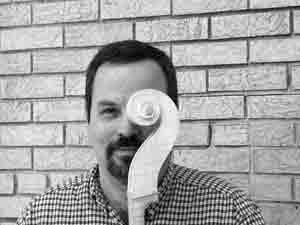
Although Fred Thompson started out studying to be a trombone player, he now knows how to play the violin. Luckily, he says, “you don’t have to play like Itzhak Perlman,” to make violins.
Fred grew up with a dad who had a shop in the basement and, due to his Depression-era upbringing, was “loathe to hire anyone to fix anything around the house.” He started learning some woodworking from his dad, “but it wasn’t really serious.”
Instead, he studied music in college — while earning some extra money doing finish carpentry work for a friend’s dad — and then played trombone with an orchestra in Mexico for a time. While he was there, some of the people in the band were making furniture for themselves, and Fred began to dabble with the idea of woodworking by buying a few hand tools and subscribing to a couple of magazines. He also visited the shops of some violin makers in the area, one of whom had been trained in Italy, and also met a couple of Americans who were teaching themselves to make the stringed instruments.
Around that time, Fred spotted an ad for the Chicago School of Violin Making. He started as a student in the school in 1985 and, he says, it’s a good thing: “If I’d done it on my own, I would have gotten frustrated and given up.”
Originally, the appeal of being a violin maker was that “I thought it was something you could do in a tiny space with not a lot of tools.” That perception didn’t turn out to be quite accurate. “You don’t need a lot of machines, but you do need specialized tools,” Fred said. “And tool buying is a lifelong thing.”
Some of the specialized tools include finger or thumb planes for shaping a violin’s arch; sets of 9 or 10 short, graduated gouges for creating the end of a scroll; long, tapered knives for cutting “F” holes in the top of a violin; and special sets of reamers, with a standard taper of 1 to 30, plus shapers made to the same taper, to fit the tuning pegs.
There are also, Fred said, a variety of specialized tools used to make the purfling inlaid channel along the edge of a violin. “There are makers who use a router, but our goal at the school isto train students to use hand tools,” he said. “The feeling is, if you can’t control a knife, you’re going to have a really hard time controlling a router.”
Having graduated from his own student work at the CVSM in the late 1980s, Fred has now been a full-time teacher there since 2001. In the intervening years, he purchased and ran, along with a partner, a violin making shop. He sold his interest to his partner in 1999.
Fred still occasionally sees some of his old customers, or their instruments, whether for tune-ups or as they play in various ensembles. One of his most recent sales, he noted, was of a viola to an instructor whose student had purchased one of Fred’s violas 20 years before. “It felt good to me that he recommended my viola to his student 20 years ago, and he ended up buying one.”
Fred estimates that, so far, he has made approximately 70 violins, seven or eight violas, four cellos, and a couple of other individual instruments, such as an Appalachian dulcimer apiece for his wife and her sister, and a mandolin. “A couple of years ago, there was a group project at the school to build a string bass,” too, he said. “It’s not in the curriculum because it takes up a lot of space and time, but about 15 students and myself worked on it.”
Fred is currently co-director of the school. “About half of the students who come here are string players interested in learning how to build an instrument, and the rest come in purely through an interest in woodworking,” he said. Violin lessons are required for those who don’t come in knowing how to play.
In addition to building the instruments by hand, the students apply the finish by hand: 20 to 30 coats of a spirit-based varnish they make themselves. The school usually buys its wood from specialized instrumentdealers — and then stores it for several years. “Most makers want their wood to be air dried for 10 years,” Fred said. “We usually buy wood at three to five years old and then let it dry here” — in order to save on costs associated with paying for storage space.
The neck, sides and back of the violins made at the school are maple, and the top spruce, which is “almost universal in violin making,” Fred said. “There are some other woods that some makers will use because they have historical precedent in Italy in the 18th century, which was kind of the pinnacle of violin making,” such as willow or poplar, he said, but it’s generally quartersawn curly maple. Fred has, however, made a couple of violins out of bird’s-eye maple, but noted that it had to be slab cut rather than quartersawn.
Most violins he and the students at the school have made are models, which might be based on a historical instrument, rather than copies, which suggests trying to make an exact reproduction of an historical instrument, Fred said. He did, however, once have the opportunity to take measurements from a violin used by a friend of his in the Pittsburgh Orchestra which had been made in Turin, Italy in 1785. Fred made three copies of that violin. “It was a beautiful instrument, and it was fun to make a copy of it,” he said.
“A lot of musicians are playing instruments that are over 300 years old,” Fred said. “I like the idea of being able to produce something an artist can use, that can last for longer than they do.”