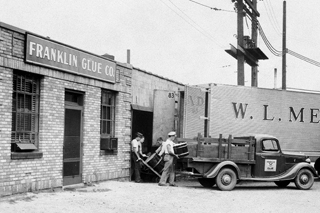
When you consider some of woodworking’s modern conveniences — things like blade brakes, CNC machines, Lithium-ion batteries, carbide cutters — glue probably doesn’t come to mind. But glue has come a long, long way. Back in mid 1930s, there was hide glue and, well, not much else. In order to use it, you had to heat up the dry glue pellets, wait for them to melt, mix it and then cool it before a glue-up was even possible. And then, considering its extremely short shelf life, anything left at the end of the day needed to be tossed and the glue pot cleaned out.
Imagine having to do that now. Just preparing a batch of glue could kill an hour of a Saturday afternoon, if not more.
If you’re still inclined to use hide glue these days, you can pop open a squeeze bottle in a few seconds, and that classic brown glue is ready to go. For that, you can thank Franklin International, makers of the Titebond® family of woodworking adhesives, including Liquid Hide Glue. The company was first to introduce hide glue in a one part, ready-to-use formula in 1935. That product was a revolution in woodworking glue, and it was the first in a long line of convenient adhesives available to us today from the same source.
“Our founders, Langdon T. and Mildred B. Williams, had a real passion for business and technical support. “At that time, furniture makers had to guess how much hide glue they were going to need for the day. The process for making it was slow, and the waste factor was awful … The Williams saw the bigger picture and invented a product that was quickly embraced by woodworkers as a better way to assemble furniture. By no longer having to heat, mix, cool and then clean up the glue, Franklin significantly improved the efficiency of project assembly.”
That first no-mix hide glue formulation is actually the same one the company still uses today, and Ford says many wooden instrument makers and furniture restoration specialists wouldn’t be without it.
Franklin’s next major breakthrough came shortly after World War II. There was a push in woodworking circles to use white polyvinyl acetate (PVA) glues that were successful in the packaging industry. The trouble was, the glue had poor heat resistance. Sanding that PVA glue would cause it to melt and gum up the abrasives. Furniture assembled with PVA and left in direct sunlight could literally fall apart in the heat, Ford says.
Again, woodworking needed a better general adhesive, and Franklin’s solution was the aliphatic resin-based Titebond Original, “which offered significantly better heat-resistance and also demonstrated an outstanding initial tack. The application of aliphatic resin as a wood glue was innovative. It was a first-to-market situation for Franklin. Titebond Original’s yellow color also made it easy to distinguish from other white glues.”
Since that time, Franklin has ushered in various other Titebond products that, to one degree or another, have “broken the mold” for woodworking. Titebond II Premium and III Ultimate adhesives provide increased levels of water resistance, with Titebond III being the first woodworking glue to pass the ANSI Type 1 standard for water-resistance; it is waterproof. Three variations of Titebond II include a brown formulation for dark woods, one that fluoresces to make glue lines visible under black light and a slower set-time Extend option. The company’s HiPURformer glues offer the durability and versatility of polyurethane in a cartridge hot-melt gun dispenser. There are also Franklin Instant Bond cyanoacrylates in four viscosities for a range of different project applications. Recently, two new glues have been added to the Titebond family as well: a No-Run, No-Drip thixotropic blend for installing molding and trim, and Titebond Translucent, which Franklin says provides “a virtually invisible glue line.” There are also Titebond adhesives for melamine and cold-press work, plus other applications for professional cabinetmakers.
Ford explains that Franklin’s extensive product line and corporate culture embrace the Williams’s original commitment to innovation and product development.
“Our leadership (now third-generation members of the Williams family) has structured the company to succeed in both short- and long-term research and development goals … Back in the 1990s, we launched a Core Technologies Laboratory staffed by a team of chemists and technical specialists that are totally invested in future product development. They’re working on a long-term timeframe of 5, 10 and 20 years, as opposed to 18 or 24 months.”
Nick says that Franklin also takes education very seriously. The company spends about 25 percent of its annual advertising budget on awareness and education. Those monies are allocated in many different ways, from updated product literature and instructional videos on YouTube to focus groups, trade show booths and support of woodworking schools, such as Marc Adams School of Woodworking. “We are a current sponsor of Tommy Mac’s ‘Rough Cut Woodworking’ show, because we believe it appeals to younger woodworkers who are just learning the craft.”
Franklin also staffs a technical service product hotline during regular business hours. Ford affirms their efforts. “We take great pride in our five technical specialists that answer end user phone calls. We have resisted the urge to use a menu-driven phone system. If you call between 8 a.m. and 6 p.m. EST with a question about our products, you will speak with a human being. They are coached to answer your questions and suggest the best adhesive to meet your needs even if that means it is something outside of our product line. That’s really critical to our corporate vision.”
Customer feedback, which channels back to Franklin International’s Columbus, Ohio, headquarters, does have impact. For instance, the new Titebond Translucent Wood Glue was invented in response to a survey of woodworking students that wanted more invisible glue lines. Franklin hopes the new glue will help both amateur and professional woodworkers achieve better results. It’s nontoxic, so a safe glue for introducing children to woodworking.
Ultimately Franklin’s mission has remained the same since that first game-changing no-mix hide glue back in 1935. “We want to be the most trusted adhesion company in the world. But equally important, we are committed to the success of your woodworking projects.”