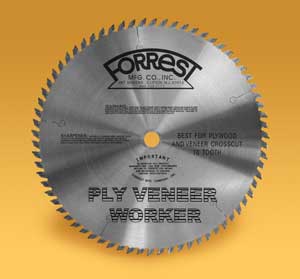
Jim Forrest Sr. is one of those people you meet from time to time who knows so much about a certain subject that even his side comments reveal a level of expertise you don’t encounter often. And it certainly shows in the blades his company makes. The Forrest Woodworker II is usually spoken of with awe, in hushed tones, wherever woodworkers gather. It is often called the standard of quality by which most other blades are measured.
Jim himself downplays the range and level of innovation he has implemented in the design and manufacture of Forrest’s blades. But his offhand comments about controlling the runout and wobble of the sawblades his company makes actually reveal a lot about both the careful manufacturing process and his own attention to detail. For example, his company holds the wobble on the plates (the disk that eventually becomes the blade that the carbide tips are mounted on) to one thousandth of an inch, he explains, because it creates fewer scratches on ridges on the wood when cutting.
Most manufacturers, he says, grind their plates on a mill that holds them in place with a powerful magnet. He doesn’t. That powerful magnet warps the shape of the plate during grinding, so when the magnet comes off, the plate springs back to its original shape. Jim’s plate grinders don’t use magnets; they lay the plate down and let gravity hold it in place during the grind. He then uses softer grinding wheels and grinds the plate slower, taking off approximately five thousandths of an inch from each side. “That takes us quite a bit more time, but that leaves us with a plate that’s basically a lot straighter,” says Jim.
Once they have the plates straight, Jim’s company brazes the carbide tips on the teeth. That’s another area where his blades differ from competitors. His carbide tips don’t taper much. With most tips, Jim explains, the carbide tapers about five thousandths on each side so the tip that bites into the wood is wider than the sides of the carbide teeth. This, he explains, reduces friction between the carbide and the wood, allowing the blade to cut cooler. His tips, however, only taper one thousandth of an inch on each side. Jim says that, while that increases the friction, it also allows the carbide on the side of the tooth to polish and smooth the cut, reducing scratches and giving the woodworker a better edge. It also stabilizes the blade a bit more, reducing wobble.
Jim knows a lot about making blades, though he doesn’t really have an extensive background in machining metal, but he also knows a lot about sharpening them. In fact, his father started the business back during World War II as a blade sharpening company as a way to help out the war effort. That’s where Jim learned about the nature of blades, sharpening, grits and metal. Right after the war, they expanded the business to sharpening a wide variety of tools. While Forrest is known as a company that makes blades, it also sharpens a lot of saw blades, of every make and model, every month. “We treat the competitors blades with the same care that we do our own,” says Jim.
In fact, he gets feedback from some customers that the blades cut better after his company has sharpened them than when they bought them directly from a competitor.
As the business grew in the 40s and 50s, Jim talked with companies that wanted him to manufacture their blades for them. Unfortunately, they didn’t have the same exacting standards that he had, so he started designing and making his own blades. The lessons he learned while designing his own line of indutrial saw blades gave him the engineering expertise he needed later, when he introduced his own line of woodworker’s blades and chopmasters.
The blades took off. Woodworkers started buying the Woodworker I, and later the Woodworker II, in droves. His father took over the accounting and bookkeeping end of the business while Jim designed both blades and manufacturing processes that guaranteed the best blades. “I knew what had to be done to make a sawblade cut smoothly,” says Jim.
One of his innovations was the use of multi-grit grinding wheels. He decided that, to get the best edge on the blades, he needed wheels with two, three and four different grits built into the wheel. So he went to the manufacturers of his grinding wheels and told them what he wanted. It was a first, but they managed to deliver the multi-grit wheels and his company has been using them ever since.
Jim Sr., after 50 years of making and designing blades, is now semi-retired. His son Jim Jr. runs the factory, and his other son, Jay, runs the business offices. So the Forrest Manufacturing company is in good hands and will remain a family business well into the future. In his spare time, Jim Sr. also runs a small airplane business, Forrest Aviation, and spends more time with his family and with his church.
Nevertheless, he still keeps an eye on the blade business, and he and his sons are expanding the capacity of the manufacturing plant dramatically. While demand for the blades has always been high, Jim is both surprised and pleased at recent increases in demand for his high quality blades. He and his sons are doing everything they can to fill the orders while always, always adhering to the strictest quality standards.
– Bob Filipczak