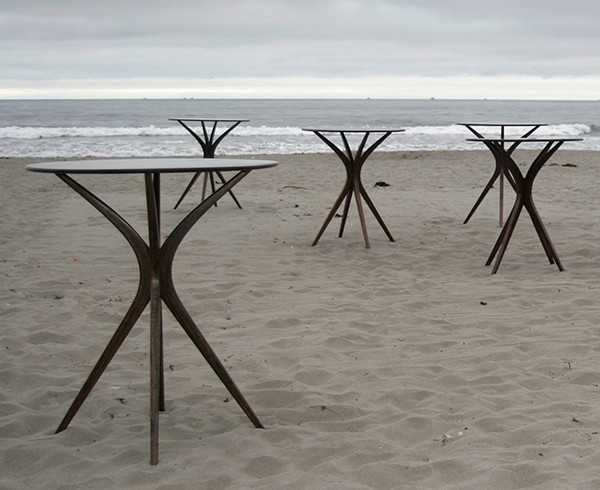
Last Summer I had the pleasure of working on a project in my old shop, Espenet Studios, with my old shopmate, Arthur Espenet Carpenter III in Bolinas, CA. That is right; his name is Art Carpenter. He goes by Tripp. Tripp’s father, also named Art Carpenter, founded the Baulines Craft Guild which is the organization that enabled me to train as a traditional woodworking apprentice. (I’ll talk more about my teacher, Michael Cullen, and my apprenticeship in a later blog.) Stick with me here… We are going to my old shop located along the Bolinas Lagoon which is 7 miles as the crow flies north of the Golden Gate Bridge at the end of June 2014.
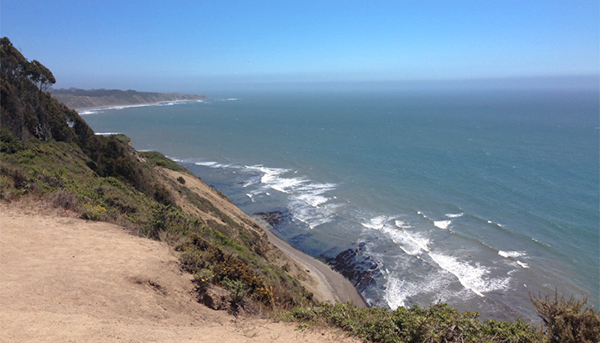
It is more magical than it sounds. The Lagoon is actually a bird sanctuary where hundreds of thousands of birds migrate through every year and seals sunbathe daily. You have to travel over or around a mountain (Mt. Tamalpais) and past a Coastal Redwood forest to get here. There is surfing. There is crab season. This place is located about an hour away from some of the best vineyards in the world. Alice Waters goes out to this town to buy produce because it is the best, and the farm stand is the only 24 hour store around. The Pt. Reyes National Sea Shore butts up to the town’s beach. One thing to consider before going, Wikipedia has deemed this place to be a town full of reclusive residents that take down the road signs. I used to live here. I can relate to the hermit personality traits susceptible in such a dreamy place.
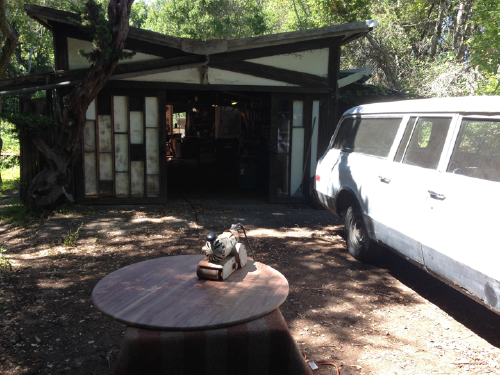
Despite having lived there for years, I could only afford a week out there this time. Luckily, Tripp was working on these amazing Jellyfish Tables, and he accepted my offer to help! The legs are the most intriguing parts of these tables. We steam bent strips of wood, laminated the strips around a form, and then shaped the legs before splining them together for an absolutely astonishing effect.
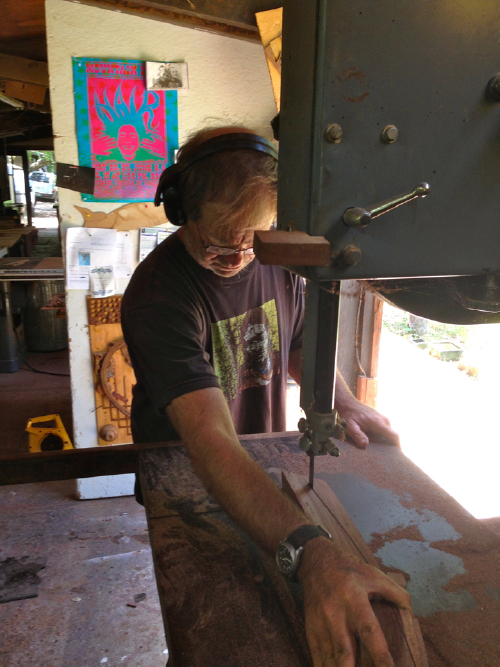
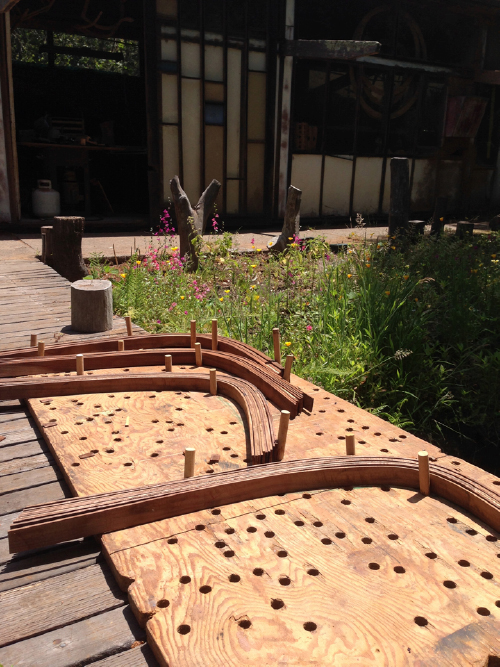
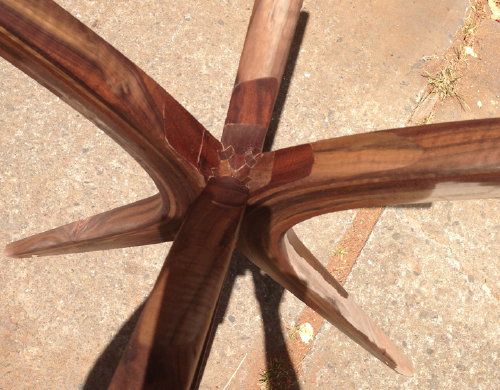
I love the effect the bent, laminated, and shaped legs have. The tops of the tables are almost as mesmerizing due to the exquisite material used. They are all made out of California Walnut, which is my absolute favorite wood! (I suppose now that I live in Indiana, I’ll choose a more local wood to be my favorite… Ash is growing on me!) California Walnut is composed of two trees, Claro Walnut and English Walnut, grafted together. The composition that those two trees make together is rather outrageous. The lumber can end up having an array of color including reddish pink to the classic chocolate brown with creamy whites in the mix.
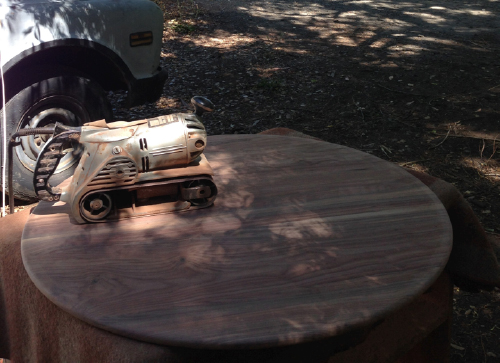
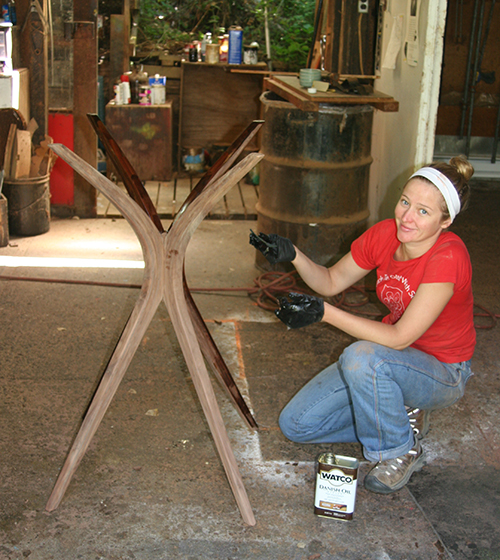
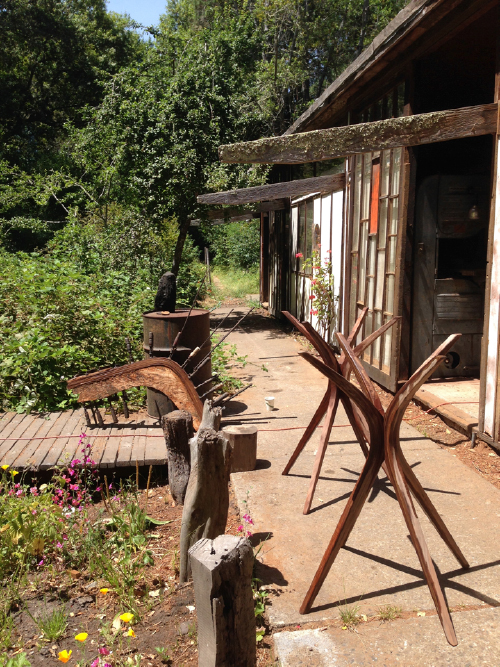
They are absolutely gorgeous tables. I’m super stoked to have been a part of the process of building these gems and to have friends like Tripp that let me pop in and work with them. You can check out some of Tripp’s work here. I can’t wait to incorporate more steam bent curves in my work. Hopefully, you feel inspired to try a new technique too. Happy ‘working’!

Kimberly McNeelan has been a woodworker for about 14 years. She’s been coast to coast and beyond studying different woodworking techniques, learning from various masters, and working on a wide array of projects. Read more of Kimberly’s latest adventures.