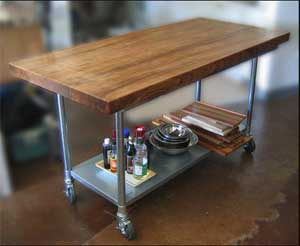
“People keep telling me I’m a Renaissance man — I work with lots of mediums,” says Will Tait.
He has, indeed, trained as a classical artist who learned figure drawing by copying the works of such Renaissance artists as Michelangelo, but Will has also branched out into painting, lithography, glass casting, boat building – and relief carving with a CNC router.
To start with, as a young boy, Will had an uncle who would take him to visit a San Diego art museum on weekends. That uncle was trained as a violin maker, and “he got me started thinking about wood when I was pretty small,” Will said. He also started thinking about art in general, which eventually led to art school — but not before a high school job at a boatyard that built wooden sailboats. “It was one of those old-fashioned, dirt floor, everything done by hand — one of those kind of places.”
As an art student, Will found his way to the Art Students League of New York, where he discovered both a mentor who worked as a curator at the Metropolitan Art Museum — and issued him an ongoing pass to go “behind the scenes” and see the 99 percent of the collection that is not on view at one time — and lessons in how to create drawings that created what appeared to be three-dimensional reality on a two-dimensional surface. That fascination with dimensional appearances has been a recurring theme in Will’s artistic life – and would again play an important role when he turned to working with CNC.
Earlier in his career, he held a job as a ranch caretaker at Big Sur, California, which gave him the time and the space to create sculptures out of large logs. After that, lithography “took over my life for a number of years” – years in which Will and a friend developed a new method of lithography that reduced the registration (the amount by which printed areas overlap to create a clearly defined image) down to “a couple thousandths of an inch, with as many colors as you wanted.”
From lithography, Will went into painting, with, all the while, an idea in the back of his mind for a large project, some day, that would incorporate many of his mediums.
At the Art Students League, Will had learned of the Peacock Room, in which all of the paintings, furniture and other elements were tied together by one theme. The Peacock Room, designed by artist James McNeill Whistler, now belongs to the Freer Gallery of the Smithsonian Institution and has served as an Art Nouveau inspiration to other artists.
With his dream to someday create his own thematic room, Will decided he needed to learn “normal furniture making — not a boat.” He explained, “In boat building, practically everything is curved. The one straight line is the keel.”
During his years of furniture making practice, he was also simultaneously doing relief carvings of Greek friezes — the sort of two-dimensional work that looks three-dimensional with surgeon’s scalpels on wood. “It was so time-consuming, I started wondering how to save time,” Will said — which led him to the possibility of the CNC.
Initially, he was looking at computer-numerically controlled routers as an option for quickly hogging out the backgrounds of his carvings. “Then I realized it could actually be used a carving tool,” he said. “I can design things I would never have thought of designing before, because now I know can make them happen. If you did them by hand, it would take hundreds and hundreds of hours, and it wouldn’t even be done well.”
For instance, lately he’s been working with Celtic interlacing patterns. He’s also had the opportunity to create a relief carving of a Giant Pacific Octopus, even accompanying a scientific expedition to Alaska as their official artist as they studied octopuses, and handling them (with permission) at the Monterey, California, aquarium “to become familiar with what octopuses are like, how they move and so forth. For some reason, I’ve always been fascinated by octopuses.”
In order to accomplish such projects on the CNC, Will taught himself how to program computers so he could program the information for his carvings. Although he’s keeping his particular method proprietary, he feels his ability to figure it out has a lot to do with his art training, and his ability to look at figures in a non-Western perspective. “At this point, I’m mostly using the CNC. I do some work by hand, but it’s 99 percent CNC.”
The CNC carving also allows him to carve intricate textured surfaces that blend into each other. Some of these textures, he said, are only about 3/1,000ths of an inch deep. Although they don’t show up well in photographs, “you can feel it with the fingers,” Will said, and, in person, the light plays over them similar to the way it does with shot silk fabric: “As you walk around, the patterns change — on the whole surface, patterns ripple, like water as it runs down over rocks. That’s fascinating to me.”
Will uses hard woods — rock maple, cherry, bay laurel, etc. — for these carvings because they take the detail better, but his personal wood preferences relate more to the color of the wood: he prefers species with more of a natural brown cast to them rather than yellow or red — species like, for example, American elm or his favorite wood, golden narra.
As you could probably guess from his wood preferences, he also prefers finishes that let the natural color of the wood show through — occasionally urethane, but frequently Renaissance Wax. “It works really great without changing the color.”
As for the woods he puts these finishes on, Will said he has “thousands of board feet of interesting wood. I have a couple of warehouses full of wood: I’ve been buying for two decades.” He has worked closely with a wood importer who gave him first choice, and “I spent a summer one year wandering around Washington and Oregon, meeting people with sawmills back in the forest, developing a network of people to get wood from.”
Among that stored wood are some walnut trees Will bought about 10 years ago and had milled to his specifications, so that he would have wood with matching grain for his eventual room project.
Of course, right now, he’s working on CNC relief carvings, high-end sculptural furniture — and carving graphite molds in which he and a friend cast transparent glass.