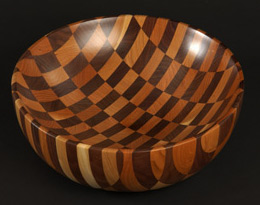
Have you ever seen those cutting boards that are assembled out of blocks of wood to create a herringbone, or some other, pattern? They take a lot of patience, meticulous skill, and an artistic eye. Well, now imagine an entire pool table constructed the same way, and you have an idea of Jamey Rouch’s approach to woodworking.
You might assume that it must be a veneer, but Jamey’s coffee tables, end tables, hall tables, animals, desks, baseball bats, bowls, chargers, and, yes, pool tables, are all constructed by cutting, fitting, and laminating solid blocks of wood. Starting just out of high school four years ago, he’s built a growing business, mostly selling to galleries across the country.
Though he’d been using a band saw since the second grade and had built piggy banks for 4H projects, his unique use of lamination was first manifested in a giraffe he built during freshman year of high school.
“I never won any prizes,” Jamey recalled, “so I started building things bigger and bigger and built a four-foot tall giraffe bank with all these random blocks of wood put together. I thought that would win for sure, but some little oak coffee table won. So the next year I built a table out of these small blocks of wood, and I won!”
And that’s how he got started making furniture. “In my senior year, I thought I might as well give it a try.”
Jamey first works out his plans in his head. After settling on a pattern, he carefully cuts each piece. Exact symmetry becomes especially important with the larger pieces, where any variation or error would be more noticeable than in the smaller work. As he builds his blocks, he uses a wide belt sander to take each piece down to the exact thousandths of an inch.
“Almost 90% of my time on a project is spent gluing all the pieces together.”
He doesn’t sell a lot of pieces to individual buyers, and his web site serves more as an online catalog for galleries. Working with galleries required him to adopt a more production approach. Jamey originally built all of his bowls and plates one at a time. So many different patterns made it difficult to keep control of them all. Seven months ago, he decided to just build eight bowls, three rolling pins, and three bats. This provides a consistent product to the galleries and helps him keep up with their orders – often shipping the items within a week.
“They might want four different plates and three different bowls.” Jamey explained, “But baseball bats are funny & some will say they want a couple of them and some say they’d never be able to sell any. Some galleries give them a try and find that the bats outsell the plates and bowls. It’s unpredictable and seems to depend on the market.
To promote his pieces, Jamey twice a year attends the Rosen Wholesale Craft Show in Philadelphia where he can meet with galleries from all over the United States. He also attends the Philadelphia Furniture & Furnishings Show and the One of A Kind Show and Sale in Chicago.
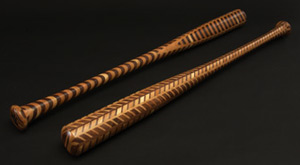
Taking the plunge into business runs in his family. His parents and grandparents run Culver Duck in Three Rivers, Michigan, the third or fourth biggest duck farm in the United States, producing about twenty-five million ducks per year. Jamey works in a freestanding wood shop next to the farm, which is also the source for some of the wood he uses. Much of his walnut, however, comes from neighbors who are tired of dealing with dropping walnuts in their yard and happy for him to come and cut the trees down. Jamey and his family also have their own sawmill.
Business gets better each year, and he now gets help from two part-time employees. They help sanding boards. According to Jamey, every piece is run through a wide belt sander before it is laminated. The sandpaper rips it up a little bit, and little scratch lines make for a stronger joint.
If he can speed up production and get the prices down, he sees adding more people to the production and spending more of his time on the one-of-a-kind furniture like the pool table and office desk. He might also branch out and start doing turning blanks or panels & but wouldn’t use any of his unique patterns.
“I don’t sell many pool tables, but I do sell lots of bats, bowls, plates and rolling pins. The business will probably grow forever, but I don’t think it will come to a point where I can just sit back and just manage things. I want to always be right in there. I enjoy doing projects like the pool table where you just jump into them and figure it out as you go. Bowls and plates are predictable, and I know what to do on those.”
Now back to that pool table. He took apart his grandmother’s pool table to see how it was constructed and get the right dimensions.
“It only took a few days to put the pool table together. The majority of time was spent gluing over 7,000 pieces of wood together. I used 23 gallons of glue. The carving on the four eagles pillars only took four hours & I learned carving just by trial and error. After I built the rail, I went to a local pool table shop and bought the slate from them and had them glue on the rubber bumpers. Since the rail was just little blocks of wood, the bumper caused it to bow in. So I cut the rails apart and reinforced them with aluminum angle irons, and that kept them straight. So I do a lot by trial and error. There are really endless possibilities to what I can build.”