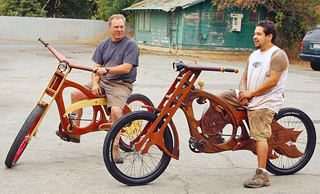
What were a couple of enterprising woodworkers to do when the economy turned sour in 2009 and clients stopped calling for custom work? For Bill Holloway, proprietor of Masterworks Wood and Design, and Mauro Hernandez, the partners started thinking outside the woodworking “box.” Instead of being resigned about their situation, they channeled creativity into the downtime and started building wooden bikes.
While the switch to wooden cruiser-style bikes might seem like a radical move, it actually wasn’t outside the realm of possibility for Holloway, who has built his reputation in the San Jose, California, area as a woodworker willing to take on nearly any challenge. The company’s “bread and butter” jobs are anything but typical cabinetry, stairs and trimwork. Holloway prefers to design and build one-of-a-kind installations: gates, arbors, hand-carved moldings and details, custom doors and even whole-house woodworking restorations.
“We almost never build the same thing twice here, and we don’t build cabinets,” Holloway says. “We also don’t use a CNC for our bikes or any other woodworking that we do. It’s all conventional woodworking machines and hand-tool work. I don’t even own a dovetail machine … I AM the dovetail machine.”
Prior to establishing Masterworks in 2008, Bill was working as a finish carpenter for several construction companies. Before that, he had spent 18 years on his knees installing resilient flooring and carpeting. A staph infection in one of his knees forced him out of the flooring business, and he wasn’t willing to take disability as an option. Instead, “the State of California paid my way to get my Contractor’s B license. That allowed me to do almost anything I wanted in construction, and it got me back on my feet.”
What Holloway really wanted to do was woodworking full-time. Even though his prior experience as a woodworker amounted mostly to small projects for his wife, and he had no formal training in the craft, woodworking had an artistic and creative appeal to him that was compelling. He decided to take on a “crazy complicated” ceiling project in a Mt. Hamilton ranch home renovation. “Other finish carpenters wouldn’t touch it, but I ended up spending three months there to complete it. “That led to more ambitious home-renovation jobs where Bill did all of the interior woodworking. Eventually, he found himself running a custom woodworking shop for another owner and overseeing six staff people. It went out of business in 2008, and Bill decided to go out on his own. Mauro, also a self-trained woodworker, left his prior work as a landscaper to help Bill start the new 4,800-square-ft. business in San Jose.
And then the economy tanked.
Bill recounted that the first bike Masterworks built in 2010 was on the suggestion of a friend and fellow cyclist when times were really slow. “We built it from off-the-shelf plywood we bought at Home Depot,” Holloway muses.” It took us about three weeks to figure out the design and then build it. Before that time, the only wooden bikes I had ever seen were made of plywood for little kids, so this was completely new to me. But I’ve always been into bikes — fixing broken chains and flats. I was the first kid in my neighborhood to ride a full-size bike, and I was just four years old. Then I became the neighborhood bike mechanic because my parents didn’t have money, and I figured out that repairing them made them last longer. Eventually I got into mountain bikes and motorcycles … the whole works.”
After that first prototype bike, the nine bikes that have followed have grown in complexity and sophistication. Holloway estimates there are 18 to 20 major wooden parts, some made up of multiple laminations and numerous smaller pieces, “and we try to get as much wood into them as we can.” The primary components of require about two sheets of 1/2-in. maple or solid mahogany 9-ply multi-plywood. It’s sandwiched by solid wood and then vacuum-bagged into laminations. From there, a system of templates — some used for routing and others for drawing parts to shape — are employed. Other wooden parts include the front forks, handlebars, fenders, seat, and a crossing member. There are no metal fasteners between the wooden components, Bill says. Only dowels and glue join wood to wood. Most of the shop’s woodworking tools are involved in the construction process, ranging from a 16-in.-wide jointer to a collection of hand planes, carving tools and files.
Of course, some parts of a working bike can’t be made of wood, and Bill adds that these bikes are designed to be ridden, not just displayed. The rims, spokes, axles, cranksets, pedals and bearings are conventional items, but several of the specialized metal components, such as the axle dropouts, are made of aluminum and machined by Holloway. “We use all sealed bearing cartridges and only the highest quality components for what we can’t make ourselves,” Holloway says.
It takes roughly 80 to 85 hours, mostly after the workday ends, for the two woodworkers to build each bike. Bill does most of the new design work for each model as their styles change, and Mauro carries out the elaborate carving work when needed. Carved bikes take much longer to complete. All nine bikes are available for sale, and prices start at around $6,000.
Holloway adds that one aspect he’s proud to integrate into both the bikes and other woodworking commissions is reclaimed urban lumber. It’s an effort he’s always felt strongly about. “I just hate to see neighborhood trees being ground up in a mulcher or, worse, headed straight to the landfill. But it’s taken many years to develop the connections and means to handle those trees myself when the city doesn’t want them.” In fact, it requires a network of friends for Holloway to turn boulevard logs into useable lumber. He now knows three arborists that fell the trees, and another friend owns the portable sawmills for cutting them into green lumber. Still another friend allows Bill to store some 30 to 40 logs and drying lumber on his property before they make it into the Masterworks shop for final drying and use.
“Right now, I’ve got about 15 different species on top of a couple thousand board feet of walnut and oak. Most of it comes from San Mateo, where the property owners once planted these elaborate gardens. The options are a lot more diverse there than here in San Jose.”
Among the more unusual species, Holloway has avocado, camphor, black acacia, casuarina, madrone and New Zealand tea tree. He owns some 56-in.-wide black walnut and has a supply of 4-ft.-wide, 22-ft.-long redwood. But the appeal of having such a diversely stocked lumber rack is still secondary for Bill to his desire to make good use of what would otherwise be wasted.
“Now with the growing awareness of ‘going green,’ people are starting to listen to me and see the real value of reclaiming these trees.”
Looking ahead, Bill and Mauro hope to continue building more bikes, but other commissioned work is keeping them busier these days as well. The two are currently completing the interior woodworking for a restaurant using all reclaimed lumber, plus a long-term commission to restore all of the woodwork in an Arts and Crafts historic home. But, he admits to having plans on the drawing board for a bicycle taxi made of wood. Someday, he’d even like to offer classes on building wooden bikes at the shop. If bike building becomes a viable business, that would suit Bill fine. Otherwise, he and Mauro are happy to build them for their own gratification and the “mob of attention” they get when riding them.
“I just think as a woodworker and a person, you should never put limits on yourself or use the lack of formal training as an excuse for holding back. Don’t be afraid to try new things or to make mistakes. It’s what you do with those mistakes that makes all the difference sometimes.”