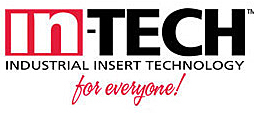
What happens when you hit a hidden nail or screw with a typical carbide-tipped router bit? Quite likely, a chipped or cracked edge. You often get the same unfortunate result when a bit takes a tumble onto a concrete floor…bunged edges. Then what? You probably kick yourself out of frustration and debate about sending it off to a sharpening service for repair. More than likely, though, it ends up in the trash or in some dark corner of a shop drawer, and you’re off to buy a new bit.
What else is a woodworker supposed to do? Well, Amana Tool has an answer and one that many of us hobbyists may not even know exists: Just unscrew the damaged cutter or cutters and bolt in a replacement. How about that for a change? Amana makes this possible, thanks to three lines of router bits that feature insert tooling. You save the bit, extend your tool investment and, once the cutter is screwed in place, are back to routing again. It’s just that easy.
John McInerney, vice president of sales and marketing at Amana, says insert tooling of this sort is nothing new. Industry has been using it for decades, because it makes such simple sense. “You don’t want the downtime that goes along with shutting down a machine to completely change its tooling and re-adjusting it again, or the expense of replacing both the bit’s tool body and the cutter. Changing just the knives is the way to go.”
Amana has been engineering insert tooling for industry for more than 20 years and quality router bits for professional and home shops for even longer. The company was founded in 1973 as a cutter manufacturer for woodworking. “When woodworking started to shift from using stationary shapers to handheld routers, Amana made that transition as well. In terms of manufacturing high quality brazed router bits, we’ve been a leader in the industry all along. In addition, we’ve been an OEM [Original Equipment Manufacturer] bit supplier to many of the major power tool labels for many years.”
The company also makes premium saw blades, shaper cutters, boring bits and planer knives.
McInerney suggested several reasons why Amana retains a dominant position among its router bit competitors. One has to do with material quality. “We know exactly where all of our raw materials are sourced, so we control that factor of production very carefully and select from among the best sources around the world.” Then there’s bit design. “We start with a single piece of steel rod and turn it down to the body you see, as opposed to casting the body from some other metal. That adds durability, balance and longevity to the bit.”
John says Amana is also able to maintain levels of inventory that are larger than some other suppliers, which makes the company better able to react on short notice. “When we commit to make something new to expand our product lines, we commit to it wholeheartedly; we make it in quantities of thousands, not hundreds, so backorders aren’t an issue. We ship immediately and completely to fulfill distributor orders, and we make our products so that they can be easily re-sharpened and serviced.”
The company’s decision to bring insert-style router bits to small production and home woodworking shops happened just a few years ago, but the reasoning is quite practical. John explains that by eliminating the brazing process to attach a cutter to the tool body, Amana is able to use much harder carbide. Harder grades of carbide already exist that can retain an edge longer than conventional router bit carbide, but with increased hardness comes more brittleness. Brazing harder carbide increases the chances of breaking it in the process. If the cutter simply fastens in place on the bit body, brazing heat is a nonissue. McInerney says that the carbide of Amana’s inserts is as much as five times harder than conventional brazed carbide. In addition to improved edge retention, harder carbide also helps the insert bits retain better balance, because premature edge wear can introduce vibration. He feels insert bits are actually safer to use in handheld routers for that reason.
Amana offers three lines of insert router bits. Its In-Tech line most closely resembles the bits we use already. Nine different bit styles, including roundovers, coves, straights, flush-trimmers, rabbet and ogees, are available with 1/4-in. shanks. Either one or two cutters fasten to the bit body with Torx screws. Those bits with straight profiles actually have two sharpened edges, for double the life before the cutter needs to be replaced. While the initial cost for In-Tech bits is 10 to 20 percent higher than conventional brazed bits, the replacement cutters are a fraction of the cost of buying a new bit. An In-Tech flush-trim bit, for instance, lists for $37 complete; the replacement cutter pair costs $15. A rabbeting bit goes for $39.50; the replacement knives are $12 per pair.
In-Groove, Amana’s second line of insert bits, is geared more toward small CNC machine use. Here, instead of a machined body on the bit that determines the cutting profile, a 1/4- or 1/2-in. straight shank accepts up to 40 different knife profiles. A single Allen screw locks the knife to the shank. The carbide formulation is unique for In-Groove bits: since the knife profile stands completely unsupported by a steel body, the carbide must be flexible enough to take a load on its own without breaking. In-Groove bits are made in various engraving points, straight and core box edges, as well as corner round and beading knives. Certain In-Groove knife profiles, McInerney reports, “can’t even be accomplished with brazed bits.” While they are designed for CNC application, In-Groove bits are also suitable for handheld routing. Packaged 8-piece sets of a tool body with a selection of cutters is available, as are single shanks with a specific cutter style. Amana can also mill custom In-Groove profiles for you with a 10-piece minimum order.
Nova bits, a third insert line, more closely resemble In-Tech bits, with one big exception: here, pairs of blades lock onto the bit body with a gap in between them; the empty space facilitates improved chip clearance and expulsion. John says the empty space is beneficial by imposing less drag on the bit during cutting, a much more aggressive rate of stock removal for faster feeding, and a superior cut edge. Another unique feature of Nova bits is that the bodies of some styles can accept multiple cutter shapes. You can change the bit’s profile by simply swapping in a different cutter. Amana offers 40 styles of Nova cutters, which lock in place between top and bottom mounts with a screw. A notch on the blades and the design of the bit body ensure perfect knife registration, and the blades can only mount one way. Profiles include both edge-forming and plunging shapes.
McInerney reports that Amana’s three insert bit lines are still being used more by production shops than “Joe and Jane Lunchbucket” woodworkers, but he says that “serious hobbyists” are also discovering them and making the switch. And, as small-shop CNC machines continue to grow in popularity, so should the market for insert bits. Regardless of how things go from here, though, John confirms that Amana has no intention of eventually moving away fromĀ conventional router bits. “We’re too committed to them, and change happens very slowly in the tooling business…We’ll always make brazed bits.”
But, bringing the convenience and cost-saving possibilities of insert tooling into the hobbyist marketplace was a logical move for Amana. According to John, you could even say it was an eventual obligation. “We’ve got so much hard data from the industrial CNC side that reinforces the benefits of replaceable cutters…It would be a mistake for us not to apply these benefits to the hobbyist woodworking market as well.”