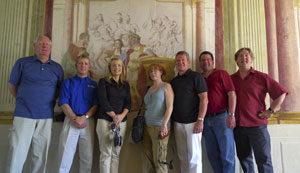
This past April, I was fortunate enough to be part of a factory tour put together by Freud Tools, a leading manufacturer of woodworking carbide saw blades, router bits and shaper cutters. A group of nine woodworking publication editors from the U.S. were taken to northeastern Italy to visit two of the six manufacturing plants that Freud has in Western Europe. One plant is dedicated to the fabrication of saw blades and the other to the manufacture of the carbide teeth, router bit tips and shaper cutter knives/inserts used in all of Freud’s products, as well as a number of Bosch products (Bosch acquired Freud in April of 2009).
One of my first surprises upon arriving in Italy was to learn that the company’s name “Freud” isn’t a family name like “Sigmund Freud.” Instead, the word is a contraction of “Fre” which is short for “fresa” (the Italian word for cutter), and “Ud,” the abbreviation of “Udine” (pronounced “OO-dee-nay”), the place where the Freud company was founded in 1950. The other editors and I had a very pleasant stay in this lovely city of about 100,000 people. Besides a panoramic view of the Alps, Udine boasts loads of impressive Venetian Gothic architecture, like the Torre dell’Orologio clock tower in the city’s central Piazza della Libertà.
The first factory we visited was Freud’s carbide plant in the hamlet of Martignacco, about five miles northeast of central Udine. It was interesting to learn that very few tool companies actually make their own carbide; most buy from a carbide tip and insert manufacturer, such as Sandvik in Sweden. The reason for this is simple: Creating the best carbide for cutting tools is a highly technical and very tricky process which requires state-of-the art metallurgical science and specialized (and expensive!) machinery. Our tour leader, technical plant manager Stefano Driussi, took us through the entire process, starting with the combination of raw metallic powders — carbide, cobalt, tungsten, titanium, etc.). Specific mixtures of these powders are formulated for each of the 16 grades of carbide that Freud makes, including their patented MicroGrain “TiCo” carbide, a combination of titanium and cobalt. Each mixture is designed to give the carbide a particular balance of hardness and toughness (also impact and wear resistance) that suits a particular type of machining application — a saw blade to rip hardwoods or composite materials; a router bit for shaping plastics, etc. The metal powers are carefully measured, then mixed together and combined with alcohol. They are then poured into a large Ball Mill — a sealed spherically-shaped tank filled with stainless steel balls that agitate the mixture 100 kilograms at a time. The ball mill runs for anywhere between 36 and 120 hours and creates a muddy-looking sludge. After the steel balls are removed, the sludge is transferred to a spray plant — an even bigger steel vessel that resembles a huge dust collection cyclone. The spraying action inside the device evaporates liquids and turns the sludge into zillions of perfectly round, homogeneous droplets. These teeny carbide balls are between .8 and 2 microns in size.
Next, a tumbling machine smoothes the surface of each ball-like droplet. Smoothing is necessary because the metallic powder must flow freely when it is next poured into tiny molds — one for each little carbide saw blade tooth (or router bit insert or shaper knife). Special automated machines make these teeth, dispensing exact amounts of carbide powder into short rows of molds, then pressing the powder to compact it to give it enough density for it to keep its shape when the tooth is pushed out of its mold. Each carbide tooth is now in a “greenwork” stage; it’s hard enough to hold in your hand, but still easy to crumble apart with your bare fingers. Many dozens of press-molded tips are deposited onto metal trays, which are stacked into holding frames. The automated presses in Freud’s plant run 24 hours a day, and each one produces between 55 and 93 thousand saw blade teeth per eight hour shift! At this rate of production, the plant churns out around 6-7 million saw blade tips a week!
Next is the most crucial step in the carbide-making process: Sintering permanently transforms the molded greenwork into solid carbide teeth ready for the rigors of woodworking. After the trays are sprayed with a nonstick coating, they go into large (1-1/2 meters in diameter) pressure vessels which are sealed, put under a very high vacuum and heated up to a maximum temperature of around 1,450 degrees centigrade. To get the disparate metals to meld properly, heat is applied slowly during a computer control cycle that ramps up heat in a precise way that’s specific to each carbide formulation and tip size.
Sintering is a necessary and complex process because the various metals that make up carbide teeth don’t easily bond together. If you were to simply heat the powder until all the disparate metals melted, some would evaporate before others had dissolved completely. To put it a different way, sintering carbide is like shaking the salad dressing bottle; the agitation gets the oil, water and vinegar to combine into a well blended mixture.
The finished teeth come out of the sintering vessel very slightly smaller than they were they went in, due to shrinkage. They’re now ready to be sent to the saw blade factory where they’ll be brazed onto blades and ground to final sharpness. By keeping the tooth size shrinkage tolerances very tight, the teeth require very little grinding, thus saving raw materials as well as wear and tear on the grinding equipment.
To help keep their carbide manufacturing on track, Freud’s carbide plant has its own on-site laboratory, which handles both quality control for production, as well as research and development for new products and improvements in the manufacturing process. The lab analyzes all raw materials that come into the factory, to assure that they’re up to Freud’s high standards. They also spot check the carbide products after manufacture (each carbide batch is bar coded so that it’s easily trackable). These checks include hardness testing using a special optical device that measures surface deflection. In another test, technicians use an optical microscope to inspect the carbide’s surface to evaluate grain size and porosity, as well as to make sure the carbide is free of fractures and “lakes” — blobs of binder material that compromise the grain structure and weaken a tooth or cutter and make it more susceptible to chipping and breakage. There’s a magnetic saturation test to evaluate the brittleness of the carbide, and an electron microscope is used to check the carbide’s surface structure as well, to assure that the brazing alloys used to attach the tips to a blade body will stick properly.
One of the coolest things about Freud’s carbide manufacturing plant is that, in addition to producing jillions of saw blade teeth in standard shapes and sizes, they’re also geared up for producing smaller batches of custom-made carbide parts. They do this using either of two methods: One is to press the carbide powder into standard shapes, such as square or round blanks, and then mill the green blanks to near-final shape before sintering them. The other process is to create the greenwork in specially made molds used in Freud’s powder pressing machines (described above). That process begins in a special mold making shop inside the plant. The molds used for making both custom and standard shape teeth and cutters are cut from thick blocks of stainless steel using a powerful electro-discharge machine (EDM). The EDM passes large amounts of electricity through a copper wire electrode or punch that actually erodes away the stainless to create the desired mold shape. It’s a slow process that removes as little as three millimeters of material in 24 hours! The positive and negative halves of each mold must then be hand polished, to achieve a final fit with a tolerance of less than plus or minus 2 microns. Such a tight fit is necessary to prevent carbide powder from leaking out when it’s poured into the mold (thank goodness woodworkers don’t need to work anywhere near this level of accuracy!).