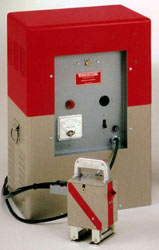
Wouldn’t it be great if someone came up with a handheld gizmo that instantly cured any common woodworking glue so that you didn’t have to clamp and then wait for the glue to set? You know, sort of like a welder for wood, but one that works with white glue, hide glue, TitebondĀ®; in fact, any waterbased glue. Think about it: you could glue up impossible shapes, curves, veneers and even bent laminations without having to create convoluted masking tape and rubber band contraptions. On top of that, you’d save space, money, and time by not buying or shuffling stacks of clamps around the shop.
I know what you are thinking. You’re convinced I’ve been reading too much Harry Potter, but as it turns out, there is just such a tool, and it is available to us Muggles. It’s called, appropriately enough, theĀ Workrite Wood Welder.
Perhaps you are kicking yourself because you missed the debut of this brand-new wonder by not going to the AWFS in Las Vegas this year. You’re not even close. Workrite has been building and selling its two models of wood welder for almost 60 years, and the company itself is way older.
Workrite is a family owned business started in 1908 by Vernon Meyer, the grandfather of the current owner, Bob Meyer. At first, they made radios and automotive parts. The family sold the radio business just before the Depression, but got it back a short time later when the buyer defaulted. During World War II, they also made wooden toys, but these days, they only make the wood welder.
“In the 1940s,” Bob Meyer recounted, “my grandfather would put ads in the local paper to attract inventors who wanted items manufactured.” One such inventor, an engineer named R. A. MacDonald, answered one of the ads. He had designed a wood welder, a technology that grew out of the development of radar. Such welders were used during World War II to quickly build wood planes and boats, but the technology soon jumped to the rest of the manufacturing world. At that time, about five companies made similar units, but today, only Workrite is left, and they have been making their welders since 1947.
At the heart of the gizmo is a radio frequency generator that puts out 27.12 megacycles of radio waves. The radio waves use the water in glue as a conductor, causing the molecules to vibrate quickly and generate heat. In just five seconds, the moisture is driven out, and the glue is set, making further clamping unnecessary.
There is no need for the unit to touch either the glue line or even the wood. Instead, it creates a field that goes right through wood, or any other non-metallic material, to cure the glue. Their Model 3000, the smaller of the two, will go through an inch and a half of wood to dry a glue line. The larger Model 4000 uses the same handheld unit, but will go through two and a half inches of wood. The glue line can be either parallel or at right angles to the handset. Surprisingly, both models work on regular 110 volt outlets with a 20 amp receptacle.
“When I take it to woodworking shows and demonstrate it,” Bob told me, “woodworkers think it is magic. It takes just five seconds for a spot weld. The time saving is enormous. You can use it to spot weld a few places, release the clamps, and let the rest of the glue line dry on its own, or use it to set the entire glue line. It works with any waterbased glue, from hide glue to aliphatic resin, by chasing out the water almost instantly, causing the glue to set. Because it works so fast, it does not heat or dry out the wood, and is completely safe to the humans using it. Our machine has been independently tested for all health issues, such as electromagnetic field duration, and it has passed all federal tests.”
The technology is similar to that which is used in garage door openers, CB radios, microwave ovens, ultrasound imaging and the diathermy treatments used in some doctors’ offices. In this case, the power is focused in a handheld unit that creates a field only about four inches by four inches. An ideal frequency, or oscillation speed, coupled with a high concentration of radio waves on a small glue line, makes it work, and good design makes it last.
“Our machines are so well designed that they will run for 50 years,” Bob said. “The only parts that need replacing are the hand unit and tubes. We keep a complete stock of replacement parts on hand, and virtually any machine, of any age, can still be repaired.”
“Marketing is mostly by word of mouth,” Meyer admitted. “Seeing the machine work is what makes people believe it. The best marketing tool I have is for you to see the machine do its thing. When I hand you two boards in seconds, and you can’t break them apart, it is the ‘wow’ moment.”
A lot of machines in the past went to high school and college wood shops, where glue drying time is a huge problem with the time limits of a class. They are also common in both small and large production and custom woodworking facilities, and some hobby shops as well. Workrite sells the machines direct, on their web site, and through over 400 tool and machinery dealers around the world.
If there is one drawback, and it certainly is the only one I can see, it is the price. Technology combined with quality does not come cheap. Their Model 3000 goes for $3,600, and the larger Model 4000 is $4,200. To be fair, though, I guess one could save an incalculable amount of time and space with such a tool, and if it really kept working for 50 years, that comes out to less than $1.50 per week. Maybe it is cheaper than it seems.
“Instead of having a third of your shop full of clamped projects,” Meyer pointed out, “you could continue working on the piece you just glued. Even beyond the savings in floor space and time, think about how much money most shops have tied up in clamps. With this machine, you don’t need them.”
Excuse me. I’m going to see if one can sell used clamps on eBay.