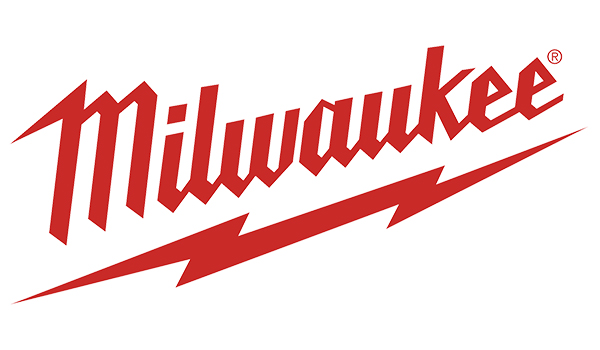
Last week, Milwaukee Tool held their 2017 New Product Symposium, where they brought several members of the tools and trades media together to show off the tools they’ve been developing and will be bringing to market over the course of the next year.
The big news for woodworkers? The M18 FUEL™ 7-1/4 inch Dual Bevel Sliding Compound Miter Saw that will be available in September. It’s made to be lightweight, at 28 pounds with the battery pack. It bevels left and right with hard stops at 45 degrees and 48 degrees and, according to the presentation, will make up to 600 cuts per charge on one M18 battery.
To go with that miter saw, they’ve also come out with some accessories, including a Miter Saw Stand equipped with a bracket system to fit all brands of miter saws. The stand has a capacity of over 500 pounds and weighs 31 pounds. Additional optional accessories for the stand include a Carry Strap and a Table Top work surface that attaches to the stand – it’s meant to be a place to put your safety glasses, pencils, tape measures, etc. The miter saw accessories will be available this month.
One of the other tools they showed us is the M12™ Stapler, a cordless 3/8-inch crown stapler designed to be 35 percent lighter and require 80 percent less muscle effort than other crown staplers. How do they measure muscle effort? Well, as of 2016, Milwaukee now has an ergonomics department led by a certified ergonomist, Raffi Elchemmas. He’s the guy in the lab coat in the video – but not all of their testing takes place in the lab. They also do ergonomics tests in real-life test environments where people are using tools on a day-to-day basis.
It’s hard to hear in the video (there were people in the background doing things like playing with drain clog-clearing plumbing tools), but the diagnostics tool being used is an electromyography (EMG) machine that measures the electrical activity in up to 108 muscles. You see the spikes in activity on the readout screen behind me in the video: when I pick up a tool, and when I compress the Milwaukee stapler or the manual stapler. You can follow the correlation between the actions and the line graphs in the video on the EMG or, what I actually find visually easier, watch the fluctuations in the bar graphs below the EMG’s video screen. By feel, would I guesstimate the Milwaukee crown stapler required 80 less effort than the manual one? It’s hard to say – but the Milwaukee stapler was definitely easier to use, and I really did have to use two hands on “Brand X” to fire even one staple.
On the other hand, it’s a company with a long history, dating back to its founding in 1924. And, three years ago, in 2014, Milwaukee Tool acquired another long-established Wisconsin company, EMPIRE® Level, based in Mukwonago, Wisconsin, which was founded in 1919. EMPIRE was the brand that introduced tools like the Torpedo Level and the Magnetic Level.
As part of this year’s New Product Symposium, we toured the EMPIRE headquarters, which are – now — full of high-tech machines like a 450,000-ton hydraulic press for making rafter squares which was custom-designed for EMPIRE. (That one’s camera-shy and requests “no photos, please”; the one you see in the photo is its 1,000-ton hydraulic press cousin.)
As of the beginning of 2016, however, there were no robotics in the EMPIRE plant. By the end of last year, there were 14; by the end of this year, there should be 20. Business has doubled since the Milwaukee purchase. What makes EMPIRE director of operations Steve Mellensack the most proud, however, in all of these upgrades, is that there have been no layoffs at EMPIRE. Instead, training has provided skills upgrades for the 210 hourly employees at the plant, which continues to produce new products like the UltraView™ LED Torpedo Level. A patent-pending system of dual ultraviolet LED lights surround each vial for maximum visibility – and, as seen in the video, it’s built for sturdiness to stand up to drops in jobsite conditions.
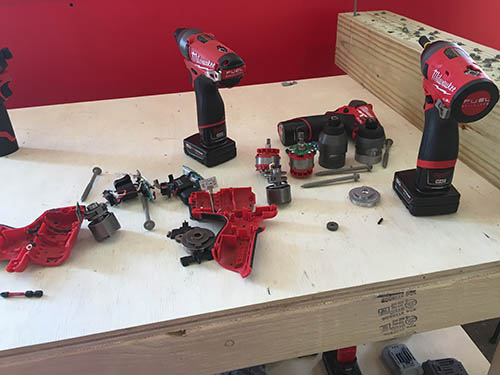
Other news from the Milwaukee Tool New Product Symposium? Well, there’s a new Hole Dozer with Carbide Teeth, a new M12 FUEL 1/2-inch Drill Driver, M12 FUEL 1/2-inch Hammer Drill and M12 FUEL ¼-inch Hex Impact Driver, all coming out in December. They’ve reduced both the weight and the size of the drills and drivers by shrinking the sizing of all three components of the tools: the motor, electronics, and gear core.
We also saw new developments in lighting, clothing, and dust collection. And learned that Milwaukee will be greatly expanding their tool storage options with the introduction of their PACKOUT™ Modular Storage System. The proprietary Mod-Lock™ attachment system allows toolboxes, organizers and soft-sided totes of multiple sizes and configurations to stack and lock together. The PACKOUT system will launch this September with three toolboxes, two organizers and three storage totes – but the Milwaukee reps at the show promised more to come. (Oh, and they also mentioned that they’ll be coming out with a Milwaukee Jobsite Cooler in October. Although the 18-can unit with a combination tape measure clip/bottle opener on the side wasn’t quite ready for its own prime-time spot in the tool presentations, they did use it to contain some of the beverages for lunch at the event.)
And, while (I hope!) yellow caution tape is not a staple in woodworkers’ shops, it was pretty cool to see it being made through the blown film extrusion process at the EMPIRE Level plant.