Bob, you are a lucky guy to own this heirloom tool chest! I’m sure you’ve watched those traveling road shows where antiques are evaluated, and the consistent advice is always “do not strip and refinish.” I would probably leave your chest as is and just enjoy it for the historical and sentimental value it has. Leave the “spruced up and polished” look for your new projects and let this old gem show the effects of time and good use. You have a fine treasure!