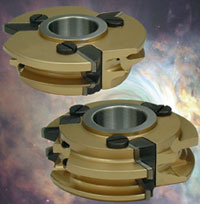
As amateur woodworkers demand better and higher quality equipment, they are turning to tools once restricted to the industrial side of the field. When they add shaper cutters to their shops, many are discovering new sources for both cutters and router bits. Even companies like LRH Enterprises that consider themselves to be primarily an industrial tool manufacturer are now developing products for small commercial shops and high-end users.
We talked to Norm Hubert at LRH to find out more about his company and their products. The family-owned company was started in 1975 by Leo Hubert, Norm’s father and the L in LRH. Leo had a saw shop in Santa Barbara and decided there was a need for standardized shaver cutters. Up to that point, Leo, like everyone else, custom-made all the cutters and customers often had to wait up to six-months for replacements. So he asked his two sons, Norm (who was then regional manager for a greeting card company in San Francisco) and Ralph (who was working at an LA saw shop) to come home and help him set up the new business.
“Our market was the industrial sector of the woodworking industry. We decided to start with the most difficult patterns first,” Norm recalled, “and we standardized a system where we could manufacture male and female cutters that would fit perfectly every time, and they wouldn’t have to come back for adjustments. We started out dealing locally, then we started doing the trade shows, and then we started advertising nationally.”
The company’s first products were component cutters that could be purchased in sets or individually. Woodworker could buy these cutters face-up or face-down, with a 3/4″ or 1-1/4″ arbor holes, and it wouldn’t matter whether they were cutting clockwise or counter clockwise. Those products evolved into the King Cutter line. As the company grew they had to decide what sort of distribution network they’d develop. It would have required a 300-strong sales force to cover the entire country, so they opted for a distributor network. The secret to the company’s success has been its emphasis on high-quality products.
“We don’t like problems,” Norm explained, “so we go out of our way to make a good product that won’t have any problems for the customer. That’s why we do some of the things to our production products that other tool manufacturers only do on their custom work. Everything is done on a CNC machine. Some applications are still more efficient done manually, but the majority is all automated. Another key difference? Whether it’s a router bit or a shaper cutter or custom or standard, anything that comes out of here gets balanced.”
Balancing eliminates vibrations. According to Norm, to get a true and accurate balance, LRH is the only company that hones its center holes. Why is honing so critical?
“Let’s say, hypothetically, there are 16 processes to building a cutter,” Norm explained. “Our first step is to drill a hole slightly undersized. Then the cutter gets milled, faced, traced, and carbide tips are welded into place. You’ve created some heat that causes steel to expand and contract and that once perfect hole might have been distorted. That’s where the honing part comes in. We hone it out to full size and remove any distortion that might have occurred in the process. When it’s done everything is balanced and true.”
Another difference involves the way LRH attaches the carbide or other alloy tips to its cutters.
“Carbide is notoriously fragile and cracks easily,” Norm noted. “We use a wafer welding, where there’s a copper shim placed between the carbide tip and steel body, and this acts like a shock absorber. Since this also allows us to sharpen the carbide to almost paper thin, you’re not going to fracture the carbide.”
LRH’s product line has expanded greatly since 1975. They got into the router bit business when Porter-Cable came out with its multiple-speed routers years back. Reducing the speed down to 8 or 10 thousand rpms allows the use of bigger router bits. To provide these bits for existing router bit manufacturers, the company was able to use its shaper cutter-making equipment to make 1/2″ bits with up to 3 to 3-1/2 inch diameters. They also ended up creating their own standard line of what Norm called odd-ball router bits that other manufacturers don’t want to mess with.
More recently, LRH began meeting a new demand for insert tipped tooling and has become a prime supplier for the industrial market. It’s pricey equipment strictly for high-end production. When a regular braised tool is sharpened, the pattern shrinks. But when an insert tool gets dull, you simply throw it out and replace the set of inserts.
“But one of our hottest things right now in the consumer market is the Magic Molder,” Norm explained. “It’s designed to convert a table saw into a molder — it’s the only one on the market for a table saw — and we’re having a hard time keeping up with the demand. It acts like a dado head set. It’s anti-kickback, it’s got a limiter, and it’s the only carbide-tipped molder on the market for a saw.”
“We’re having a good time,” noted Norm. “The key is that everything is under one roof, so we control manufacturing from start to finish. And that’s why we can back our products 100 percent.”