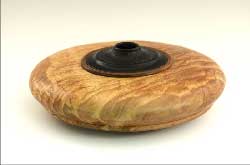
For over 20 years, Don Suiter worked in construction, building homes. Toward the beginning of that career, a friend of his had started building some furniture and, because they worked together on some projects, Don bought a small lathe for “spiral work for furniture, things like that.”
After a couple of decades had gone by, Don was tiring of the physical exertion of construction work. When he and his wife took a 25th anniversary trip to Deer Island, Maine, and saw the work of the local artists’ there, Don said, “I saw what people were doing with lathes, and I came back and bought a 14″ bed lathe.”
Excited about the possibilities of what he could do on a lathe, Don, back in Minnesota, quickly outgrew his 14″ lathe purchase. When he realized he was excited about hollow forms, he bought a bowl lathe, and now, he says, he’s “upgraded beyond that.”
Those first two or three years after the fateful 2005 trip the reintroduced him to woodturning, Don was still working construction, and his turning efforts were “hit or miss. I would go months without getting behind a lathe.
“When I first started, I did everything by hand, and with an Ellsworth gouge.” Now in the process of downsizing his ship — eliminating the furniture and cabinetmaking components to focus on woodturning — Don is currently using a Jamieson hollowing jig. “It makes it a lot easier to have constant wall thickness,” he said, “but I’m glad I started out the other way, doing it by hand. It gives me a better idea of what’s going on in there. It’s like going from hand tools to power tools. There’s a difference, but I think starting out that way makes you better.”
Part of the appeal of woodturning for Don is the creative process, including the study of various forms. It’s a challenge, he says, to figure out “what’s the difference between a form or design that’s immediately pleasing to the eye and one that’s just mediocre.” As a part of this, he does “a lot of looking at what other people are doing. The Internet is great for that.” In fact, Don belongs to the online group World of Woodturning, where people from across the world offer critiques on woodturning designs.
For Don himself, many of his designs these days are combinations of lathe work with carving and piercing. “I don’t do a lot of the same thing; I love exploring,” he said.
His love for exploration extends to the varieties of woods he uses, as well. “My shop looks like a natural history museum,” Don said. “I’m always looking for unique woods, unique colors, unique grain patterns. It goes along with my attitude toward the styles I turn: I like unique.”
He does, however, admit to at least one preference in his wood choices: a love for burls, particularly those from Australia and New Zealand. The trees there, he said, “are prolific burl makers, and most of them are absolutely gorgeous, both the grain and the color.”
Don also enjoys figuring out the possibilities of what he can do on a lathe. In addition to studying wood art forms, he also enjoys learning about pottery, particularly Middle Eastern, Chinese and Japanese forms, as well as glass blowing. And, in the past couple of years, he’s also begun carving stone.
That came about at the urging of a friend, who had been after him to try working with stone. “I resisted for a while,” Don said. “I have kind of an obsessive-compulsive personality, in that, when I try something, I have a tendency to go crazy with it. I love wood so much that I didn’t want to try stone and take time away from it.”
Now, after working with alabaster, soapstone, and quartite — a material that is between the two others in hardness — Don is looking into the technology of microblasting to carve stone. He’s hoping it will allow him to do more detail work than he has yet been able to. “I kind of like looking for things that not everybody is doing,” he said. “There’s a lot of people out there who do wood piercing, but I’m not aware of any doing stone piercing, and the same with sandblasting.”
One of his favorite pieces, he mentions, is a 6″ diameter turned sphere of Italian ice alabaster. Don pierced the hollowed 1/8″ side walls with a Dremel® oscillating tool, as “an experiment to see how much stone I could take away and it would still hold together and not just crumble.”
“I’m experimenting, trying different forms and different techniques,” he said.