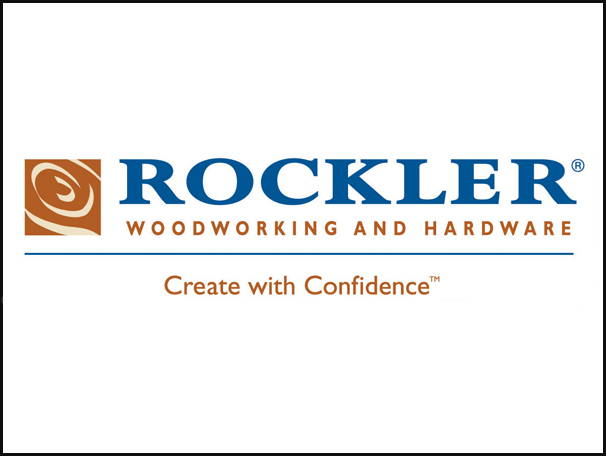
It’s official. Rockler has named five special woodworkers as the best in their categories. Fighting their way up through tough Rockler Woodworking and Hardware Store competitions, they’ve emerged as the best of the best. To find more about them and their craft, we recently caught up with a couple of the winners, Bob Mathews in Portland, Oregon and Jim Burrows of Cincinnati, Ohio.
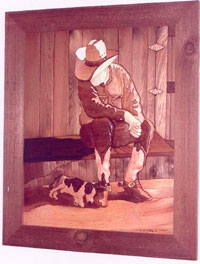
Like a lot of people, Bob Mathews got started in woodworking because his dad worked with wood. And as an adult, he made furniture as a hobby. But after about 10 years, his interest in furniture making was beginning to wane.
“Then, about three or four years ago” Bob recalled, “my wife asked me to make one of those intarsia pieces. People saw it and liked it, so I made another.”
His first and still strongest influences were the works of Judy Gale Roberts. He diligently went through her books and videos. When he started, he shared many woodworkers’ common disdain for scroll saws. But after struggling with a band saw, he discovered that the scroll saw was perfect for his work. He now owns a DeWalt and an RBI Hawk.
In practice, his early work followed small patterns … until one day while watching one of Judy’s videos, her saw her standing in front of a huge piece she’d created. It dawned on him that this hobby could be more than what Bob called “just cute little pictures.” And along with working at a larger scale, Bob began to make his own patterns by combining his love of photography, his drawing ability, and woodworking.
In fact, it was a photograph taken by his brother-in-law that inspired his award-winning portrait of a cowboy.
“He [the BIL] used to break horse and raise and judge show dogs,” Bob recalled, “So when I got the picture from him, the idea of cowboy and dog seemed obvious. The original was a little rough, so I added the fence, changed a concrete bench to a porch seat, and of course added the dog.”
Since Bob doesn’t use stain, he’s always on the look out for the right color and shade of wood. The perfect piece often turns out to be that incredibly ugly one that no one wants. But it may have just the right character & like the dirty, dusty look he needed for his Cowboy’s hat and pants.
Bob had made over 50 intarsia pieces since he started. His current goal is to finish 25 new ones each year. Though he’s not giving up his day job, keeping the equipment running at Daimler Chrysler Parts Distribution Center, he has signed up with a gallery in Portland. They’ve also asked Bob to try his hand at band saw (also called “freeform”) boxes … incorporating intarsia into the design.
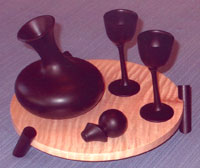
Jim Burrows is 71 years old, but he’s not retired. He still plants 800 acres of soybeans and corn on the family’s Ohio farmstead every year. He’d also worked with wood his entire life, even building homes back in the fifties. Then, eight or nine years ago, while building some furniture for his church, Jim ended up making a couple of table legs. It rekindled an earlier interest in turning. Not one to hold back, he decided to study under woodturning masters such as David Ellsworth and John Jordan (whose work is on display in the White House).
As Jim described it, “It’s a hobby that got out of hand.”
He got so interested; he started teaching around Ohio and became a member of the Ohio Valley Woodturners Guild in Cincinnati and the Western Ohio Woodturners in Columbus. In fact, the 2 AM piece that made him a national winter started as a contest in offset turning at the Cincinnati club. To create the distinctive look, part of the piece is turned, and then it’s moved to a different center point to turn another part.
“The parts you’re not working on become a blur.” Jim noted. “It’s not a big mystery on how to do, but it’s difficult and requires a lot of hand work. The two goblets were especially hard since they had to be identical. You can’t finish one whole piece, and then do another. You make one cut on a piece and take it off and make the same cut on the second, then go back and forth until you’re done. It’s not for everyone.” Jim uses a General 260 lathe at his shop, where he also has a gallery.