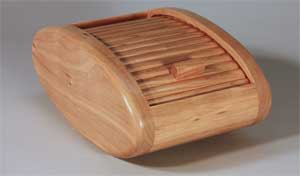
Bruce Erdman was once a professional woodworker — and now he is again. Back in the 1970s, throughout college, his interest “festered.” Around 1972, his future wife — as Bruce put it, “In 1972, we found out we were going to get married: I knew it, she didn’t, but she eventually found out” — asked if he could make some of the furniture for their home.
He did, and also read about woodworking, looked at it and, “the day after I graduated, it was an instant decision: the heck with teaching.”
Instead, he opened what he described as a “normal” woodworking business in Mount Horeb, Wisconsin. Within a couple of years, he’d found a signature product: the oval tambour box. It came about as a way of doing something that “not everybody else was doing,” and was a combination of the traditional rolltop desk and Shaker oval boxes. The appeal of the design, Bruce said, has “stuck” since 1978.
What didn’t stick was the appeal of running a business: as interest rates went up in the early 1980s and relationships with galleries changed, Bruce’s business shifted to a focus on computer furniture, “which was all the rage in ’84. Solid oak computer furniture: it’s the craziest thing, now that I look back on it.”
Then, “the next step for me was to do a ‘real business.'” After months of Small Business Administration courses, loans for CNC [computer numerically controlled] machines and more, that “taught me how to be a real businessman,” though, Bruce said “I was turned off to that.”
He sold his woodworking business and all of his equipment and went to work as a computer programmer.
That lasted for a few years and then, a couple of years ago, he found himself needing to choose another occupation again. He decided to give woodworking another go.
“When people ask me why I do it, back in the day, the answer was easy: ‘It’s a job; it helps pay for what we need.’ Now, it’s different. It doesn’t affect whether we stay in the house. What excites me about it is the woodworking. I don’t know why, but I have to be torn away from the shop in order to do anything else.”
This time around, since he’d sold off all his machinery, Bruce started out with a couple of projects made entirely with hand tools: a rocking chair and a Bible box.
Then he found out about the possibility of acquiring old woodworking machinery, including the Delta 6 x 48 belt sanders from the 1950s and 60s he says are critical to the production of his oval tambour boxes. With the discovery of the possibility of acquiring these old machines and the website Old Woodworking Machinery [now Vintage Machinery], Bruce says he found himself heading down a slippery slope.
“I’ve bought 100 machines in the last three or four years, and kept maybe 10 of them. The rest I’ve sold as restored or parted them out. I enjoy it as much as woodworking now. It’s a real kick to take a rusty piece of nothing and turn it into a beautiful, stunning piece of something.”
Usually, in the summer, Bruce says he kicks everyone else out of the garage in order to work on paint removal and other restoration processes for these old tools — but this summer, he has so many woodworking orders, he doesn’t know if he’ll have time to do that.
One project he’ll be working on is his new series of chess tables. The 3″ squares have clear, open air around them — “you could drop a quarter, and it would fall between them,” Bruce said — while the actual pieces are blocks of wood of different heights with features cut into them. They are not turned.
“Chess is oriented somewhat toward medieval times and castles, and castles have moats,” Bruce said to explain the open air surrounding the squares.
It’s one of the ideas that have just popped into Bruce’s head, the source of inspiration for most of his woodworking projects. “I’ve got 20 or 30 [ideas] up there right now that I can’t wait to get started on.”
Another one he cites as something with ongoing popularity is his Pigeonhole Cabinet. “I was working in the shop on a pigeonhole desk, and it didn’t come out right, so I threw it in the burn pile,” Bruce said. “My wife took it out, and it occurred to me: people want pigeonholes. They don’t care if they’re in a desk.”
Although Bruce worked mostly with imported woods in the 1970s, “this time around, I work only with domestic woods” – mostly walnut, bird’s-eye maple and cherry. “Domestic woods grow right here and are pretty,” he said, plus, “I no longer feel the need to work with anything that I don’t know where it comes from.”
And, although he says he would love to use more reclaimed lumber, it’s just too darn expensive. “It’s hard to get used to the way prices are going these days. The glue I bought two years ago for $12 a gallon is now close to $20 a gallon.”
So, for his wood, Bruce relies on sources like Craigslist and people who run mills in southern Wisconsin. “I pick up whatever old wood I can get: if Grandpa had a tree he cut down and put it in the garage, and he died, and the son died, and the grandson’s wondering what he can do with this: I know what he can do with it.”