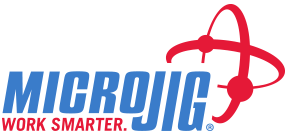
Gazing at the shingle cutting machine at the Washington State History museum is enough to give a modern woodworker chills. Shingle weavers, as they were called, pushed blocks of cedar through a large, unguarded saw blade with hands perilously close to the teeth. Lost fingers, and worse injuries, were common. With that in mind, it’s not hard to imagine a worker deciding it was safer to push with wood scraps, and thus creating a primitive push stick.
We’re a lot luckier today. The push stick, an absolute must-have safety item for the table saw, has come a long way. Each new generation of tinkers refines it further, but I think I have finally seen the state-of-the-art. That conviction came after watching a demonstration of the Microjig GRR-Ripper. As is often the case, this amazingly versatile improvement on the push stick grew out of frustration.
“For about five years, I was an importer and exporter of tropical fish,” explained Henry Wang, the GRR-Ripper’s inventor, “then spent 10 years running restaurants. That business involves a lot of renovation, which in turn involves a lot of woodworking. Having counted woodworking as my hobby for some two decades, I did much of the work myself.
“Around 1999, I found myself having to cut and glue a lot of very narrow strips for laminated cutting and chopping boards. For safety, I would only cut them from the offcut side, which means you must move the fence and recalculate for each cut. By the time you get the board down to about four inches, it is too narrow to cut safely with typical push blocks. That was wasting material. Like many woodworkers, I was always seeking jigs and methods to build things easier and quicker, so to solve that problem, I came up with what would eventually become the GRR-Ripper.
“As I got older, the hours in the restaurant business started to wear on me. I wanted to cut back but also wanted to spend more time doing woodworking. I felt the GRR-Ripper was marketable, so I left the restaurant business in 1999 to devote my time to develop it. I made about 45 different prototypes over the next two years before coming up with the model you see today. Since then, I have added more components that let it do even more and give it even more versatility. Our DVD shows more than 30 different applications for it, and there are still more.
“In a nutshell, the GRR-Ripper is an adjustable push block that holds the wood on both sides of the blade. That not only gives you total control of forward motion, but also allows you to safely keep the stock against the fence. Moreover, it protects your hands by completely covering the blade. The original has an adjustable handle so you can secure it directly over the cut line, the ideal spot for it. An optional MJ Handle Bridge gives you four-point contact and allows you to cant the handle at an angle, which makes it even easier to keep pressure against the fence.
“My intention in designing it was to solve the problems inherent in existing push sticks. For instance, a narrow push stick that hooks to the back of the board gives you no control in keeping the wood against the fence. Sometimes those thin push sticks even push the back corner of the wood toward the fence, making the front corner head out toward the back of the blade. That’s a recipe for kickback. The other problem with hooking push sticks is that they don’t work with stock that extends off the front of the table. On the other hand, most push blocks that are wide enough to offer control of the wood are designed to go between the fence and the blade, but that limits you in width.
“The GRR-Ripper solves all those problems. It is designed with a flat side that rides along the fence, keeping the push stick itself moving in a straight line. The bottom is covered with non-slip sticky material to hold the wood securely without leaving residue. Once you grab the wood with the GRR-Ripper, you can keep it properly oriented and going in a straight line relative to the fence and the blade. Two long feet on the bottom straddle the blade so that the wood is both held and pushed securely on both sides of the blade. Because the gripper is rigid and the feet grab the wood, there’s no chance of either side of the wood slipping or tipping into the back of the blade.
“In essence, it applies pressure in three directions to the wood on both sides of the blade: forward pressure, downward or hold-down pressure and pressure to keep the board against the fence. As you use it, the blade passes through a tunnel under the GRR-Ripper, making it a sort of blade guard that travels with your hand. In a sense, it does everything your hands do without letting them get to the blade, but because it controls both sides, there is no need to use either hand to push stock or guide the wood. Thus, you have complete control and total safety, but there’s more.
“Look at the GRR-Ripper and you will see three legs, all different widths. All three legs are removable, and both the handle and center leg are adjustable. One side has a quarter-inch leg, which lets you rip down to a quarter inch wide without damaging the unit. The other side is a half-inch leg, and the center one is one inch wide. The center leg slides back and forth between the other two legs to provide complete support while still missing the blade no matter what the width of the cut. The handle moves the same way, so your pressure is always where you want it.
“The GRR-Ripper itself is three and five-eighths of an inch wide, so the only problem you can run across is if you have to make a three-and-a-half-inch cut. To solve that problem, you can add a spacer to the side, or remove one leg to give it a two-legged stance. Furthermore, you can use it for both routing and sawing operations in a host of different configurations. When routing, you can even prevent the wood from moving into the outfeed fence at the end of a cut; the gripper keeps the wood in its original position from the start of the cut because it rides against the fence instead of the wood having to do so.
“Because it is so secure, you can even cut wood that is not against the fence. Because the GRR-Ripper holds the wood, and because one side is square and flat to travel along the fence, the board itself does not have to be against the fence. Thus, you could cut a freehand taper safely without a taper jig. You can even safely cut a straight edge on stock with two irregular edges. It will do bevel cuts using two hands, cut veneer at an angle, or make repeat crosscuts, all safely and with no other jigs. Since both pieces of the wood are being held, neither side can fly up in kickback.”
While it is certainly the headliner on the Micro Jig website, the GRR-Ripper is not Henry’s only product. He also offers the pop-in, pop-out MJ Splitter, a small splitter that sits securely behind the blade. “The holes in which the splitter sits are accurately drilled into a zero-clearance throat plate using a supplied hole drilling guide,” Henry explained. “The splitter kit comes with the guide, a sized drill bit and two polycarbonate splitters.
“Each splitter is two-sided. The plus sign on one side indicates a three-thousandths offset. By flipping the splitter over, you can tighten up the gap between board and fence by three thousands of an inch. That makes the splitter act like a gentle featherboard rubbing against the side of the new cut and helps the stock stay against the fence on the far side of the cut. Other splitters have six- and nine-thousandths offsets, should you need it.”
Finding one won’t be difficult, since for years the GRR-Ripper has been the number one seller at many woodworking shows, and is available at most woodworking specialty stores. Many also carry the MJ Splitter system as well.
There is one thing I must warn you about, though. When you get the GRR-Ripper, you must assemble it yourself. That’s intentional. “I want the user to understand completely how this tool works,” Henry insists, “and assembling it is the best way to do that. We do make it easy, though. For example, to make certain that you don’t lose screws when assembling or changing configuration, the screws are held in place by tiny O-rings.
“The bottom line is that I truly hope all my customers enjoy woodworking, but to do that, you must stay safe. The whole point of the GRR-Ripper is to make woodworking more enjoyable not only by helping you work safer, but by making your cuts cleaner and more accurate as well.”