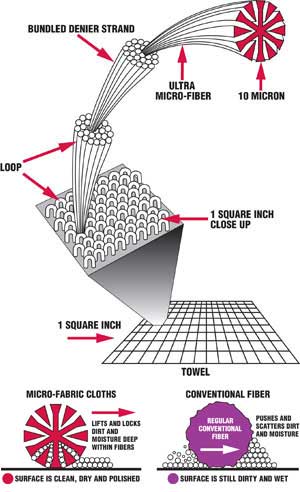
“It’s not easy being green,” laments Kermit the Frog, one of the Muppets, and that sentiment is quite true of wood finishing. With the advent of water-based coatings came a spate of problems eventually traced to the sandpaper and tack cloths that had worked beautifully with solvent-based finishes. Not surprisingly, the companies who produce abrasives and such went back to the drawing board to solve the problems, but one company did vastly more.
Rather than merely fix the problem, Norton offered replacements that were also measurably superior in doing their respective jobs. And while the technologies they employ may be recent, the company itself is the most venerable there is, and the largest as well. To get some background on them, I spoke with Paul Krupa, the senior product manager for coated abrasives.
“Norton was founded in 1881 as a pottery company,” Paul told me, “but got into sharpening when they bought Pike Products in the 1890s. We are the oldest abrasives company in North America, and the largest abrasives manufacturer in the world. We sell more than one billion dollars per year in abrasives alone, and are currently part of a larger 54 billion dollar company that also makes insulation, windows, pipe and various architectural products. Saint-Gobain, which is 350 years old, is our parent company, and along with building materials, they also make bottles for wine, beer, perfume and other uses. That’s not all that far from their original reason for existing: they were founded to make mirrors for the Louis XIV palace at Versailles, and those mirrors are still in place today.”
These days, the Norton division makes sandpaper, grinding wheels, sharpening stones, diamond wheels, loose grit, tape and other related products at 66 production sites in 22 countries, employing some 15,000 people in abrasives alone. However, there are two fairly recent Norton products that are particularly interesting to us woodworkers: Norton 3X sandpaper and Micro-Fiber wiping cloths.
“Norton 3X sandpaper started as search for a premium performance product specifically for the individual and small shop woodworker who normally might not have access to leading edge technology,” Paul explained. “Our goal was to bring the best technology to them. We had recently had some breakthroughs in paper backing that allowed us to use stronger bonding systems for the grit without making the paper brittle. Sandpaper fails prematurely when the grain breaks off; the longer you can keep it on, the more use you get out of the grit itself. These improvements allowed us to do that.
“We talked to woodworkers to ask them what they hated about hand sanding. They said it takes too long, the paper doesn’t last, and the paper is likely to crack when you fold or bend it for contours and edges. By looking at superior abrasive grains, better bonding materials and improved backings, we were able to come up with improvements in all three areas. We have a backing that can take a more durable bond and paired that with grain that cuts faster and lasts longer.
“On top of that, we had been working on the additives in non-loading coatings. While we had No-Fil self-lubricating sandpaper since the early 1970s, we found that the traditional stearate used on them was not always compatible with water-based finishes. Stearate is a dry lubricant similar to soap that both makes sanding easier and prevents finish from clogging and sticking to the paper, thus extending its life and eliminating the need for wet sanding. To solve the problem, we developed a stearate that is water-based compatible, so that even if there is a trace of residue left, it won’t cause fish eyes or adhesion problems.
“We called it 3X paper because it offers three times the total performance of traditional sandpaper: it cuts faster, lasts longer and helps produce a more consistent finish. It’s sold in belts, disks, sheets and sponges in grits ranging from 36 to 400. Thus, it is perfect for both raw wood and finish sanding.
“Of course, that meant we also had to turn our attention to the other problem area related to water-based finishing; tack cloths. Some tack cloths can cause fish eyes or blooming in subsequent coats of water-based finish. We wanted to find a technology that would not contaminate the surface and cause adhesion or flow-out problems with the next coat.
“That led to the addition of Micro-Fiber cloth to our product line. The modern replacement for tack cloth, Micro-Fiber is made up of filaments that are split along their length so that the cloth made from them has vastly more surface area than normal cloth or paper. As a result, they pick up more dust than other wipes. Even better, the fibers rubbing against one another create their own static charge, which also contributes to grabbing dust. There are no chemicals or sticky additives and nothing to leave any residue. The fibers themselves are what do the job of picking up and holding dust.
“On top of everything else, it is quite green in that it is very environmentally friendly. You can wash it and reuse it repeatedly with no loss of effectiveness. In fact, the cloth can be washed and reused literally hundreds of times. There are no chemicals, additives, tacky substances or anything that could contaminate either your finish surface, or the water you wash it in.
“Of course, the woodworking field has always been very traditional. As a result, it’s difficult to get woodworkers to try new materials. Hopefully, offering sandpapers and cloths like these, that are a giant step ahead of their predecessors, will help them overcome the fear of trying new products.”