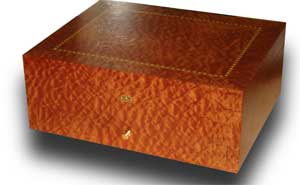
Although Don Green’s father was a builder and he was “kind of exposed” to woodworking all along, when he went to college, he graduated with a degree in sculpture. “I realized quickly that was going to be a hard road,” Don said. Luckily for him, shortly after graduation, he was asked to be the shop superintendent in the wood department at his alma mater — “be the shop super guy, deal with the equipment, the kids and stuff.” In another lucky break, “There were two real sharp guys in the shop at the time, so I learned real woodworking,” Don said.
Don has never had any other career, and “I make all kinds of different things,” he said. When he started out, “At first, I started to feel like I was always reinventing the wheel.”
Now, after 20 years of woodworking, he says making things generally goes efficiently and effectively. “My shop is full of fixtures and jigs,” Don said. “Over the years, I’ll sort of get into one thing, figure out how to make it efficiently, and bring in the equipment I need. Over the years, as the market gets saturated, and I get tired of it, I sell off the equipment.”
For example, Don said, he used to have a couple of lathes set up for automatic feed: one to do spindle turnings, one to do faceplate turnings. “When I wasn’t doing those anymore, those machines went.”
A few years back, when he began making small boxes, “I married two pieces of equipment to create a small-lot press, to press panels for three minutes.”
Don’s current work requires solid bandings and veneer faces, which means Don has a machine he refers to as “an oddball bander: it uses a resin glue joint as opposed to a hot-melt joint, and gives you a furniture grade banding instead of cabinet grade.” Not too many of these banders are around, as Don suspects the technology was developed before the widespread use of hot-melt glue. “For real big shops, [a resin glue bander] isn’t effective. For small shops, it’s overkill.”
He combines his bander and his small-lot press with a third tool, a two-edged trimmer that flush trims both edges of a banding simultaneously in an automatic feed process, for his work. “With those three pieces of equipment, I could make money,” he said. “Without the equipment, I wouldn’t have made a dime.”
Recently, Don has developed designs for some new chairs, chests, tables and a coatrack. “The biggest treat is developing new work,” he said. “That’s what’s still sort of fun about it” — and all of those designs, he said, have potential for growth as he revisits them. When he’s making his designs, whether on computer or on paper, Don takes notes about possibilities that he might return to later.
Don’s preferred wood to work with is mahogany but, as it is no longer a viable option for him, he’s now working mostly with sapele. “A big, heavy grain pattern gets in the way of the stuff I do,” Don said. “Sapele is a nondescript wood. It takes finish well, and it’s stable, and it’s available.”
Whatever he’s building, “figuring out how to make a high quality product without laboring over every little thing — that’s where the challenge is,” he said. “You get that all right, then you make a piece. Then when you make 20 of them, you don’t want to make another one.”