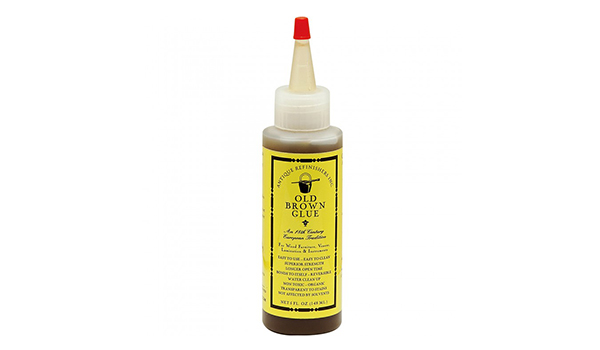
For most woodworkers, the name W. Patrick Edwards evokes images of some of the finest, most complex marquetry on the planet, and so it should. Pat, as he is know to friends, is the expert who owns and runs The American School of French Marquetry, and executes eye-popping inlay to back up his well-deserved reputation. What you may not know is that he, his wife, Kristen Arrivee, and Matthew, one of their three sons, manufacture and sellĀ Old Brown Glue.
What is Old Brown Glue? It’s Pat’s “boutique” version of hide glue, modified to give it better handling properties and a longer, yet variable, open time. It’s used by Brian Boggs, Kelly Mehler, and a host of antique repair people and chair makers who love the controlled open time, which can vary from 20 minutes to an hour merely by changing the temperature in the shop.
As is often the case, the glue was created to fill a need by its developer, who then concluded that others would also appreciate having it. To understand how it came about, we need to get a bit of background both on hide glue, and on the type of work it benefits. In Pat’s case, it’s marquetry and antique restoration.
A native of San Diego, Pat has owned and operated Antique Refinishers, Inc. in the same location for the past 35 years. After studying in Paris at Ecole Boulle under Pierre Ramon, he focused his business on restoring pre-industrial furniture, (18th and 19th century or earlier) and specializing in veneer and marquetry. Four years ago, he and Kristen started the American School of French Marquetry at the same location. It is the only school outside of Paris that teaches the French method of marquetry, which allows you to make multiple copies quickly and accurately using only hand tools. Veneers are cut on a curious device called a “chevalet,” or “marquetry donkey,” that looks like a cobbler’s bench on steroids. The school has been so successful that they are currently expanding the building.
“Originally, I started using a glue pot with hot hide glue. It did everything well. It was strong, transparent to stains, easy to clean up, reversible, economical, and the only adhesive which glues to itself both mechanically and chemically. That makes it ideal for repairing antique furniture, all of which, incidentally, was originally made with hide glue. If a joint breaks, you simply add more glue without having to clean off the old, and you get a perfectly strong joint.”
“One of the trends I see today is the use of non-reversible glues. Furniture that will last will eventually need to be repaired. In fact, sometimes, you need to repair during construction. In my restoration work, reversibility is essential. Hide glue is reversible, even after many decades.”
By manipulating heat and moisture, you can modify how hide glue behaves, affecting viscosity, open time, and cure time. This control is especially important with veneer work, chairs, and other complex assemblies. But hot hide glue requires almost constant attention, and sets too quickly for some veneer operations. “At times, you must overlap the veneer, because it can shrink and pull back from the joint while curing. Hence, you need a glue that takes a longer time to set, allowing the veneer to shrink before the seam is cut. Old Brown Glue does just that.”
It started in 1996 during a European trip, where he joined a marquetry conservation group discussion on modifying hide glue to be liquid at room temperature. Back home, he started work on his own formula.
“While other liquid hide glues exist, I found they gave me uneven results, probably because the glue was not always fresh.” Though dry glue granules have an indefinite shelf life, once it is mixed, it starts to deteriorate. “Other companies use preservatives, but that does not always work. Besides, some of the preservatives are hazardous, and since glue tends to get on your skin, I wanted to use only organic ingredients. I wanted to make glue as simple and safe as possible.”
True to his mission, Old Brown Glue is made in small batches and sold fresh, like upscale coffee or handmade chocolate truffles. The shelf life is about one year after you buy it, but you can extend that time by keeping the glue in the refrigerator. “No one else sells fresh, liquid hide glue cooked in small batches,” says Pat.
It’s easy to see why. Old Brown Glue starts in the kitchen of their building, where Milligan and Higgins’ 192 gram strength hide glue is cooked, along with the other ingredients, in a huge double boiler. It takes four days, during which time the pot must be stirred every hour. They bottle it themselves. “The shop dogs chew on any glue that drips onto the floor. That’s not a problem,” Pat says, “since the glue is nontoxic and almost pure protein.” Each batch yields only 300 ounces.
“Unmodified hide glue gels at around 100 degrees. For Old Brown Glue, I reduced the gel point to about 80 degrees. When the glue first arrives, it appears to be a gelatinous solid, if the room temperature is below eighty degrees. Put the bottle in sunlight, or in warm water for a few minutes, and it is ready to use. It will stay liquid all day long once it is warmed.”
Even more surprising than their manufacturing method is the way they do business. They are about to start taking credit cards, but up until now, they have simply sent out the glue, and asked people to send the money once they received it. It’s an Old World honor system that dovetails nicely with this Old World product.
None of this lends itself to mass production. “Old Brown Glue remains a specialty product for a small group of customers who appreciate the features it has to offer. For 30 years I tended the hot hide glue pot, maintaining the glue,” Pat told me. “Old Brown Glue is a convenient, easy-to-use improvement. It’s made my life much easier, so I wanted to share it with other woodworkers.”