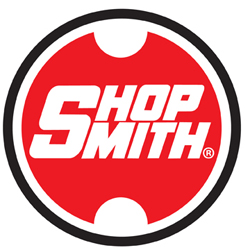
Some people will go to any lengths to get the parts they need. Take Bob Folkerth’s father for example. Back in 1972 Bob’s dad, John, couldn’t find a part for his recently purchased Shopsmith Mark V. John discovered he couldn’t get parts for his Shopsmith and did a little checking around. He discovered that the company was currently “on hold” due to management and financial difficulties. At first he thought he might start a company that could supply parts for the Mark V. In the end, however, he finally decided to rescue the whole company. He bought Shopsmith, moved it to Dayton, Ohio, and has been the CEO ever since. Oh, he also got the part he was looking for.
Bob, currently the vice president of sales and marketing, grew up surrounded by Shopsmiths. He learned woodworking using a Shopsmith and, while in college, began selling Shopsmiths and doing educational seminars around the country. You might say that Shopsmiths are in his blood, but then you might say that about a lot of people.
Shopsmith, the company, is in the enviable position of having a customer base that is almost fanatically devoted to its products. “Part of what makes this a cult is that getting a Shopsmith isn’t the normal path that most woodworkers take,” says Bob. “Most people buy a table saw, then they buy a band saw, then they buy a drill press; our customers jump in all at once. But the success they have with woodworking on our product gives them all a common bond.”
If It Ain’t Broke…
And the company has been intelligent enough not to mess with that success. The first Shopsmith Mark V, Bob explains, wasn’t too different from its predecessor, the 10ER. It was just a tad lighter. Then in 1984, Shopsmith unveiled the 510, but that too wasn’t a great departure from the Mark V. It added an upgraded table system that provided an extra eight feet of support when the user had some long stock to cut. And just recently, in 1999, the 520 was launched. It was just like the Mark V but with more improvements to the table system and a heavier-duty rip fence.
In fact, these models are so similar, the parts are interchangeable. Consequently, if you need to replace a part on the Mark V you bought back in the mid-50s, you can buy a brand-new part for it straight from the factory. The new parts do not, however, work with the 10ER, even though Bob contends that there are still thousands of the oldest generation of Shopsmiths still out there.
A Tool That Spans the Generations
Shopsmith fans are wildly devoted to the product and the company. There’s a whole newsgroup on the Internet devoted to talking about the particulars of Shopsmith ownership and we, at the Woodworker’s Journal, have been following those conversations for a few months. These owners know more about the workings of these tools than most of us regular woodworkers can fathom. “It’s fun,” says Bob, “being associated with a company where so many people absolutely love your product.”
But having a whole slew of raving fans for your product also means you need to listen to what they are saying. Bob says of Shopsmith customers, “they’re not shy about telling us what they think.” And the Internet has made it that much easier to give the company feedback. Consequently Shopsmith has at least two customer service representatives who listen and respond to the questions and concerns that crop up on the newsgroup.
And even though the Shopsmith is supposed to be the only power tool you’ll ever need, some of the owners on the Internet group have more than one of these all-in-one devices. That surprised us until Bob explained that many people inherit their Shopsmith from their father–who may have inherited it from his father–and then buy one of the newer models as they increase their woodworking skills.
So why has Shopsmith succeeded so well here in the U.S., where all-in-one woodworking machines clearly go against the grain? Bob attributes the company’s success to:
-Woodworkers realize that they don’t give up any capabilities with this multi-use tool
-Shopsmith’s customer service goes above and beyond to keep its devotees making sawdust
-Shopsmith’s educational mission with woodworking seminars across the country
-The quality of the Shopsmith itself, a versatile tools that saves space without sacrificing capabilities
-Bob Filipczak