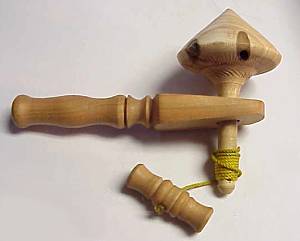
Most of us have our jobs and then we have our workshops. Every once in awhile a woodworker will quit the day job and decide to make a go of it as a professional woodworker. It’s rare, however, when someone has a job that so beautifully accents his woodworking hobby that they blend together and it’s difficult to see where the vocation ends and the avocation begins.
John Cotten is one of those folks. As director for wood products for the state of Kentucky, John gets to play with wood at work and at home. But when he plays with wood, it looks like serious business.
His father was a general contractor and John grew up in his father’s cabinet shop. While he does all kinds of woodworking, his current work is mostly in wood turning. He’s got a Powermatic 3520 lathe that he’s been using for about two years. He has two other lathes but doesn’t have room for them in his new shop (he’s already loaned them out so don’t even think it).
He likes turning because he can turn out pieces quickly. He can come home from work, spend a couple hours in his shop and come out with two finished bowls. Of course, finding interesting wood to turn is a bit easier for him since his job takes him to all corners of Kentucky, talking to lumber mill owners and furtively looking around for interesting scraps.
Plum wood, for example, is one fruitwood he really likes to work with. He has one bowl that he turned to a thickness of only 1/16″. It was great to work with, John says, because he could cut it really thin but it got very hard when it dried. The sapwood also has a beautiful deep purple color that is reminiscent of the fruit.
Just recently he was visiting a Mennonite lumber mill and the owner had just cut down a plum tree. It was about 10″ in diameter and 5′ long with a great crotch piece. He asked the mill owner what he was going to do with it and the he said, “you can have it if you want.”
Not to be outdone by such generosity, John took a long look at the plum crotch. He saw deep vase there, but knew he didn’t have the tools to do it justice. So he sent the piece to his friend, Jack Fifield, a noted turner who has pieces in the Smithsonian and the Guggenheim. “It was one of those instances where you realize the wood had a lot more potential to be made into something than I had the capability to do with my tools,” says John.
But not all wood is so forgiving. The cherry burl he made into a bowl was nothing but trouble. It dried out before he got to it, so it wasn’t in ideal shape. He couldn’t get it to the level of thinness he was aiming for. “I was afraid if I took it down any further it was going to blow out. It was a very difficult piece of wood to work with,” says John.
His background in wood technology helps him when he’s working with some strange pieces. For example, John knows a lot about the spalting process. The spalt is essentially a form a rot, he explains, and so almost all wood will spalt (except walnut). The trick is getting it at the point where the patterns are through the wood but it’s not so soft that it won’t hold up under turning. Some woodworkers, he says, will even accelerate the spalting process by sealing up the wood in plastic and keeping it in a warm place. The plastic also keeps the moisture locked in and that keeps the wood from falling apart. John explains that it’s only during the drying process that spalted wood disintegrates.
On the other hand, sometimes spalted wood is just beyond hope. “I’ve learned over the years sometimes it’s better to just chuck the thing in the firewood pile and go on,” says John.
His future challenge is to get a shop large enough for all of his tools. He recently moved and had to set up his shop in a 24’x24′ garage. If that sounds big enough, you haven’t seen his tools. Besides the Powermatic lathe, he has a 5 HP table saw, a 20″ planer, a 20″ Delta band saw, a 60″ horizontal/vertical sander and a 20″ jointer (that last tool he doesn’t have room for).
So John gets to work with wood all day only to come home and really work it. “It’s my career and my hobby both. I’m one of those lucky individuals,” says John.
– Bob Filipczak