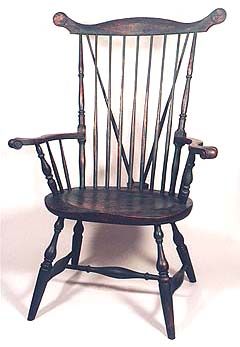
Many people are said to “make” things, but according to my Dad’s old copy of Black’s Law Dictionary the word “make” is legally defined as “to cause to exist, to form.” And that’s a pretty good definition of what Jeff Trapp does.
From his shop in Madison, Wisconsin, he makes Windsor chairs in the time-honored tradition of 18th century New England craftsmen. He’s established a reputation as one of the top makers of Windsor chairs in the country. (Early American Homes magazine officially declared him “One of America’s 200 Best Craftsmen.”)
Though Jeff first discovered Windsors while working as a boat builder out East, he got off to a slow start.
“I bought plans by the author of “Make a Windsor Chair with Michael Dunbar,” but they stayed in a drawer for 12 years?until my wife finally bought me an inexpensive lathe.”
He also got Dunbar’s book and eventually took a class with the master chair maker. But basically, he learned his craft by building his own chairs. His techniques and hand tools are the same used 200 years ago and all he admits to adding is his own “elbow grease and patience.”
But there’s much more to making a Windsor. Jeff periodically heads into northern Wisconsin to pick out good trees to use for chairs. Scouring the properties of family and friends, he selects birches or maples for the legs and braces, and red oak for arms and spindles. (Thick white pine or poplar used for the seat is purchased from a local mill.)
“I look for the least interesting grain because it will be the straightest.” Jeff noted.
That’s important, because he doesn’t saw the timber, but rivens or splits it along the grain. The fibers making up this grain, running from bottom to top of the tree are hollow, like bundles of straw. The process of rivening separates one bundle from another. Some of the riven pieces become the narrow spindles that give Windsors their distinctive, graceful look.
“They may look light and fragile,” explained Trapp, “But because of the way the chairs are made, they’re incredibly durable.” Most mass-produced chairs are just cut out of lumber and lacking this in-grained strength, end up both heavier and weaker.
The green wood he brings back to his shop is easier to work?especially with his hand tools, than kiln-dried wood. Rather than turning spindles on a lathe, he uses drawknives — not just because he’s a traditionalist — because, “It’s easier to just whittle them.”
He might cut out the seat on a bandsaw, but then uses an adze — ax-like tool with a curved blade — to scoop out the seat, a scorp refines the hollow area, and a homemade travisher finish the seat. In a departure from tradition, he admits to making the seat from two joined pieces. It creates a stronger seat, and it was only the relative weakness of the old hide glues that prevented the practice in the past. That same weak glue, however, also originated a traditional “compression” technique Jeff uses to attach legs to his chairs. The h-brace set between the chair legs holds them apart, not together. Sitting on a Windsor increases the tensile strength of the legs?. regardless of the glue.
Acknowledging that the practice is fraught with controversy, Jeff paints his chairs with a milk paint that resembles the old finishes. Traditionally, the chairs were painted?partly out of fashion and partly to protect them during outdoor use. (Their thin spindles were less likely blow over, making them a good outside chair). Painting also makes it easier to use the right wood for the right part of the chair and not worry how the mix of oak, birch, and pine looks when complete.
That’s fine with Jeff, who declared, “The beauty of the chair is in the overall shape, not the different grains.”
So, what’s the best way to learn Windsors?
“Spend a week with me. For the cost of a couple of chairs, we work together and build two chairs each. I have all the tools — although people can bring their favorites – and it gives them a chance to try out tools and decide what they like to work with.”
Jeff makes a variety of Windsor chairs and he also makes other beautiful 18th and early 19th century reproductions. They cost more than mass-produced but when customers learn his chairs will last for generations, they usually decide it’s worth it. In his spare time, Jeff is an avid bicyclist and canoeist (he makes those too) and owns a couple of BMW motorcycles.