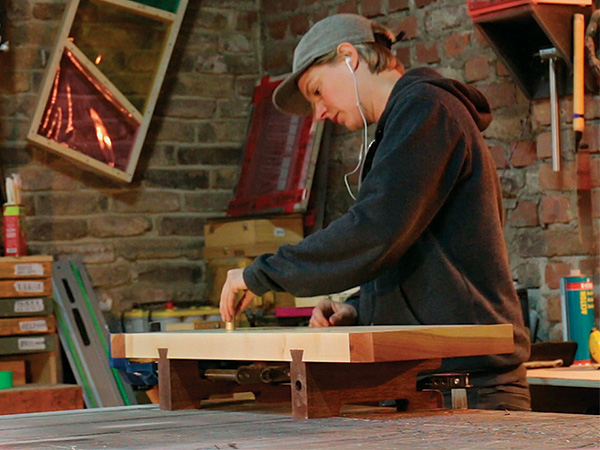
The idea to build a Mini Tabletop Workbench came to me for several reasons. First, while I do have a big workbench that is very strong, I also use it for cutting sheets to size and to paint and oil things. Naturally, the top is covered with dried paint, and when I work with more expensive woods, these paint stains rub off on the nice wood, which makes my finishing process a lot more difficult. The top of my This strong and versatile Mini Tabletop Workbench provides a great mobile work surface that is sure to enhance your workshop experience. larger workbench is also not very even, because it serves as a sacrificial surface for my tracksaw.
Another good reason to make a Mini Workbench for yourself might be the size of your shop. This little bench has all the key features of a big bench but is easy to move out of the way — or even to take with you on a job or just to work outside.
For my Mini Workbench, I chose to use maple, plum and mahogany lumber, mainly for aesthetic reasons. If you want a bench that is cheaper to build and can take a bit more stress, beech would be a good choice.
The dimensions of my bench are 35-1/8″ long by 12″ wide with a height of 7-1/8″.
Getting Started
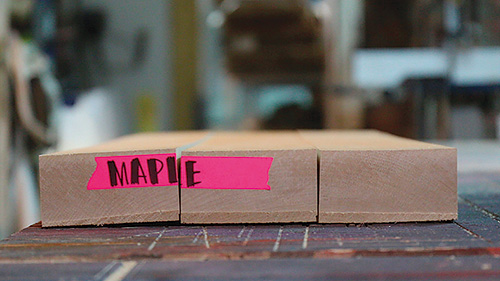
I started by cutting the different woods into roughly the dimensions I needed (see Material List) and milled it all down to the same thickness of 2″.
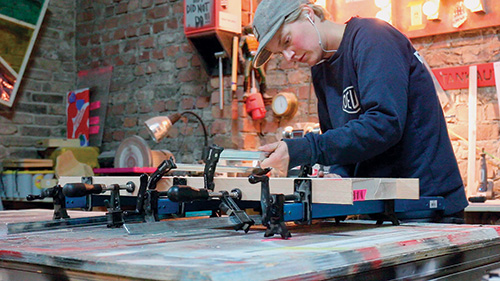
For the top of the bench, I cut a maple slab into three strips of 4″ x 29-1/8″ and glued it back together with the middle strip flipped upside-down to minimize cupping as much as possible. For extra strength, you can also join the three pieces with biscuits or dowels, but it is not necessary with this construction.
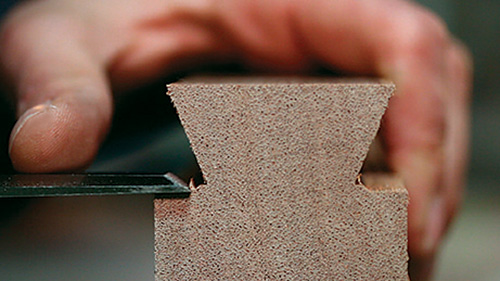
While the glue dried, I started working on the legs, which I made from mahogany. I cut the wood for my bench’s legs into two pieces measuring 2″ x 6″ x 12″, but in hindsight I would be a bit more generous with the height, because when the vise is built in later, it wouldn’t hurt to have a bit more clearance.
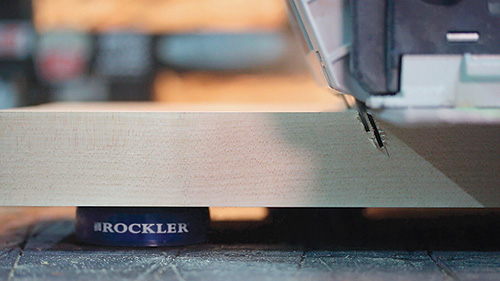
I connected the legs to the benchtop using a long dovetail joint. The dovetail on the legs was cut on the table saw at a 22.5˚ degree angle.
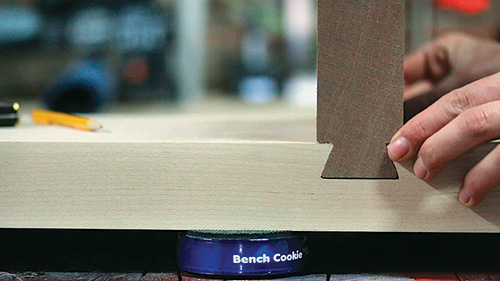
After the tabletop glue-up dried, I took my tracksaw and cut the same 22.5˚ angle into the underside of the top to make room for the dovetail to slide in. I took my time doing this and sneaked up on this cut because it is very easy to cut it too wide. It is a good idea to experiment with test pieces until it fits perfectly. A chisel and a router plane work great to clean up traces of saw blade marks and to refine the inside corners of the tails on the legs.
Breadboards
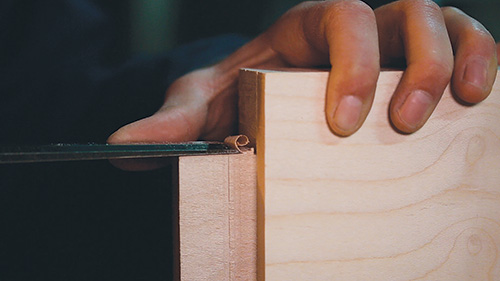
Your next step is to machine the breadboard ends. I cut tenons on the ends of the benchtop, first. There are a lot of ways to cut nice tenons. I used a hand plane, but the tracksaw will do a great job as well. Before I made the first cut, I checked what Forstner bits I had available and sized the tenon thicknesses based on that bit. In this case, I used a 1″-diameter Forstner bit.
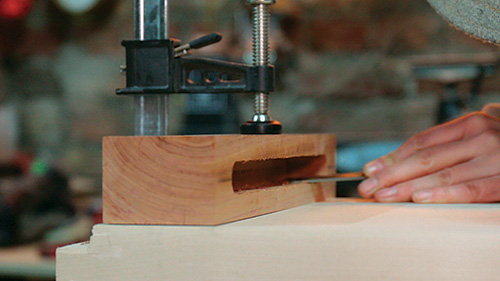
Since I would be cutting the mortises with the Forstner bit, I rounded over the edges of the tenons with some sandpaper to provide a snug fit.
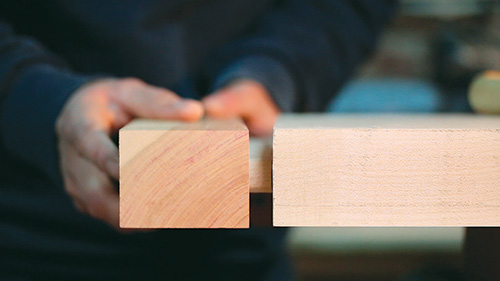
The plum wood I chose to use for the breadboard ends was already milled to the right thickness, so I only had to cut them to size and drill out the rough mortises with the Forstner in my drill press. To make things easier, I set up some stop blocks that assured that both breadboards were identical. Set up a depth stop, as I did, to drill these repetitive holes.
Again, a nice sharp chisel was all it took to clean up both mortises.
Legs and Vise
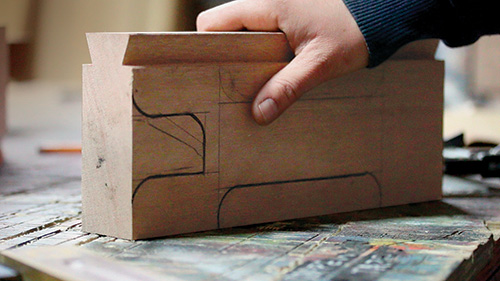
I didn’t secure the breadboards and legs right away because, now that all the joints are done, it is time to shape the legs and fit the vise.
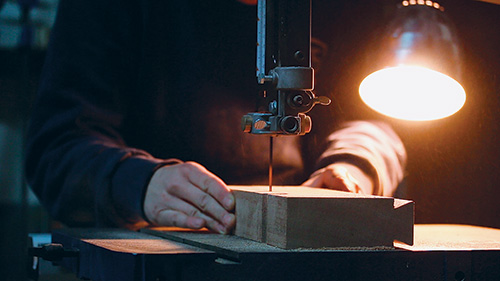
I chose the leg shape you see in the Drawings because it looks great and also provides a good surface to clamp the workbench to a tabletop, later. It is a quick job to cut the legs to shape on the band saw. I used sandpaper backed by a round piece of steel to clean and smooth them, but a spindle sander would be a great help here.
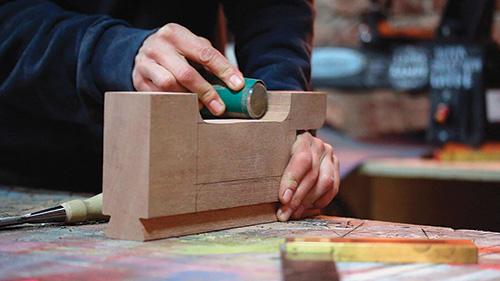
After one leg is done, the other leg needs further work because it will have to make room to fit the vise. I chose a 9″ quick-release vise with a built-in bench dog. I took measurements from the vise and cut out the corresponding recess from the right-hand side table leg to accommodate the hardware.
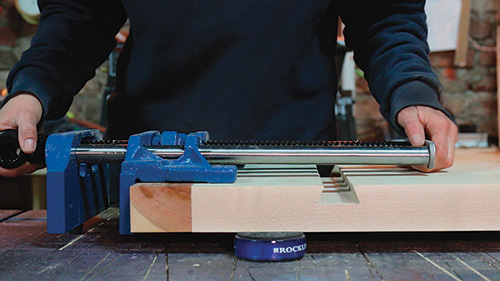
Once the vise had enough room to fit, I continued by working on the right breadboard. It is very helpful (and also looks nicer) to have the vise flush with the breadboard.
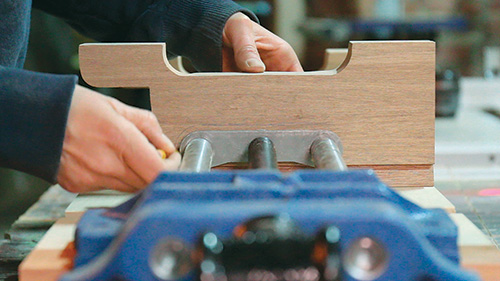
Again, I transcribed the measurements to the breadboard and used my table saw to cut a recess into the plum wood to fit the vise.
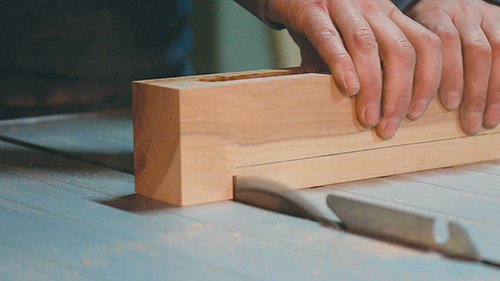
My vise attached with four screws driven up from the bottom and two more driven into the face, which was quick and easy to do.
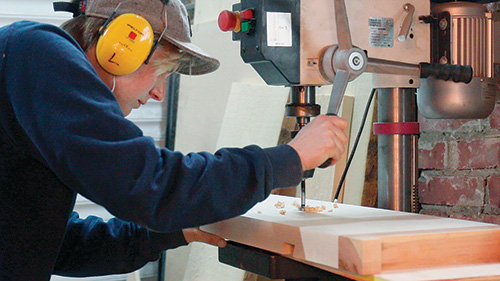
The last step before putting it all together was to cut the holes in the benchtop for my bench dog. It is much easier to drill these holes on a drill press before the legs and the vise are attached. I bored a line of 3/4″-diameter holes down the middle of the benchtop, spaced every 4″.
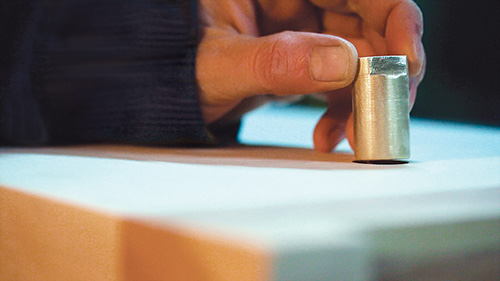
I had a piece of 3/4″ solid brass to use as a bench dog, into which I filed a little notch for securing flat-edged workpieces. Then I drilled one hole into the left leg for storing the bench dog when I’m not using it.
Assembly
Now you’re ready for final assembly. Although this is technically not the correct way to do it, I secured the dovetailed legs with two 3/8″ wooden dowels. My opinion is that, for a tabletop this narrow, there probably won’t be enough wood movement to affect the leg dowels. I also secured the breadboards to the benchtop with three dowels each.
The Mini Tabletop Workbench is a great addition to my shop, and I am sure I will get a lot of use out of it. I bet yours will get a workout, too.