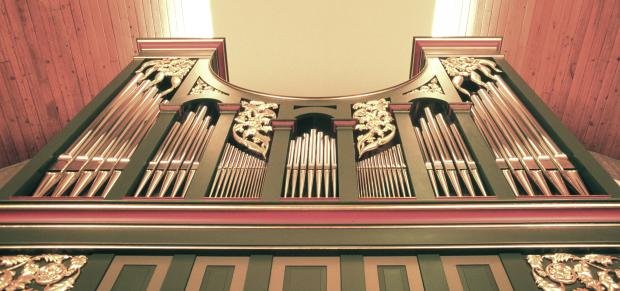
The invitation led my wife and me to an unassuming wood building set well back on a sleepy residential street. Stepping inside, we found ourselves in a grand room with a surprisingly high arched ceiling. A railed catwalk clung to the walls halfway up their 40-foot height. Filling the room, floor to ceiling and almost wall to wall, was a massive and thoroughly breathtaking pipe organ, replete with shiny metal pipes, ornate wood carved screens and figurines, and lush figured wood throughout.
Though a cavernous church would soon be its permanent home, it was on that day assembled and squeezed into this relatively small room. Its sheer mass and exquisite craftsmanship made it most impressive. That feeling quickly accelerated to overpowering as one of the invited guests, a professional organist, sat down at the console of keyboards and made the room fairly explode with heavenly sound.
“Building pipe organs is a calling rather than a job,” explained Paul Fritts, the owner and auteur of Paul Fritts & Company Organ Builders. “You are kind of born to do it, and I was blessed with the combination of skills and abilities, both musical and mechanical, to be able to do most anything that must be done in the shop. I design organs, run the company, build, voice and make key actions.
“I grew up in a rather interesting household. My father was a professor of music at Pacific Lutheran University, and his father was a Lutheran pastor. My father actually built our family home, and it had a shop in the basement with all the typical woodworking tools. I grew up in a rich environment for music, culture and woodworking.
“On the side and during summers, my father rebuilt and modified organs, which sometimes meant making parts like wind chests. I remember helping drilling and assembling with him, and one summer when I was 12 or 13, I went with him to Alaska for an installation for five weeks.
“Though I took some piano lessons in high school, after high school I went to University of Puget Sound to study violin. That was the beginning of my ear training. As it turns out, controlling the tone of a violin is quite similar to voicing an organ pipe. Voicing means adjusting the mouth and wind pressure to the best sound and correct pitch out of the pipe. It is refining sound so that it sounds right at a distance for the listener.
“In the late 70s, after I had left college, my father retired from teaching and became an organ builder part-time. He asked me to come into the business with him, which was housed in our garage and basement. I started to get more serious, and he let me take charge of jobs. I started to become more aware of historically inspired organ building, a movement that looked at the great historic organs, most of which were in churches. I decided I wanted to build tracker organs. My father agreed, and we talked the next client into letting us do a mechanical action organ.
“A pipe organ has pipes supplied with wind, which creates the sound. How the wind is activated defines the difference between the two basic types. In an electromechanical or electo-pneumatic action organ, the air is fed via an electrical switch. On a tracker organ, there is a series of mechanical levers and rods that connect the key that the organist presses directly to the valve that opens the air into the pipe. Everything on a tracker is mechanical; there is no power or electricity required to play the organ. All the technology of tracker organs has been around since at least 1500 AD.
“If you look at the manual, or keyboard, of an organ, above and surrounding it are knobs called stops. Each stop, when pulled, moves a piece of wood underneath the boards on which the pipes stand. These are called sliders. The holes in the sliders correspond to the pipes. When any particular stop is pulled out, the holes line up to allow air into a certain set of pipes, or close off the wind when the stop is pushed in. Stops merely turn a pipe on or off. When you pull out all the stops, all the pipes are playing. The organ is as loud as it can be, and each key pressed plays several pipes. When only one stop is pulled, one key only plays one pipe.
“The pipes stand on a box called a wind chest that channels air into them. The most complex and demanding woodworking in pipe organ work is the wind chest mechanism, which includes the sliders. They must slide easily and function under a variety of humidity conditions without leaking any air or warping. For that reason, we use only quartered material on wind chests, and carefully choose the wood for the purpose. The sliders are made of quartered basswood, the grid that divides the air channels to the pipes is made of quartered poplar, the sides are made of quartered redwood, and the racks that hold the pipes upright are made of quartered oak.
“Eventually, I bought out my father’s interest in the company, along with another partner who had been with us for a time, and moved next door to a 20- by 60-foot building. I’m still in it now, but it has been remodeled and expanded at least 10 times. Eponymous organ company names, those named after the maker, are the norm, both traditionally and today, which is why my company is called what it is.
“Today the workshop has eight full-time and two part-time employees. Our last instrument, for St. Joseph’s Cathedral in Columbus, Ohio, was a two-year project, that cost two million dollars. It sports three manuals or keyboards, foot pedals, 66 stops and just under 5,000 pipes. The organ itself weighs somewhere in the neighborhood of 15 tons. Its largest pipe is 30 feet long and about a foot and a half in diameter, and the smallest is the size of a pencil.
“We cast the metal for our pipes right here in our shop by melting tin lead alloy and pouring it out onto a 12-foot-long stone casting table. Once the metal cools, we measure it for thickness, make necessary adjustments, and roll it into cylinder. Obviously, larger pipes require thicker wall metal. The seam is soldered, the mouth and tip are shaped, the cone-shaped foot is soldered on, and the pipe is smoothed, cleaned and ready for voicing.
“We always make freestanding cases. Our largest was 36 feet tall, 26 feet wide, and nine feet deep. Inside was a staircase and four levels. I called it my four-story condo. Building the case is fairly straightforward woodworking done in all solid wood with post and beam and frame and panel construction, mortise and tenon and dovetail joinery, and hand carved ornamentation. The case must support everything, yet still ensure that all the complex connections that make up the maze of trackers and connectors continues to work flawlessly.
“Sometimes I have organists who come to me with a mission to build organs, but they usually have no idea what is involved. Building an organ is about the craft of woodworking, which can be at times tedious and exacting and monotonous. There are phases, like now, when a finished organ stands in the shop, when there is some grandeur, but in the earlier phase it is all hard work and very little thrill. Still, my employees like the work; some have been with me 16 years. As each organ is completed, we have an open house for anyone who is interested in seeing the shop and hearing the completed organ. I usually invite friends and local organists.
“Those who are into historic building in this country are very dedicated, because we don’t have that history here. It’s not our history; it’s Europe’s history, but because we don‘t have it we tend to value it more. I’m working very hard to keep alive a very old art form because I feel passionate about it and value the art form. I’m one of only six or seven strict historical comprehensive builders in the country. That means exercising various skills, like how to make pipes, design an organ and create a certain sound.
“Each organ is like a child. It has a life of its own and takes shape over a period of months or years, and we coax as much life, vitality and music out of that child as we can. This one that you’re looking at today has 53 stops, took about 20 months to make and will take another three months to install. Seven people will take two weeks for an initial physical setup, and three will remain three more months voicing and tuning the pipes.”
And like any good parent, Paul visits his children whenever he can.
“Because we maintain the organs we build,” he pointed out, “I get to visit my organs every year or so. Each October I go to the East Coast for the organs there. I travel about once a year to Europe to study some of the great organs from 1500 to 1800, and each year I come back with new ideas to try and the desire to do better. Sometimes I will revisit the same organ two or three times, and see different things each time.”