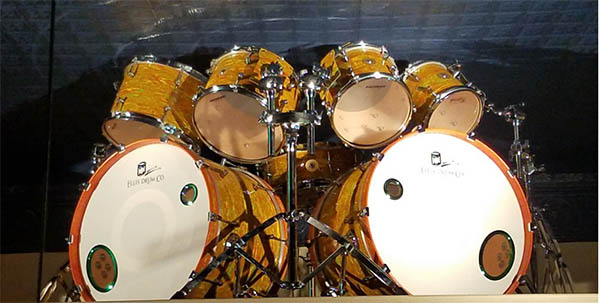
Tim Ellis, of the Minnesota-based Ellis Drum Company, has been making the drums in his self-named line for 35 years now.
Originally the owner of a drum shop selling a variety of lines, Tim got started making his own drums after providing advice and assistance to some customers who were making their own drum as a side project and showed him their prototype. By the end of his time as a shop owner, the Ellis Drum Company drums were the only high-end line people were buying.
These days, the Ellis Drum Company is a two-person operation: “myself and another gentleman, we do it all.”
That starts with getting a shell made to the specs he’s requested. “I get a long cylinder, and typically they’re about four feet tall by whatever diameter of drum that I’ve ordered. It takes really large molds to steam bend and put these shells together.”
After receiving the shell, Tim cuts it down to a specific size on the table saw. Then he may rub the shell down with a fine steel wool in preparation for a lacquer or hand-rubbed satin oil finish. He also cuts the bearing edges – the top and bottom edges that the drum head rides on – on the router table, using a dual 45 degree cut, with the sharp edge then hand-sanded.
When the shells come, “They’re just flat on top and bottom,” Tim said. “And the drum head wouldn’t sound very good if you just had it riding on a flat edge like that.” Although other companies do a 45-degree cut with a counter, making a more rounded edge, “it gives a boomier tone. It’s not as versatile,” Tim said. “With a dual 45 edge, and less wood up against the drum head, it increases your tuning range of the drum immensely. Which means jazz guys, which prefer to tune their drums a little higher, this edge can handle that tuning. Or low pitch, or middle, or whatever you decide to tune the drums, less wood up against the drum head allows a much wider tuning range.”
If building a snare drum, Tim will rout a snare bud on the bottom of the drum shell to accommodate the snare wires to ride on the bottom head more evenly. And, after completing the hand detail work on the shell, it’s time to drill the holes for the lugs (the metal pieces that hold the drum head onto the shell and allow tuning) and hardware, and then assemble the lugs. In addition to drum building and finishing, Ellis Drum Company manufactures all the metal parts for the drums.
As for the wood portions of the drum, unless there is a specific customer request for another type of wood, Tim said he prefers to exclusively use maple. While he’s seen drums made of birch, mahogany, walnut or exotics like bubinga or zebrawood, “All these woods are very exotic, very pretty, but they just don’t have a sound to them,” Tim said. “I would argue that we’re not hearing much of a shell as much as you are the thickness, the bearing edge and the types of heads used.
“We choose on Ellis Drum Company drums to use a very thin shell, very much like a violin body or an acoustic guitar body. Those are made very thin and meant to resonate, and that’s what our drums do.” Maple, he said, “is a pretty wood, it’s a hard wood for what we’re using the shells for, and it works real well. It’s kind of the standard of what they’ve used since Day One of good drums, and we’ve stuck with that formula.”
There are a few variations, depending on the types of drum: the snare drums are eight-ply (“just gives you a little more beef and sound out of that snare drum”), whereas the toms have six plies of 6 millimeter cross-laminated maple “because we want resonance out of our shells.”
The finish choices aren’t related to the sound as much as they are to the customer’s personal preference and use of the drums. “If it’s a real hard-core working drummer, they may not want a varnish finish or a finish that looks like a piece of furniture, because that’s literally what you’re hauling around now. They take their abuse, knocks, bumps, that type of thing, and it shows on lacquered finish drum sets.”
Vinyl wrap finishes, on the other hand, can hold up for decades. Those, Time said, might include the “sparkles and cool finishes you might have seen out there. Some of the color schemes people come up with, I couldn’t wear them, but they love that stuff, and we’ll build whatever they want.”
A few memorable sets have been one finished with a road map atlas – “It was literally a real map, so it was striking. You couldn’t really tell what it was from a distance, but the closer you got, the more you understood, and it was really neat” – and a drum set that looked like each drum was wrapped in a can of SPAM luncheon meat.
Tim also remembers one customer who wanted a great-looking drum set for his den. “Well, the wife had done the entire den in teak. Everything: the furniture, the end tables, everything was teak. So, the drums had to be teak. So we found some really good teak veneer, still stuck with our maple shell, wrapped these drums in teak and, by golly, you can’t even see these drums when they’re in the room because they match so well.”
Before delivering a drum to a customer, Tim tunes it as “kind of a final quality control thing.” While customers may adjust to their own tuning preferences, it would essentially be possible, Tim said, “ to take them out of the shop and set them up and play them at a gig.”
He himself has been a professional musician for about 50 years, currently playing and touring in Chicago tribute band Transit Authority.
When not playing, he’s making between 20 and 50 kits a year, with each kit, or drum set, generally ranging between four and seven drums apiece. He also makes a specialty drumstick, “louder than a brush but quieter than a typical drumstick” out of birch dowels.
And as he completes the drum sets, Tim said, “Because I’m doing everything, I don’t have to check out anyone else’s work. I know it’s correct, I know it’s right.”